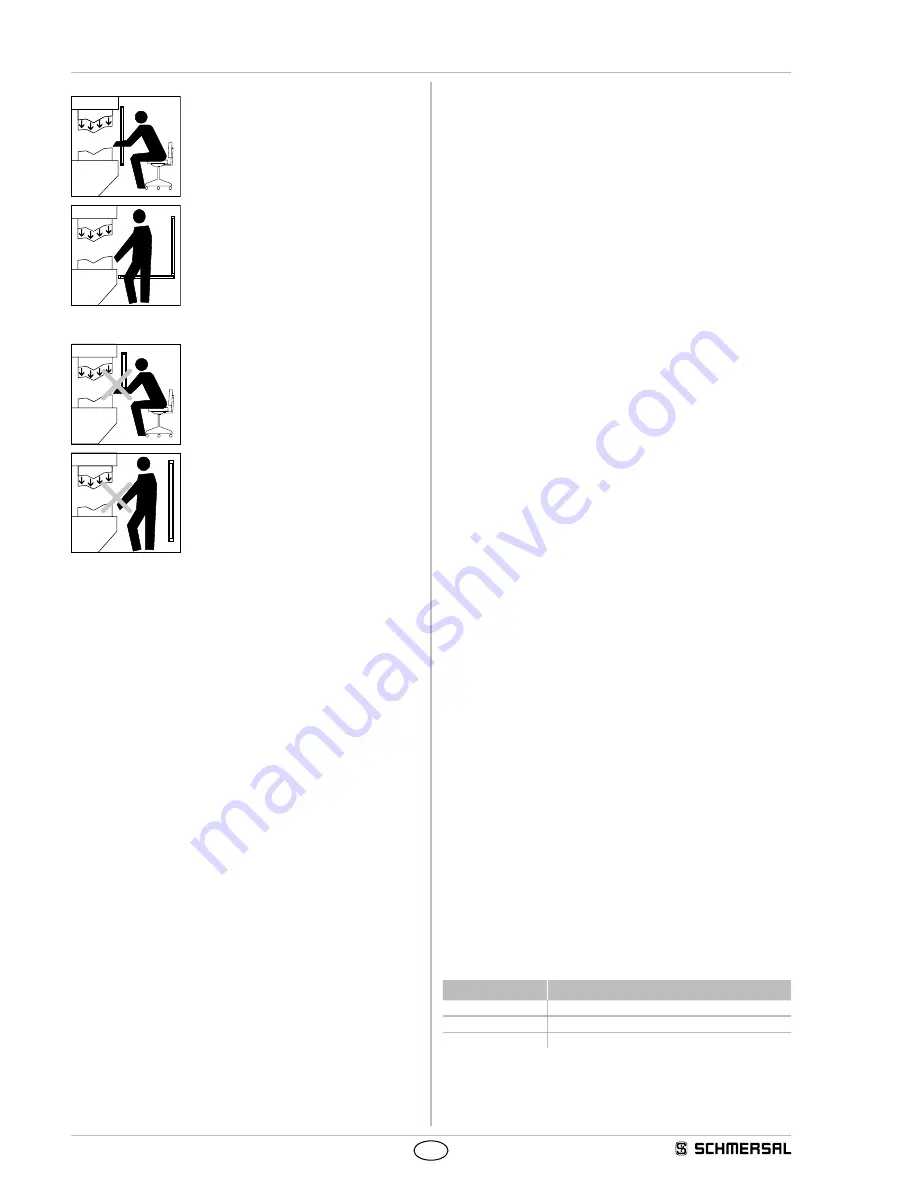
8
Operating instructions
Safety light curtain/safety light grid
SLC 420
SLG 420
EN
Correct installation
Hazardous machine parts can only be reached
after passing through the protection field
Persons between the protection field and
hazardous machine parts must be prevented
(protection against stepping over)
Unauthorised installation
Hazardous machine parts can be reached
without passing through the protection field
Persons between the protection field and
hazardous machine parts is enabled
3.3 Alignment
Procedure in automatic operating mode:
1 The transmitter and the receiver must be fitted parallel to each other
and at the same height
2 Turn the transmitter and monitor the diagnostic window of the
receiver Fix the light curtain, when the LED OSSD ON (green) is on
and the LED signal reception (orange) is off
3 Determine the max rotating angle to the left and to the right, at which
the LED OSSD ON (green) is on and tighten the mounting screws in
central position Make sure that the LED signal reception (orange) is
not on or flashing
3.4 Setting mode
The alignment of the sensors is carried out using the setting mode
Activating setting mode
If +24 V is on the input (pin 1, receiver) "Release restart interlock" at
system start for at least two seconds (by pressing the button restart),
the system changes over to the setting mode of operation
The signal strength at the receiver is indicated with the signal strength
LED (colour orange) through light pulses The better the alignment, the
higher the frequency of the light pulses The alignment is optimal when
the light pulses switch over to continuous light
If there is no optical synchronisation between the transmitter and the
receiver, a light pulse is emitted every 3 seconds The setting mode is
ended by a system start ( +UB OFF/ON)
Additional signalling with the SLG 420 by the status light
In this mode the signal strength of the beam is signalled to the status
indicator with the lowest value through light pulses (colour yellow)
The better the alignment, the higher the frequency of the light
pulses The alignment is correct when the light pulses switch over to
continuous light
3.5 Safety distance
The safety distance is the minimum distance between the protection
field of the safety light curtain and the hazardous area The safety
distance must be observed to ensure that the hazardous area cannot
be reached before the hazardous movement has come to standstill
Calculation of the safety distance to EN ISO 13855
The safety distance depends on the following elements:
• Stopping time of the machine (calculation by run-on time
measurement)
• Response time of the machine and the safety light curtain and the
downstream relay (entire safety guard)
• Approach speed
• Resolution of the safety light curtain
• Vertical or horizontal installation
Safety light curtain SLC 420
The safety distance for resolutions 14 mm up to 40 mm (vertical
installation) is calculated by means of the following formula:
(1) S = K x T + C [mm]
S = Safety distance [mm]
K = Approach speed 2000 mm/s
T = Total reaction time (machine run-on time, reaction time of the safety
guard, relays, etc)
d = Resolution of the safety light curtain
C = additional distance depending on the resolution,
C = 8 (d - 14) [mm]
If value S <= 500 mm after the calculation of the safety distance, then
use this value
If the value S >= 500 mm then redetermine the distance S using an
approach speed K of 1600 mm/s:
(2) S = 1600 mm/s * T + 8 (d - 14) [mm]
If the new value S > 500 mm, use this value as safety distance
If the new value S
<
500 mm, use a minimum distance of
S = 500 mm
Example:
Reaction time of the safety light curtain = 10 ms
Resolution of the safety light curtain = 14 mm
Stopping time of the machine = 330 ms
S = 2000 mm/s * (330 ms + 10 ms) + 8(14 mm - 14 mm)
S = 680 mm
S = > 500 mm, therefore new calculation with K = 1600 mm/s
S = 544 mm
Calculation of the safety distance for SLG 420 and SLC 420 with a
resolution d > 40 mm
(3) S = ( 1600 mm/s * T ) + 850 mm
S = Safety distance [mm]
T = Stopping time of the m reaction time of the
safety light curtain
K = Approach speed 1600 mm/s
C = Additional distance 850 mm
The following mounting heights must be observed:
Number of beams Mounting height above reference level in mm
2
400, 900
3
300, 700, 1100
4
300, 600, 9001200