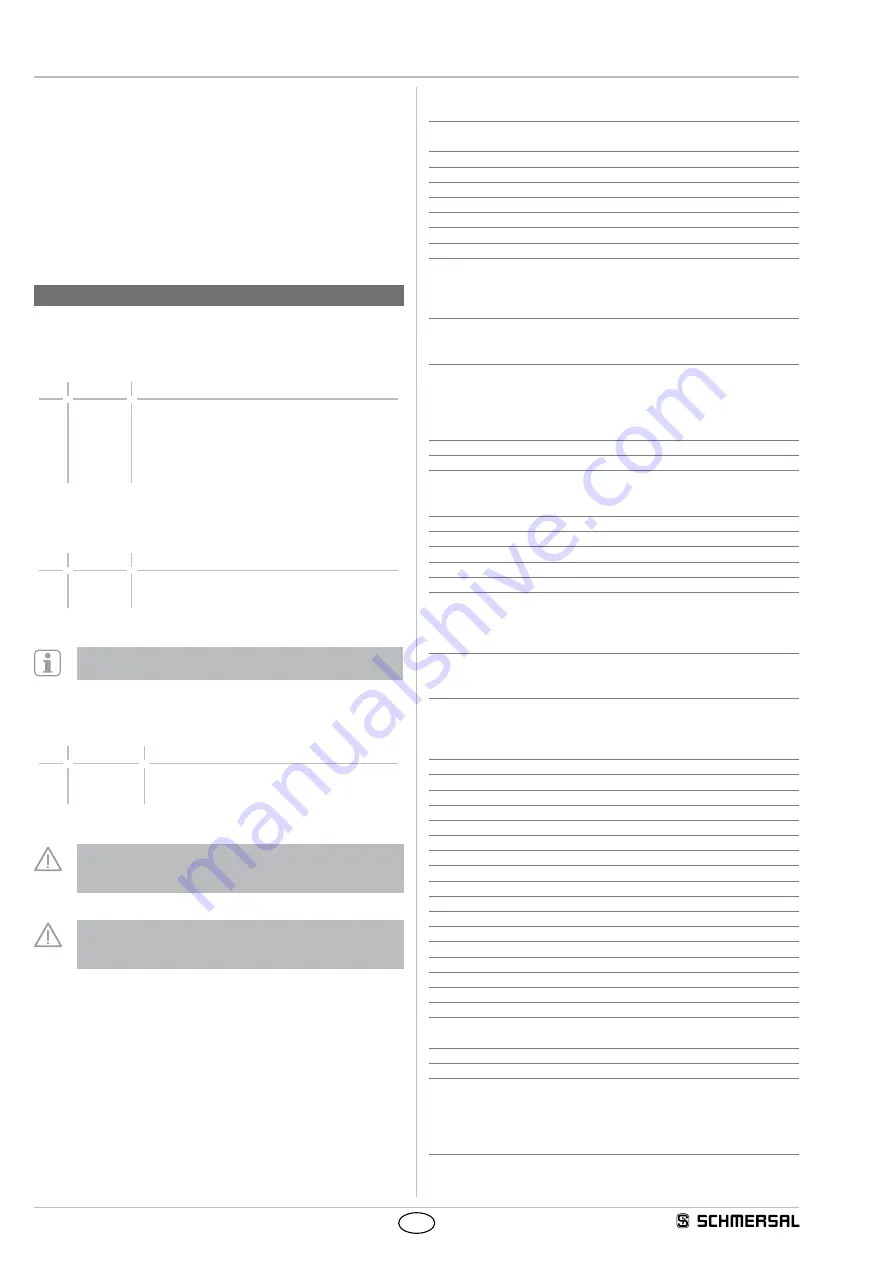
2
Operating instructions
Emergency stop command device
EDRRS40...
EN
1.7 Exclusion of liability
We shall accept no liability for damages and malfunctions resulting from
defective mounting or failure to comply with this operating instructions
manual. The manufacturer shall accept no liability for damages
resulting from the use of unauthorised spare parts or accessories.
For safety reasons, invasive work on the device as well as arbitrary
repairs, conversions and modifications to the device are strictly
forbidden; the manufacturer shall accept no liability for damages
resulting from such invasive work, arbitrary repairs, conversions and/or
modifications to the device.
2. Product description
2.1 Ordering code
This operating instructions manual applies to the following types:
EDR
➀
40
➁➂
Operating element
No. Option
Description
➀
RS
with cylinder lock, unlocking only by key and
pulling (EFR required)
➁
Mounting hole 22,3 mm
VH
Mounting hole 30,5 mm
➂
RT
Lock with red lid
In combination with the following contact variants:
EF
➀
…
Contact element
No. Option
Description
➀
303
1 NC / 1 NO
220
2 NC / 0 NO
For more information about contact versions, see section 4.2.
and the following spring elements:
EFR.
➀
Spring element
No. Option
Description
➀
without earth connection
EDRRS
with earth connection
When the EFR is used, the electrical connection in the PELV
(extra-low voltage) must be executed in accordance with
EN 60204-1.
By observing the information described in this operating
instructions manual, the safety function and therefore the
compliance with the Machinery Directive will be maintained.
2.2 Special versions
For special versions, which are not listed in the order code below 2.1,
these specifications apply accordingly, provided that they correspond
to the standard version.
2.3 Purpose
The EDRRS series of emergency stop command devices are designed
for use in emergency stop circuits to ISO 13850.
2.4 Technical data
Pushbutton:
Standards:
ISO 13850; IEC 60947-5-1;
IEC 60947-5-5; IEC 60947-1
Design:
emergency stop pushbutton with latching - front plate mounting
Unlocking:
by key and pull release
External snap-action mechanism:
yes, through EFR
Fully insulated:
No
Protection class IP:
IP65
Mechanical life:
100,000 operations
Actuating force:
approx. 25 N
Material:
- Material of the operating unit:
anodised aluminium /
chrome-plated brass
- Material of the front ring:
anodised aluminium
Colours
- Operating unit colour:
red / silver
- Front ring colour:
silver
Dimensions:
- Height:
29 mm (without key)
- Diameter of the operating button:
39 mm
- Hole diameter:
22.3 mm + 0.4 mm
- Form:
round
Fixing:
with mounting flange ELM
Tightening torque for the fixing screws:
0.6 Nm
Front plate thickness:
- min. front plate thickness:
1 mm
- max. front plate thickness:
6 mm
Grid dimensions:
50 mm x 40 mm
Mounting position:
random
Ambient temperature:
−25 °C … + 75 °C
Contact element EF:
Standards:
IEC 60947-1; IEC 60947-5-1
Material:
- Material of the enclosure:
plastic, glass-fibre reinforced
thermoplastic, self-extinguishing
- Material of the contacts:
fine silver, spring bronze or brass carrier
Utilisation category:
AC-15: 250V / 8 A
DC-13: 24 V / 5 A
(only in case of fully insulated device head)
Application:
When an EDRRS... with EFR is used,
the electrical connection in the PELV
(extra-low voltage) must be
executed according to DIN EN 60204-1.
Rated insulation voltage U
i
:
400 V
Rated impulse withstand voltage U
imp
:
4 kV
Degree of pollution:
3
Overvoltage category:
III
Suitable low voltage:
≥ 5 VDC / 3.2 mA
Thermal test current I
the
:
10 A
Max. fuse rating:
gG 10 A
Climatic resistance:
to EN 60068 part 2-30
Ambient temperature:
−25 °C … +60 °C
Switch travel:
depending on the contact execution
Positive break travel:
2 mm
Test voltage enclosed:
2500 VAC
Actuating force at stroke end:
approx. 8 - 15 N
Switching frequency:
1200 s/h
Mechanical life:
10,000,000 operations
Bounce duration (100 mm/s):
< 5 ms
Restistance to shock:
110 g / 4 ms - 30 g / 18 ms, no bouncing
Shock resistance:
> 20 g / 10 … 200 Hz (for actuating heads with
higher mass accordingly lower)
Contact force:
0.5 N each contact point = 2 N each contact bridge
Wiring configuration:
to IEC 60947-1
Termination:
screw connection,
flat plug-in connector,
Cage-Clamp connection
(in case of a Cage Clamp connection, the contact
elements can not be additionally secured against loosening)