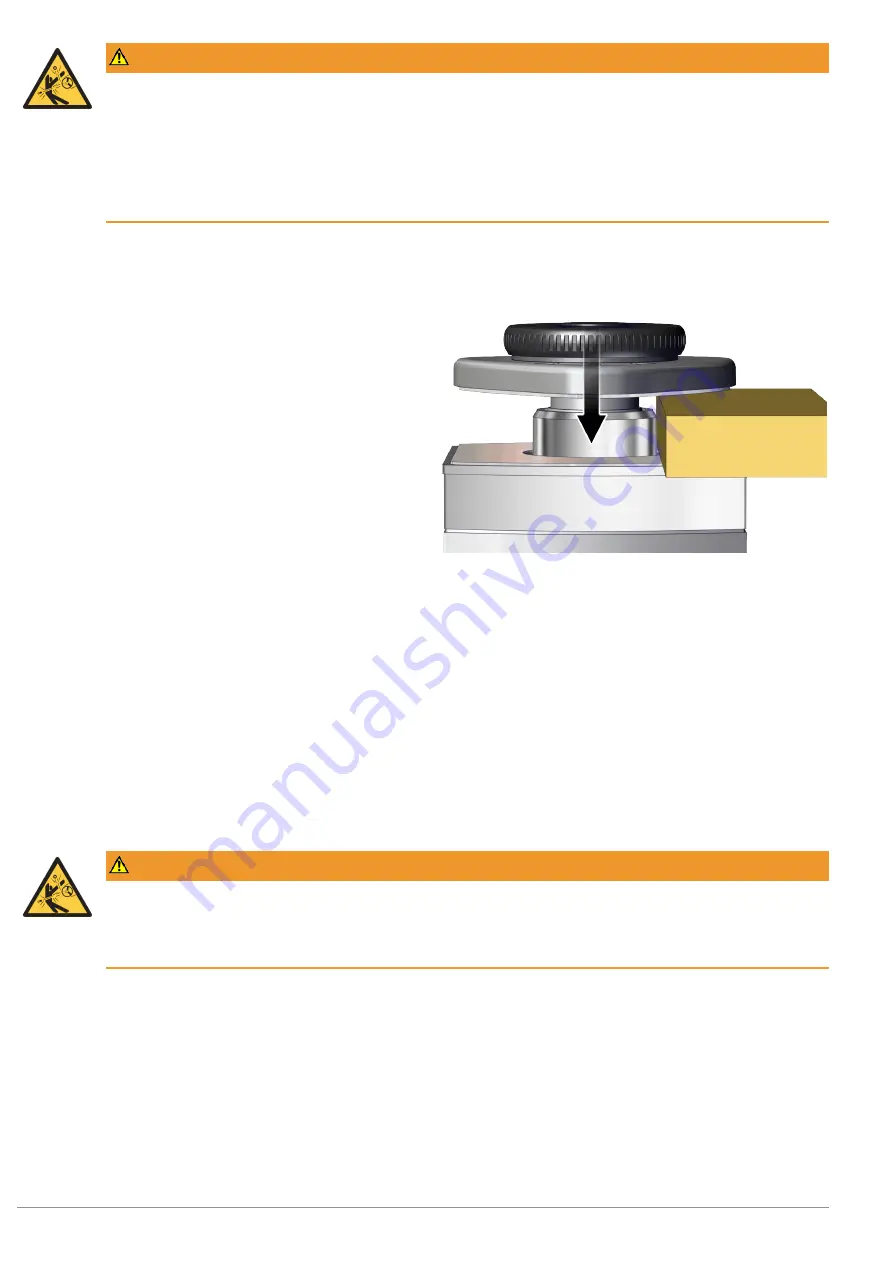
WARNING
Flying workpiece due to insufficient clamping force during processing resulting from incor-
rect setting of the clamping height.
Risk of injury due to flying workpiece
4
Adjust the clamping height such that the VCMC uses its maximum clamping force. While doing
so, ensure that the lifting force of the VCMC is less than or equal to 6 mm.
4
Personal protective clothing must be worn.
ü
The locking disc must be entirely closed.
ü
The workpiece is set.
1. Evacuate the appropriate vacuum circuit on the
grid table via the higher-level machine.
ð
The VCMC is clamped to the grid table and the
workpiece is clamped by lowering the clamping
disc (
≤
6 mm).
2. Carry out both a visual and manual check to make
sure that the workpiece is securely clamped by
pulling on the workpiece.
ð
If the workpiece can be moved, then it is not sufficiently tightly clamped. Check the clamping height and ad-
just it if necessary.
ð
If the clamping is sufficient, then machining of the workpiece may commence.
7.2 Machining Limitations
WARNING
The workpiece comes loose during machining and is flung away by the machine.
Risk of injury from flying parts.
4
Ascertain the maximum machining parameters and observe them.
The clamping force is limited, meaning that it can withstand machining forces only up to a certain point. Accord-
ingly, the operator of the mechanical clamp is obligated to establish for themselves (by experiment, slowly and
carefully increasing the machining forces) the optimal settings and number of mechanical clamps necessary to en-
sure that the workpiece does not slip or even come loose during the machining process.
Schmalz assumes no liability for damages resulting from slippage or release of workpieces due to faulty adjustment
of machining parameters.
14 / 15
EN-US · 30.30.01.03049 · 00 · 10/21