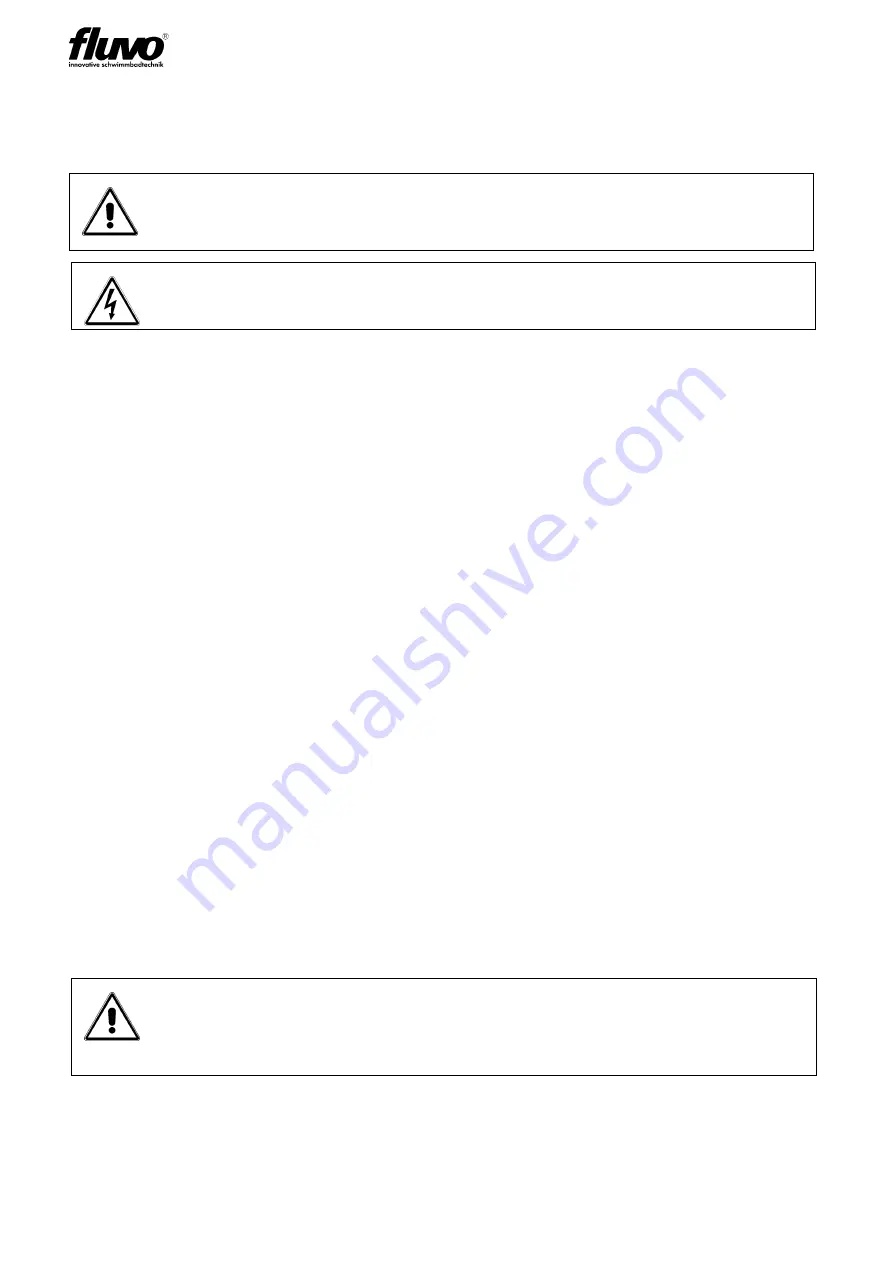
OPERATOR‘S MANUAL
4
NT2 rondo
Version: 27211 -
F
Schmalenberger GmbH + Co. KG
D-72072 Tübingen / Germany
2.2
Symbols
In these operating instructions the following symbols are used to draw your special atten-
tion to dangers:
Notices attached directly to the counter-current system , e.g. the arrow indicating the direc-
tion of rotation, must always be observed and maintained in a clearly legible condition.
2.3
Safety Instructions for the Operator
1. Electrical equipment must be installed and maintained by qualified electricians. The ap-
propriate local safety requirements and installation regulations must be observed. The
expression “qualified person” is defined in VDE 0105 and IEC 364 There is no informa-
tion contained in this operator’s manual for unqualified persons. It must be pointed out
that EU regulations prohibit the use of unqualified persons on electrical systems.
2. The details on the type plate must correspond to the electrical supply being connected
to.
3. The counter-current system may only be operated using an earth leakage circuit brea-
ker.
4. Under no circumstances must there be any conducting connection between the metal
parts of the motor and the water.
5. If the counter-current system is built into a pump pit then it must be ensured that there
is enough ventilation (for cooling the motor) and enough drainage facility for leaked wa-
ter (at least DN 40).
6. Prior to carrying out repairs to the counter-current system it must be isolated from the
electrical supply and protected from unintentional switching on.
7. Regardless of what nature they may be, repairs must only be carried out by qualified
persons and the counter-current system must be emptied first.
8. The operator must ensure that
- the operator’s manual is always available for users to read,
- instructions in the operator’s manual are being observed,
- the counter-current system is immediately stopped if abnormal electrical voltages,
temperatures, noises, vibrations, leakages or other faults should arise.
Warning! Danger of injury! / Warning! Risk of damage!
This symbol warns you of dangers through mechanical effects and also warns
of handling that could damage the product.
Warning! Mortal danger!
This sign warns you of the danger from electric shocks.
9. Persons who are likely to be endangered by radio waves (e.g. wearers of
heart pace makers) should not linger close to this counter-current swim-
ming system with radio control. In such cases it is recommended to employ
some other form of control (external or pneumatic).