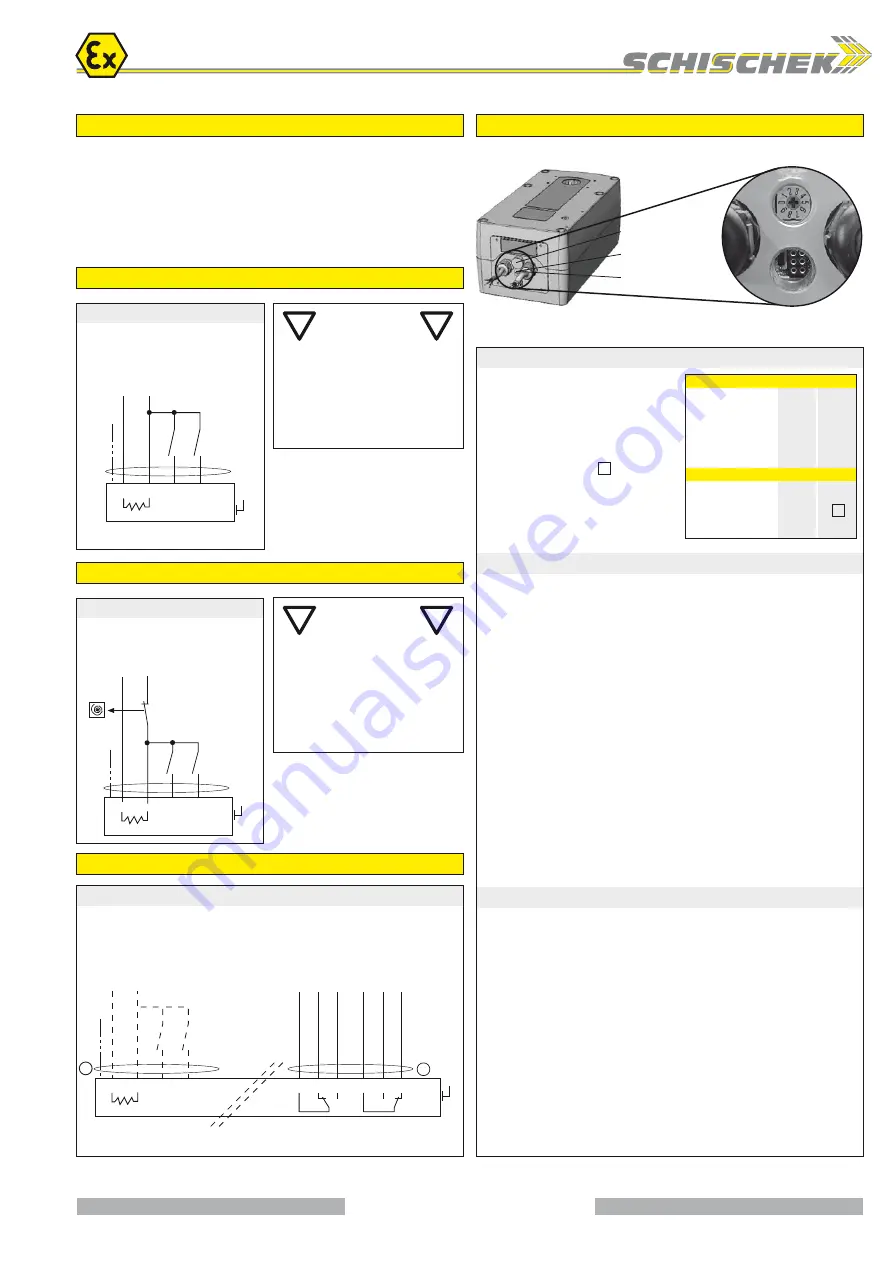
www.schischek.com
Schischek GmbH Germany, Mühlsteig 45, Gewerbegebiet Süd 5, 90579 Langenzenn, Tel. +49 (0)9101 9081-0, Fax +49 (0)9101 9081-77, E-Mail [email protected]
E X P L O S I O N P R O O F
S
T
10-position switch (S)
Push button (T)
3-colour LED
Switch – Push button – Lamp for adjustment, behind the blancking plug
SB 1.0
SB 1.1
SB 3.5
B
A
Example: ExMax-50.75
Requested parameter:
Torque 75 Nm
Running time motor 90 sec/90°
Result: switch position (S) 07
Parameter selection
1
2
3
4
~
-
~
+
PE
heater
Type
Torques
ExMax- 50.75
50 Nm 75 Nm
ExMax- 100
100 Nm
ExMax- 150
150 Nm
ExMax- 30-F
30 Nm
ExMax- 50-F
50 Nm
ExMax- 60-F
60 Nm
Running times Position of switch S
40 sec./90°
00 05
60 sec./90°
01 06
90 sec./90°
02 07
120 sec./90°
03 08
150 sec./90°
04 09
Wiring of integral aux. switches
1
2
3
4
~
-
~
+
PE
heater
1 2
Integral aux. switches
potential free contacts
switching at 5° and 85°
Angle of rotation
max. 24 V/1 A, 240 V/0,25 A
< 5 °
3
4 5
> 85 °
6
Wiring of the actuator in acc. with
actuator type, see wiring diagrams 1.0/1 .1
Additional wiring of the integral aux. switches
1
2
3
4
~
-
~
+
24 to 240 VAC/DC
PE
heater
24 to 240 VAC/DC
24 to 240 VAC/DC
a
b
a
b
If 40 sec. or 60 sec. mode is selected,
the self adjustment of angle of rotation
must be started.
Attention
!
!
If 40 sec. or 60 sec. mode is selected
for motor and/or spring return, the self
adjustment of angle of rotation must be
started.
Never use actuators in this mode
without external torque/force.
Attention!
!
!
PA
PA
PA
A) Self adjustment of Angle of rotation:
Switch (S) into position 02 (low torque) or 07 (high torque), then push button (T) for
minimum 3 seconds. The actuator will drive into both end positions to be adjusted.
LED indicates green.
Adjusmtent time needs approx. 180 sec. (90 sec. On, 90 sec. Off). After that, switch
S into position 00-09 in acc. with your required torque and running time.
B) Selection of running time and torque:
Put switch (S) into the correct/selected position in acc. to above table.
The selected parameter will work at next operation of the actuator.
Adjustment can be done even without supply voltage. If supply voltage is available
turn switch only if actuator is not running.
C) Additional information for 3-pos operation:
a closed, b open = direction I
b closed, a open = direction II
a and b closed = Motor doesn't work
a and b opened = Motor doesn't work
Direction (I and II) depends on left/right mounting of the actuator to the damper/valve.
You can change direction of the motor by changing electrical wiring terminal 3 and 4.
See extra information „EL-M“
Error indication
Function, adjustment and parameter
Wiring diagram ExMax-.... (without spring)
Wiring diagram ExMax-..-F (with spring return)
Parameter, Adjustment – Failure indication
Wiring diagram type ExMax-...-M with integral aux. switches
ExMax actuators are equipped with a universal supply unit working at a voltage range from
24 to 240 VAC/DC
.
The supply unit is self adjustable to the connected voltage!
The safety operation of the spring return function works if the supply voltage is cut. For
electrical connection inside hazardous locations an explosion proof junction box is required.
For permanently connected equipment is an external 5 A (time lag) circuit-breaker in the
control cabinet required.
Electrical connection
ExMax-50…150 ExMax-30…60-F
Special makes
ExMax-…-S/SF
ExMax-…-CTM