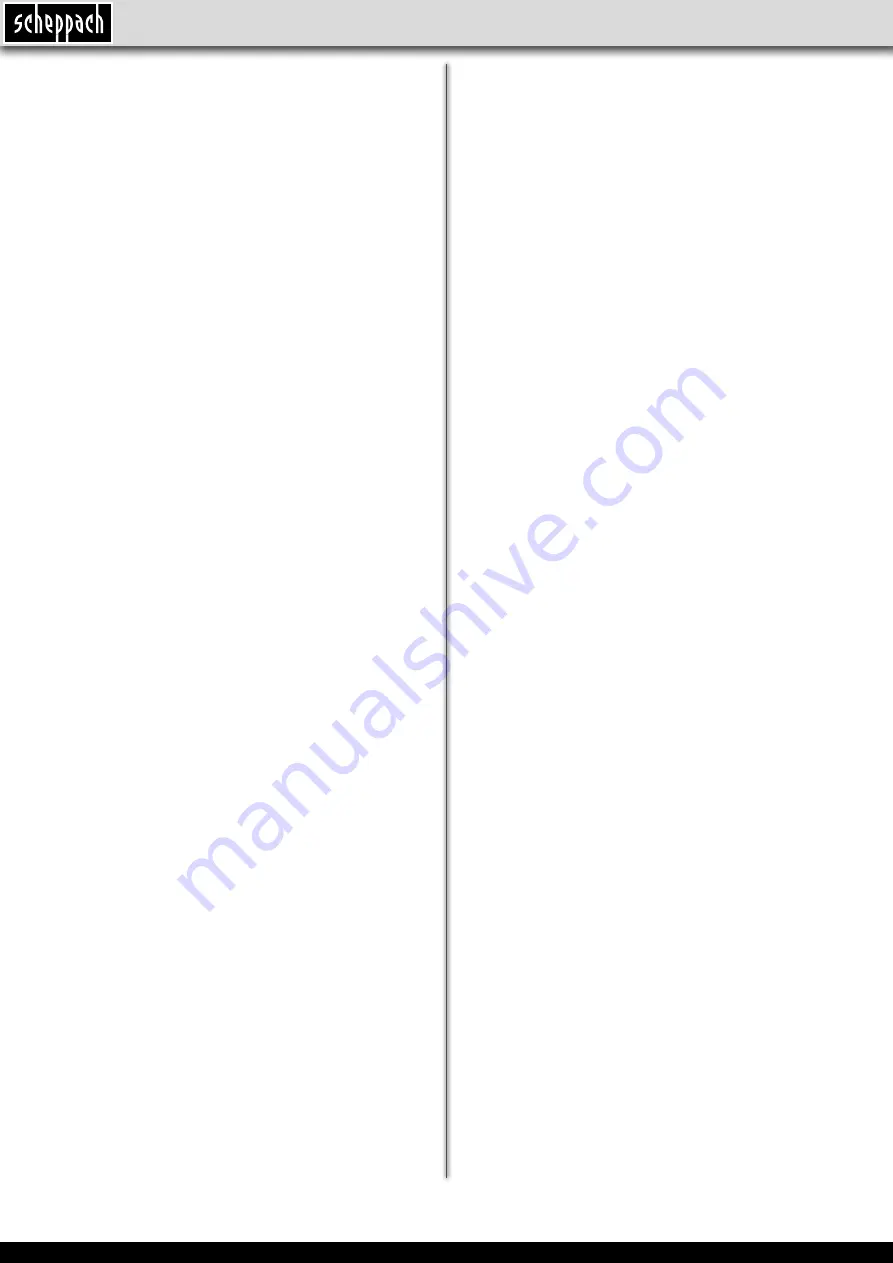
www.scheppach.com
+(49)-08223-4002-99
+(49)-08223-4002-58
26 І 36
4. The small black adjusting screws are used to align the
guide rail (G) so that the rip fence (20) is parallel with
the blade (3) no matter where it is along the length of
the rail.
Fig. 13, 14
1.
Now take the first of the extension tables (18), loosen
the nuts and bolts and slide it onto the guide rails
(F+G).
2. Follow it with the second one (18) and tighten all the
locking nuts and bolts. If the tables (18) do not slide
into place easily, check that the front (G) and back
guide rails (F) are really parallel and adjust the rear
one (F) if necessary.
3.
Do not move the front rail (G) or you will upset the
alignment of the rip fence (20).
Fig. 15
1.
Slide the holder for suction hose clip (6) onto the rear
guide rail (F) and lock it into place.
2. Fit the suction hose (5) to the saw blade guard (4) and
the spigot on the rear extraction point. Secure in place
with the two hose clamps provided.
3.
Clip the suction hose (5) into the holder for suction
hose (6) to hold it clear of the table.
4. It is strongly recommended you use a dust ex-
tractor at all times, by connecting a hose to the
100mm outlet.
5. Failure to use an extractor will require stopping
the machine regularly to clean out of the internal
parts of the extraction hood, to avoid causing
damage.
Fig. 16, 17
1. Fit the two support brackets (A) which will carry the
guide rail(10) for the sliding table (12).
2. These are bolted to the left hand side of the table with
four countersunk bolts. Fitf the wide guide rail extru-
sion by sliding it over the heads of the eight securing
bolts.
3.
Position the sliding table guide rail (10) so that the
back edge of the rail (10) is level with the back side
of the rear guide rail (F). Ensure the guide rail (10)
is parallel to the saw blade (3) before tightening the
eight nuts.
Fig. 14, 18
1.
Before fitting the sliding table (12) it should be noted
that the two outboard bearing wheels are mounted on
eccentrics.
2. Should it ever be necessary their position can be
adjusted with the aid of a 14mm spanner.
Fig. 20
1.
The guide rail (10) is fittted with front and rear travel
stops.
2. Move the rear travel stop to the back of the slot.
3. Remove the front stop completely and fit the sliding
table (12) onto the guide rail (10) so that the four bea-
ring guides are located in the matching grooves along
the sides of the rail (10).
4. Replace the front stop.
Fig. 21
1. Check the sliding table (12) is level to the main
table. It should also be slightly higher (up to 1mm)
than the main table (1) to allow a clamped work
piece to move across the main table.
2. If necessary, loosen and adjust the four silver
support brackets (A) to lift or level the sliding table
(12).
Attachment
Important. Pull out the power plug before carrying
out any maintenance, resetting or assembly work on
the circular saw!
Place all parts supplied on a flat surface. Grouping
equal parts.
Insert screws each from outside to inside. Secure con-
nections with nuts on the inside.
Note:
Tighten the nuts and bolts during assembly only
to the extent that they can not fall down.
If you tighten the nuts and bolts prior to final assembly,
final assembly can not be performed.
Mounting of the Stands (Fig.6)
1. Lay the machine together with another person on the
side.
2. Mount the for stands (14) to the frame of the saw. Use
an Open-end-wrench (size 17 mm)
3.
Put up the machine together with another
person.
Mounting of the handwheel for angle adjustment
(Fig.7)
1.
Plug the hand wheel for angle adjustment (16) to the
connection at the side of the machine.
2.
Tighten the hand wheel (16) with an Allen key (3 mm)
at the connection.
3. Raise the saw blade by turning fitted hand wheel (15)
at the front of the machine clockwise.
4. Turn the wheel clockwise until the blade is vertical, if it
is not already in this position.
Mounting of the Guide Profiles (Fig.8-10)
1. Loose the hexagon screws at the 4 brackets (H)
(Front + Back)
2.
Push the both guide profiles (F+G) on the hexagon
screws at the brackets (H)
3. Push the guide profiles (F+G) towards to the adjust
screws (I).
4. Tighten the hexagon bolts by hand.
Fig. 11
1. The
front guide profile (G) with
the measuring scale
(17) should be fitted to the front of the table, scale
uppermost and in both cases the open side should
face outwards.
2.
If they are difficult to slide on, make sure that you
have slackened the nuts sufficiently and rock the
extrusions gently as you move them along.
3.
You may need to reach round to the back of the bra-
ckets (19) and unscrew the black adjusters a little, if
they are binding on the aluminium.
4. Join the two parts of the clamp for rip fence (19) using
one cap head setscrew (J) and one hex head bolt (K).
Fig. 11
5. Place the rip fence (20) over front guide rail (G), so
the lip of the clamp of rip fence (19) sits behind the
rail.
Fig. 12
1. Position the rip fence (20) parrallel to and up against
the saw blade (3).
2. Whilst holding it in that position, adjust the guide rail
(G) to align the 0cm on the measuring scale (17) with
the left hand edge of the clamp for rip fence (19).
3.
Having done this you can tighten up the 4 nuts on the
support brackets (A) underneath, locking the guide rail
(G)in place
Summary of Contents for 5901309903
Page 8: ...www scheppach com service scheppach com 49 08223 4002 99 49 08223 4002 58 28 29 8 36 30...
Page 9: ...www scheppach com service scheppach com 49 08223 4002 99 49 08223 4002 58 9 36...
Page 20: ...www scheppach com service scheppach com 49 08223 4002 99 49 08223 4002 58 20 36...
Page 30: ...www scheppach com service scheppach com 49 08223 4002 99 49 08223 4002 58 30 36...
Page 31: ...www scheppach com service scheppach com 49 08223 4002 99 49 08223 4002 58 31 36...
Page 32: ...www scheppach com service scheppach com 49 08223 4002 99 49 08223 4002 58 32 36...
Page 33: ...www scheppach com service scheppach com 49 08223 4002 99 49 08223 4002 58 33 36...