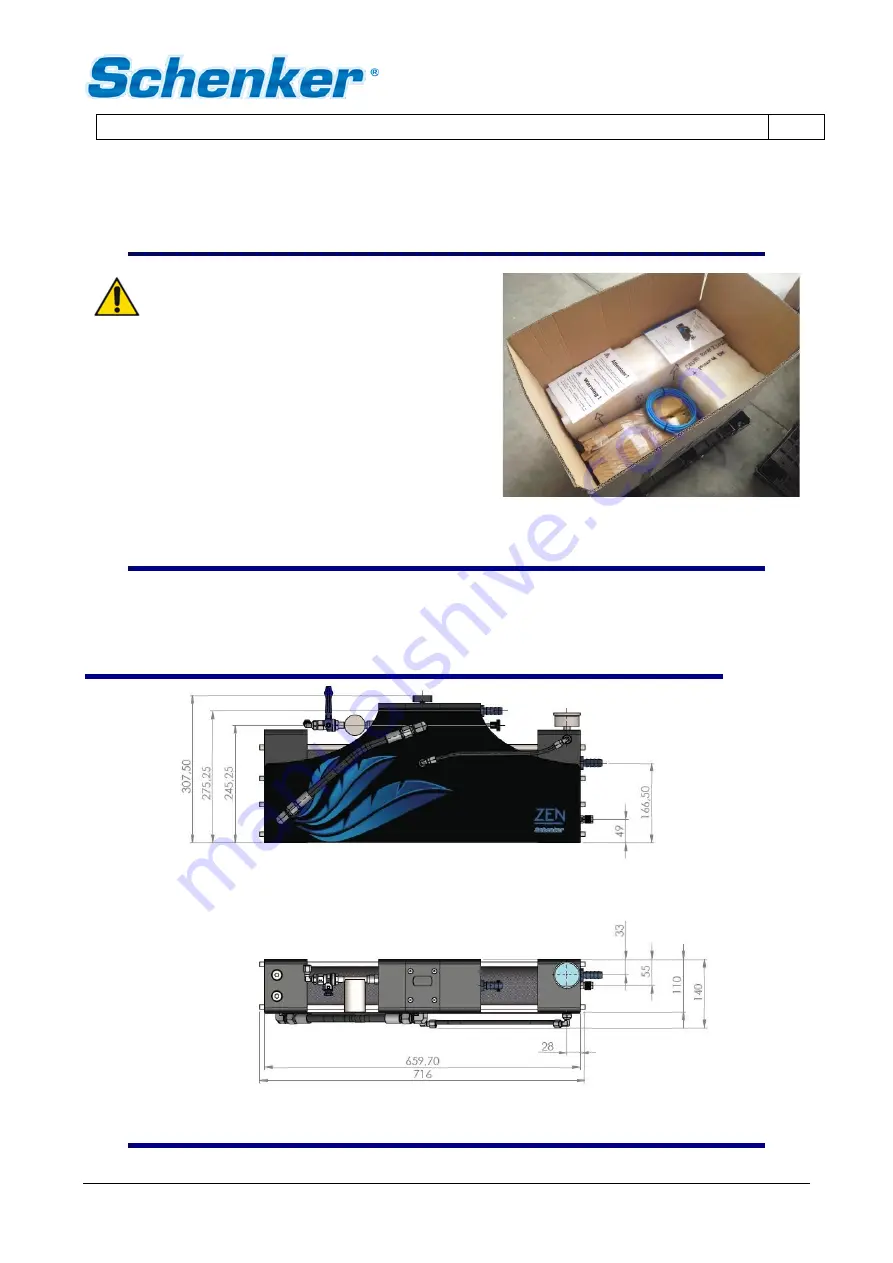
3
– PRESENTATION OF THE PRODUCT COD.
30Z12/24.B.2021
EN
THE PRESENT MANUAL BELONGS TO -
Schenker Italia
- ALL RIGHTS RESERVED
10
3.4 Attached documents
The package contains the technical documentation (use and maintenance manual, electric and hydraulic
scheme, warnings and instructions).
ATTENTION
•
Read carefully the use and maintenance
manual before installing the system.
•
Use only recommended material for the
installation (especially hoses, fittings and
seals) in accordance with the manual.
•
Do not store the unit under temperature
below 5°C and above 45 °C
DOCUMENTS INCLUDED IN THE PACKAGING
FIG. 3-3
3.5 Technical data
WATERMAKER
WATERMAKER DIMENSIONS
FIG. 3-4