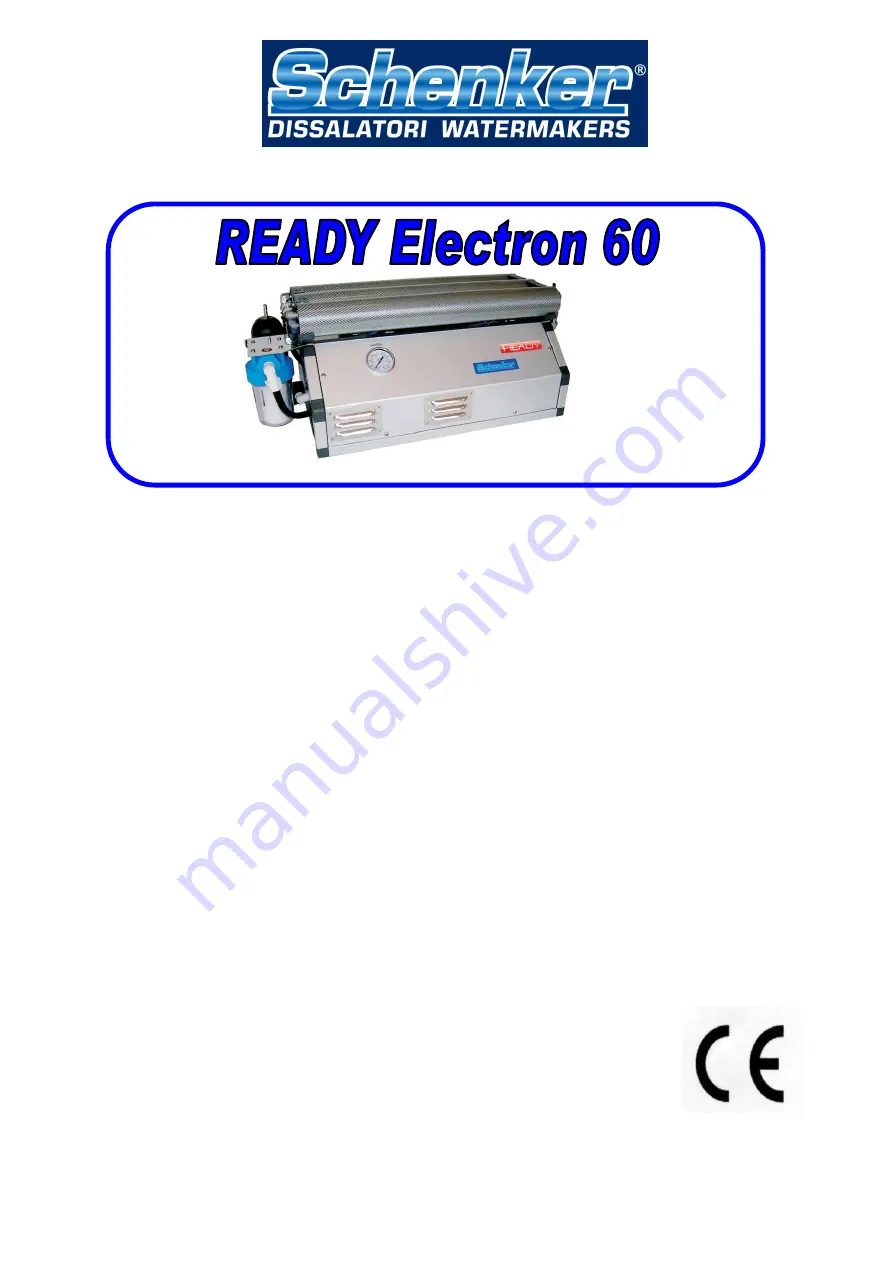
1
OPERATION AND MAINTENANCE MANUAL
1.
Introduction
1.1.
General
1.2.
Technical data
1.3.
System description
2.
Installation
2.1.
General criteria and material required
2.2.
Components mounting
2.3.
Water intake
2.4.
Hydraulic connections
2.5.
Hydraulic diagram
2.6.
Electric connections
3.
Operating procedures
3.1. By-pass activation
3.2.
First start-up procedure
3.3.
Normal operating procedure
4.
Maintenance
4.1.
Shutdown procedure
4.2.
Maintenance and recurrent inspections
4.3.
Troubleshooting
5. Safety cautions
6. Most frequent operations summary table
7. Warranty
Rev. 2004