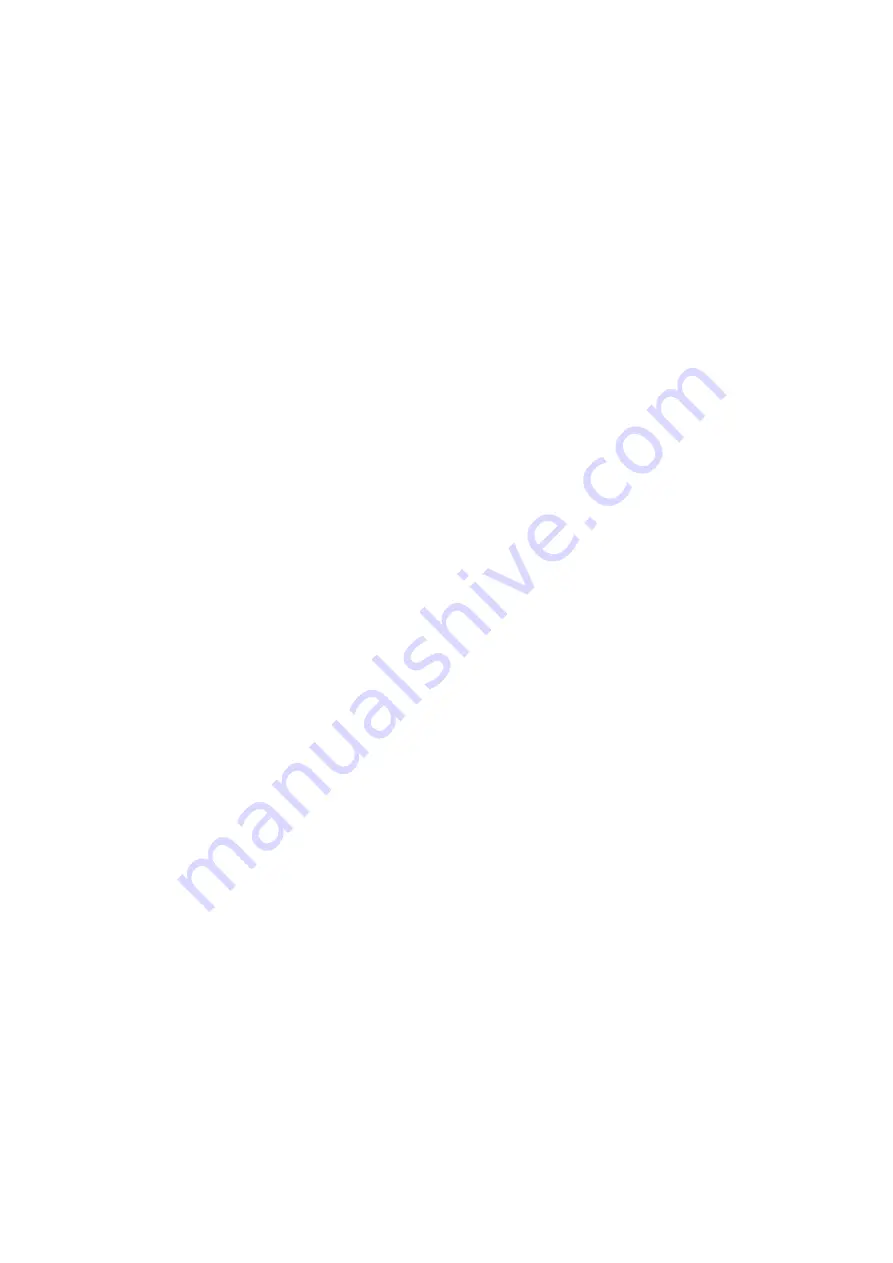
Calibration Procedure:
ACT_wCON
Active sensor with calibration control
0% LOAD
unload sensor
100%Con
after pressing ENTER the calibration takes place automatically.
SAVE
query for takeover of calibration data
ACT_nCON
Active sensor without calibration control
0% LOAD
unload sensor
100%Con
calibration by 100 % load (apply the nominal load/nominal torque) or switch to nominal
value
NOMVALUE
enter the nominal value in mV/V or switch to 100 % load
SAVE
query for takeover of calibration data
PAS_wCON
Passive sensor with calibration control
0%LOAD
unload
sensor
100%Con
after pressing ENTER the calibration takes place automatically.
SAVE
query for takeover of calibration data
PAS_nCON
Passive sensor without calibration control
0% LOAD
unload sensor
100% LOAD
calibration by 100 % load (apply the nominal load/nominal torque) or switch to nominal
value
NOMVALUE
enter the nominal value in mV/V or switch to 100 % load
SAVE
query for takeover of calibration data
CURRENT
Sensor with 4 - 20mA
0% LOAD
unload sensor
100% LOAD
calibration by 100 % load (apply the nominal load/nominal torque) or switch to nominal
value
or
NOMVALUE
fixed value 4-20 mA
SAVE
query for takeover of calibration data
Edit and Adjust Limit Values
In menu 2 SYSTEM - 2,9 INPUT - Setpoint the limit value parameters can be adjusted. If menu LIMIT VALUE SETS is
selected and confirmed by ENTER, the limit values are listed. Switch to the next limit value with the PLUS key. With the
MINUS key the switching level HI or LO can be selected.
Definition of the switching levels:
HI... if the measured value exceeds the SP, the output will be switched on.
if the measured value falls below the point of hysteresis, the output will be switched off.
LO.. if the measured value exceeds the SP, the output will be switched off.
if the measured value falls below the point of hysteresis, the output will be switched on.
The adjusted level is taken over by pressing ENTER. If ENTER was pressed, the SP can still be edited. With the keys PLUS
and/or MINUS the leading sign and the digits can be adjusted. Jump to the next digit with ENTER. By confirming with
ENTER the new adjusted SP is accepted; with ESC the new adjusted SP gets discarded.