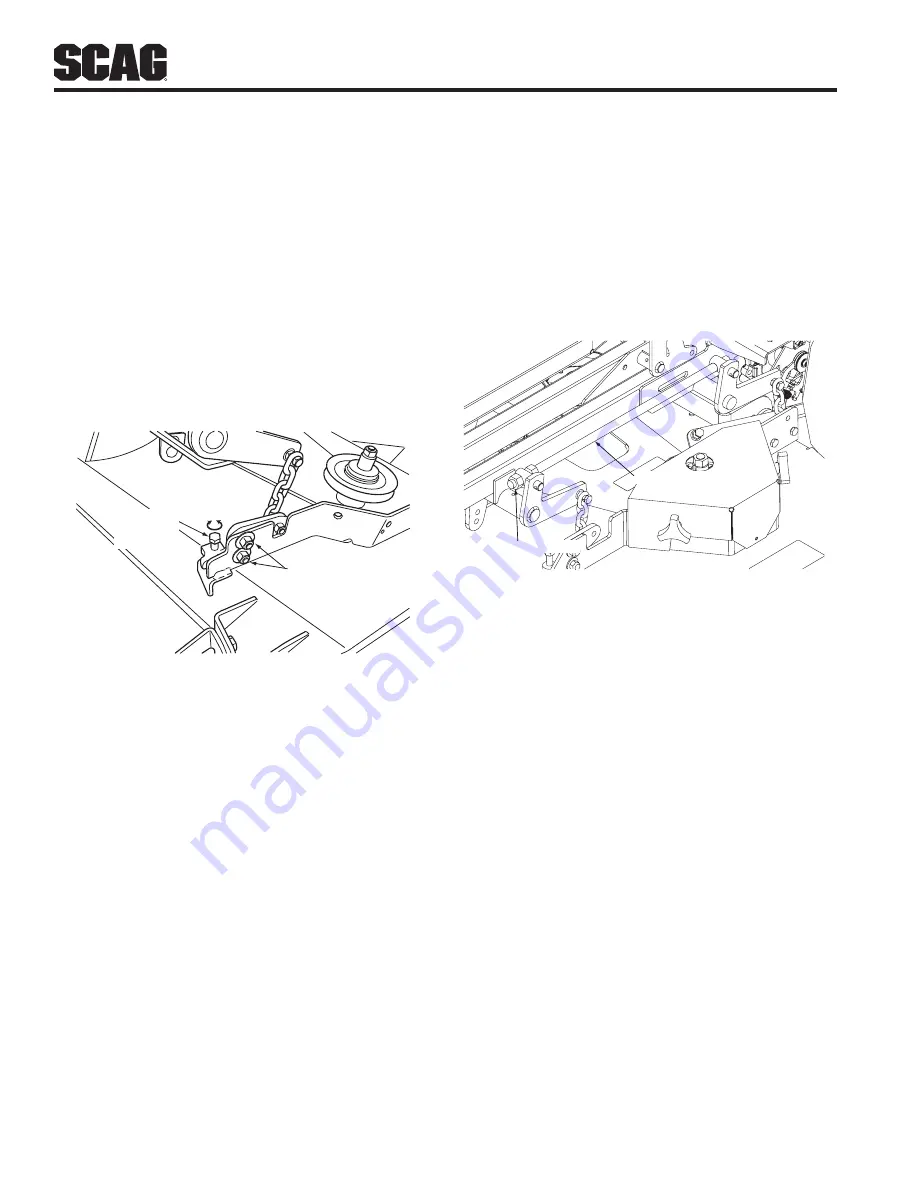
26
R
Section 6
CUTTER DECk LEvEL
The cutter deck should be level from side-to-side for
proper cutting performance. To check for level, be sure
that the mower is on a flat, level surface, the tires are
properly inflated and the cutter deck is set at the most
common cutting height that you will use. On the RH side
of the machine, check the distance from the top of the
cutter deck to the floor. Next check the distance from the
top of the cutter deck to the floor on the LH side of the
machine. Both measurements should be the same. If the
two measurements are different, the cutter deck level
must be adjusted as follows:
On the front LH side of the cutter deck locate the
1.
cutter deck level adjusting bracket. See Figure 6-5.
LOOSEN
HERE
ADJUST
HERE
Cutter Deck Level Adjustment
Figure 6-5.
Loosen the two (2) elastic stop nuts. Adjust the bolt
2.
up or down on the adjustment bracket to adjust
the cutter deck until the distance from the top of
the cutter deck to the floor is the same as the
measurement on the RH side of the machine.
Tighten the two (2) elastic stop nuts to secure the
3.
cutter deck in the proper position.
CUTTER DECk PITCH
The pitch of the cutter deck should be equal between
the front and rear of the cutter deck for proper cutting
performance. To check for proper deck pitch, be sure
that the mower is on a flat, level surface and the tires are
properly inflated.
Check the distance from the top of the cutter deck to the
floor at the rear RH side of the cutter deck directly behind
the cutter deck hanging chains. Next check the distance
from the top of the cutter deck to the floor at the front
RH side of the cutter deck directly in front of the cutter
deck hanging chains. The measurement at the front of the
cutter deck should be the same as the rear of the deck.
Make these measurements at the LH side of the cutter
deck also. If the measurement at the front of the deck is
not the same, the cutter deck pitch must be adjusted as
follows:
Loosen the jam nut on both adjusting rods. See
1.
Figure 6-6.
ADJUSTMENT ROD
LOCK NUT
Cutter Deck Level Adjustment
Figure 6-6.
Using an adjustable jaw pliers, turn the adjusting
2.
rods on the non-threaded portion of the rod until the
deck is equal front to back on both the RH and the
LH side of the cutter deck. Tighten both lock nuts.
- NOTe -
To prevent the cutter deck from teetering, all four
(4) cutter deck hanging chains must have tension
on them. If all four chains do not have tension on
them and the deck teeters, you must readjust the
cutter deck as outlined in the procedures above.
All measurements should be taken from the top
edge of the deck as the Velocity Plus decks have
an uneven bottom edge.
CUTTER DECk HEIGHT
The cutter deck height adjustment is made to ensure
that the cutter deck is cutting at the height indicated on
the cutting height index gauge. To check for proper deck
height, be sure that the mower is on a flat, level surface
and the tires are properly inflated.