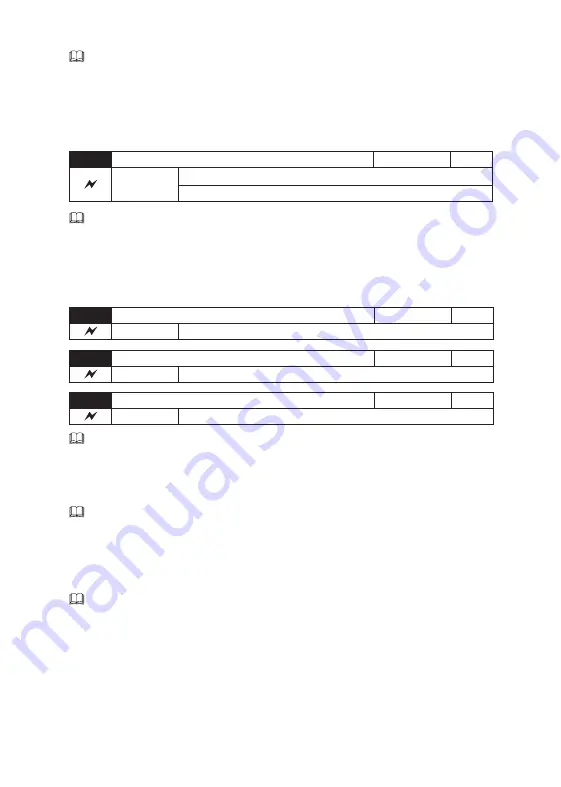
Differential time (Td): It determines the adjusting intensity of variation rate of deviation of PID
feedback quantity and set quantity by PID adjuster. Differential time means if feedback
quantity varies 100% in this period, the adjusted quantity of integral adjuster is the max
frequency (00-03) (Regardless the effects of proportion and integral). The longer the differ-
ential time is, the greater the adjusting intensity will be.
PID is the most commonly used control method in process control, each part has different
function. The following content gives a brief introduction to the working principle and adjust-
ing method.
Integration time (Ti)
Setting range 0.01~10.00s[s]
10-05
Factory setting
0.10
Proportion gain (Kp)
Setting range 0.00~100.00
10-04
Factory setting
0.10
Proportion gain (Kp): it determines the adjustment intensity of whole PID adjuster. The
greater the P is, the greater the adjustment intensity will be. When the parameter value is
100, it means that when the deviation between PID feedback quantity and set quantity is
100%,there is max frequency on PID adjuster when set output frequency command
(Regardless the effects of integral and differential).
Integral time (Ti): It determines the integration adjusting speed of deviation of PID feedback
quantity and set quantity by PID adjuster. Integral time means that when the deviation of
PID feedback quantity and set quantity is 100%, the integral adjuster(Regardless the effects
of proportion and integral) keeps adjusting during this period and make the adjusted
quantity reach to maximum frequency (00-03). The shorter the integral time is, the greater
the adjusting intensity will be.
Differential time (Td)
Setting range 0.00~10.00s[s]
10-06
Factory setting
0.00
0: Analog channel AVI1 feedback
1: Analog channel AVI2/ACI feedback
2: AVI1+AVI2/ACI feedback
3: Remote communication feedback
Selecting PID feedback channel through this parameter.
Note: The set channel and feedback channel can't overlapped. Otherwise, PIID can't
control efficiently.
0: PID output is positive characteristic. When the feedback signal is larger than PID set, it is
necessary to decline the inverter output frequency to make PID reach balance, e.g. PID
control of winding tension.
1: PID output is negative characteristic. When the feedback signal is smaller than PID set, it
is necessary to increase the inverter output frequency to make PID reach balance, e.g. PID
control of unwinding tension.
Factory setting
0
Setting range
0: PID output is positive
1: PID output is negative
PID output characteristic selection
10-03
75
Summary of Contents for S2800 Series
Page 1: ......
Page 2: ......
Page 3: ......
Page 4: ......
Page 5: ......
Page 6: ......
Page 7: ......
Page 8: ......
Page 9: ......
Page 10: ......
Page 11: ......
Page 12: ......
Page 13: ......
Page 14: ......
Page 15: ......
Page 16: ......
Page 17: ......
Page 18: ......
Page 19: ......
Page 20: ......
Page 21: ......
Page 22: ......
Page 23: ......
Page 24: ......
Page 25: ......
Page 26: ......
Page 27: ......
Page 28: ......
Page 29: ......
Page 30: ......
Page 31: ......
Page 32: ......
Page 33: ......
Page 34: ......
Page 35: ......
Page 36: ......
Page 37: ......
Page 38: ......
Page 39: ......
Page 40: ......
Page 41: ......
Page 42: ......
Page 43: ......
Page 61: ......
Page 62: ......
Page 63: ......
Page 64: ......
Page 65: ......
Page 66: ......
Page 67: ......
Page 68: ......
Page 69: ......
Page 70: ......
Page 71: ......
Page 72: ......
Page 73: ......
Page 74: ......
Page 75: ......
Page 76: ......
Page 102: ......
Page 103: ......
Page 104: ......
Page 105: ......
Page 106: ......
Page 107: ......
Page 108: ......
Page 109: ......
Page 110: ......
Page 111: ......
Page 112: ......