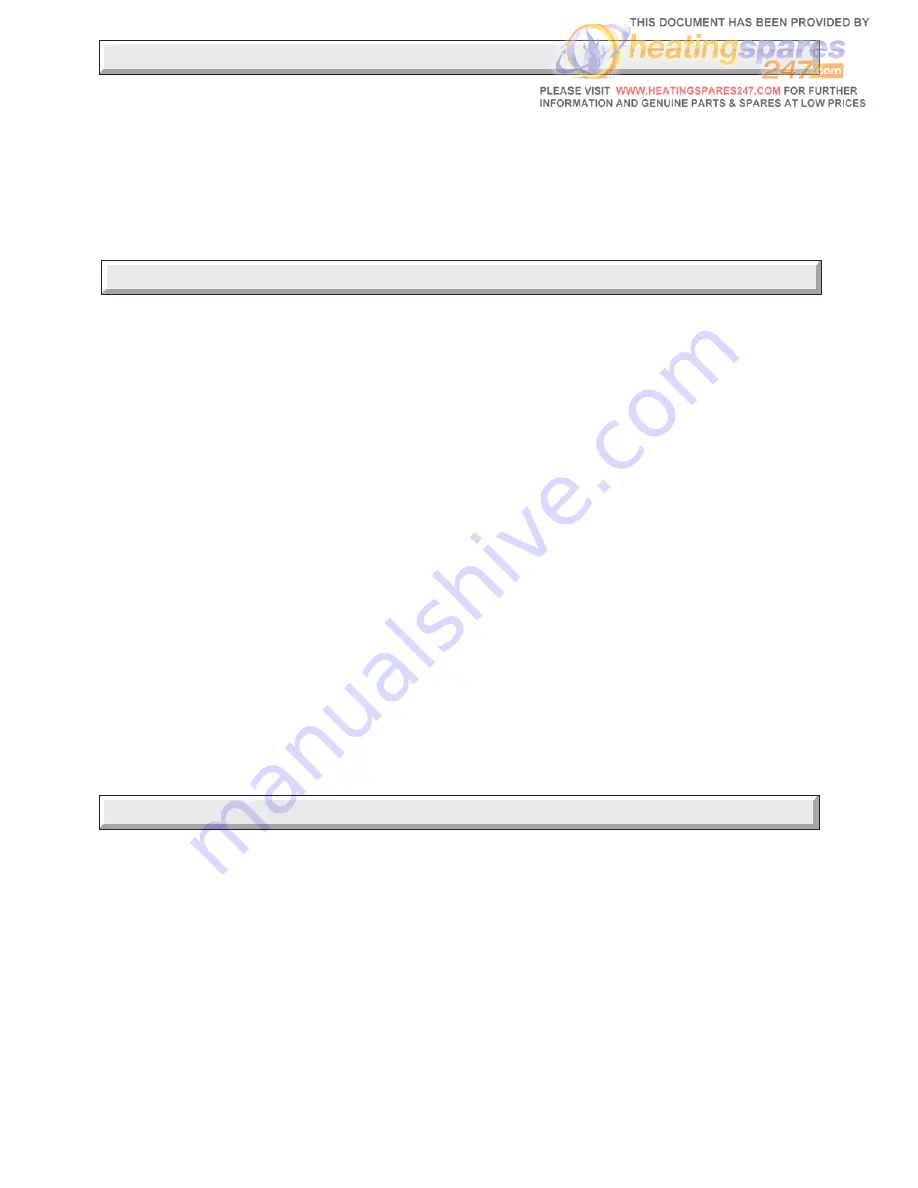
8
4000122704-1
The boiler incorporates a visual fault display that indicates
certain fault conditions, (red flashing light) should they occur.
Should the boiler fail to operate during Commissioning, the
most likely fault is that the gas supply to the boiler has not been
turned on or purged sufficiently or that there is no pressure in the
heating system.
General safety devices
Air flow rate safety device
If an obstruction, even partial, of the flue occurs, for any reason
whatsoever, the built in safety system of the boiler will turn the
boiler OFF, the red light will flash and the fan will continue to run.
The boiler will be ready to operate when the fault has been
cleared.
Heating safety valve
CAUTION: A heating safety valve with a discharge pipe is fitted
to this boiler.
The valve MUST NOT BE TOUCHED except by a qualified
registered person. If the valve discharges at any time, switch the
boiler off and isolate it from the electrical supply. Contact your
installation/service company.
In case of power supply failure
The boiler no longer operates. As soon as power supply is
restored, the boiler will be automatically restarted.
If the gas supply is interrupted
The boiler switches over to safety mode, the red light will flash.
Call a qualified service engineer or Heatcall (Saunier Duval’s
own service organisation) using the telephone number on the
front cover of this literature.
Air in pipes
Important: A central heating system can not operate correctly
unless it is filled with water and air bled from the system. If these
conditions are not met the system may be noisy.
Bleed the air in the radiators and adjust the pressure if system
requires. If the system requires filling to often this may be due
to minor leaks or corrosion in the system. Call a qualified
service engineer or Heatcall (Saunier Duval’s own service
organisation) using the telephone number on the front cover of
this literature.
Frost protection
The boiler has a built in frost protection device that protects the
boiler from freezing. If the boiler is to be left and there is a risk
of frost, ensure that the gas and electrical supplies are left
connected. The frost protection device will light the boiler when
the temperature of the boiler water falls below 6
°
C. When the
temperature reaches 16
°
C, the boiler stops.
Note : This device works irrespective of any room thermostat
setting and will protect the complete heating system.
Servicing and Maintenance
To ensure the continued efficient and safe operation of the
appliance it is recommended that it is checked and serviced as
necessary at regular intervals. The frequency of servicing will
depend upon the particular installation conditions and usage,
but in general once a year should be enough.
If this appliance is installed in a rented property there is a duty
of care imposed on the owner of the property by the current
issue of the Gas Safety (Installation and Use) Regulations,
Section 35.
Servicing/maintenance should be carried out by a competent
person in accordance with the rules in force in the countries of
destination.
To obtain service, please call your installer or Heatcall (Saunier
Duval’s own service organisation) using the telephone number
behind the controls cover door.
Please be advised that the ‘Benchmark’ logbook should be
completed by the installation engineer on completion of
commissioning and servicing.
All CORGI Registered Installers carry a CORGI ID card, and
have a registration number. Both should be recorded in your
boiler Logbook. You can check your installer is CORGI registered
by calling CORGI direct on: 01256 372300.
Cleaning
The boiler casing can be cleaned with a damp cloth followed by
a dry cloth to polish.
Do not use abrasive or solvent cleaners.
Boiler casing
CAUTION. Do not remove or adjust the casing in any way, as
incorrect fitting may result in faulty operation. If in doubt, consult
your installation/service company.
Draining
Protection against freezing
The boiler has a built in frost protection programme as long as
the electricity and gas are left switched on.
If the temperature within the appliance falls to 3˚C the burner
and system pump are activated.
When the temperature inside the appliance reaches 10˚C the
burner will shut down and after a short period the pump will stop.
This device primarily protects the boiler. Any other exposed
areas of the system should be protected by a seperate frost
thermostat.
If the boiler is to be out of use for any long periods during severe
weather conditions, it is recommended that the whole system,
including the boiler, be drained to avoid the risk of freezing.
If in doubt, consult your servicing company.
Draining and filling
Caution: The boiler is installed as part of a sealed system which
must only be drained and filled by a competent person.
Safety Devices