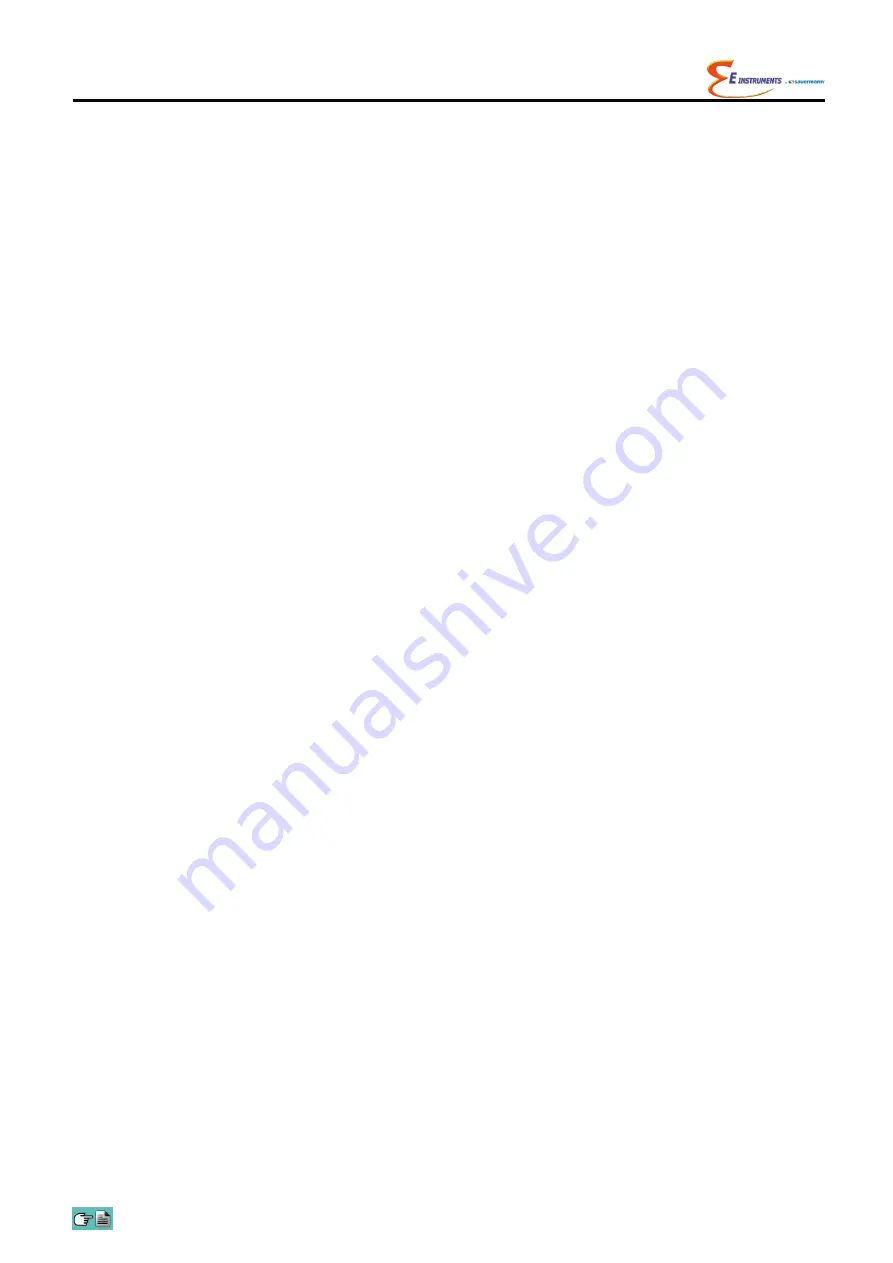
9
K000000000EJ 032433 210519
3.1 Working principle
The gas sample is taken in through the gas probe, by a diaphragm suction pump inside the instrument.
The measuring probe has a sliding cone that allows the probe to be inserted in any stack with
the gas probe
tip roughly centered in the flue.
The gas sample is cooled, dried and cleaned of humidity and impurities/particulates by a condensate trap and
filter positioned along the rubber hose that connects the probe to the analyzer.
The gas is then analyzed by electrochemical gas sensors.
The electrochemical cell guarantees high precision results in a time interval of up to about 60 minutes during
which the instrument can be considered very stable. When measurement is going to take a long time, we suggest
auto-zeroing the instrument again and flushing the inside of the pneumatic circuit for three minutes with clean air.
During the zero calibrating phase, the instrument aspirates clean air from the environment and detects the
sensors’ drifts from zero (20.9% for the O2 cell), then compares them with the programmed values and
compensates them. The pressure sensor autozero must, in all cases, be done manually prior to measuring
pressure.
The values measured and calculated by the microprocessor are viewed on the LCD display which is backlit to
ensure easy reading even when lighting is poor.
3.2 Measurement sensors
Oxygen (%O
2
) is measured with an electrochemical cell that acts like a battery which, over time, is apt to lose
sensitivity.
The toxic gases (CO, SO
2
, NO, NO
2
) are measured with electrochemical sensors that are not subject to natural
deterioration being intrinsically lacking of oxidation processes.
The measurement sensors are electrochemical sensors made up of an anode, a cathode, and an electrolytic
solution, which depends on the type of gas to be analysed. The gas penetrates the cell through a selective
diffusion membrane and generates an electric current proportional to the absorbed gas. Such current is
measured, digitalized, temperature-compensated, processed by the microprocessor, and displayed.
The gas shall not be at a pressure such to damage or destroy sensors. The maximum estimated allowed
pressure is ±100mbar gage.
The response times of the measurement sensors used in the analyzer are:
O
2
=
20 sec. at 90% of the measured value
CO(H
2
) =
50 sec. at 90% of the measured value
CO
=
50 sec. at 90% of the measured value
NO
= 40 sec. at 90% of the measured value
NO
2
=
50 sec. at 90% of the measured value
SO
2
=
50 sec. at 90% of the measured value
It is therefore suggested to wait 5 minutes (anyway not less than 3 minutes) in order to get reliable analysis data.
If sensors of poison gases are submitted to concentrations higher than 50% of their measurement range for more
than 10 minutes continuously, they can show up to ±2% drift as well as a longer time to return to zero. In this
case, before turning off the analyzer, it is advisable to wait for the measured value be lower than 20ppm by
intaking clean air. If there is an automatic calibration solenoid, the device performs an automatic cleaning cycle
and it turns off when the sensors return to a value close to zero..
The CO sensor can be protected from high gas concentrations through the dilution function which allows for a
wider measurement range of the sensor without overcharging the sensor itself.
The dilution function allows the CO sensor to always be efficient and ready to respond even in the case of very
high concentrations of CO.
3.0 WORKING PRINCIPLE
Summary of Contents for E INSTRUMENTS 1500
Page 2: ......
Page 67: ...67 K000000000EJ 032433 210519 10 1 1 Memory Organization...
Page 166: ......
Page 168: ......
Page 169: ......