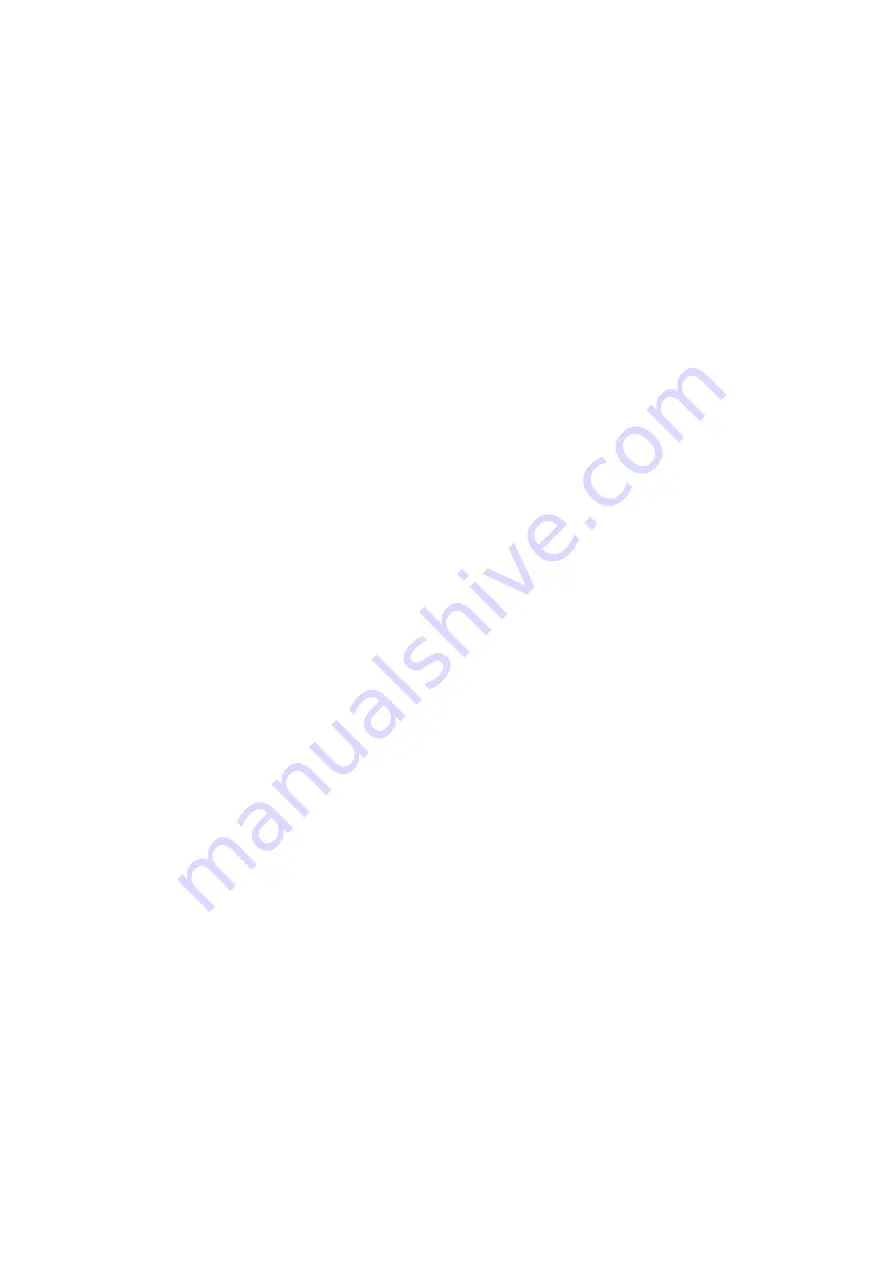
CONTROL MODULES
(Cont.)
RPW Setting (review only)
This parameter displays the remote set value from the RPW input to
the controller.
–10,000 to 10,000
–
Reset Setting (review only)
This parameter displays the influence that the reset input is having on
the set value.
–10,000 to
+10,000/10 Volts
–
Reset Ratio
This setting is used to determine the influence that an analogue input
connected to the reset input of the controller has over the main set
value. By setting the value as a positive number the set value will be
increased as the analogue input is increased. The opposite is true if it
is set to a negative value.
–10,000 to
+10,000/10 Volts
10
Stage 1 Deadzone Occupied
The deadzone is the difference between the set value and the point at
which the stage starts to control. This parameter is used whilst the
controller is in occupied mode.
0 to 10,000
1
Stage 2 Deadzone Occupied
The deadzone is the difference between the set value and the point at
which the stage starts to control. This parameter is used whilst the
controller is in occupied mode.
0 to 10,000
1
Stage 1 Deadzone Relaxed
As for the occupied deadzone but only used whilst the controller is in
relaxed mode.
0 to 10,000
3
Stage 2 Deadzone Relaxed
As for the occupied deadzone but only used whilst the controller is in
relaxed mode.
0 to 10,000
3
Stage 1 Deadzone Night
As for the occupied deadzone but only used whilst the controller is in
night mode.
0 to 10,000
6
Stage 2 Deadzone Night
As for the occupied deadzone but only used whilst the controller is in
night mode.
0 to 10,000
6
Upper Deadzone (review only)
This parameter displays the upper deadzone value that the IAC is
currently using.
–10,000 to 10,000
–
Lower Deadzone (review only)
This parameter displays the lower deadzone value that the IAC is
currently using.
–10,000 to 10,000
–
Stage 1 Proportional Band
This setting is the range over which the Stage 1 output moves
proportionally across its full stroke.
0 to 10,000
10
Stage 1 Integral Action Time (0 = Off)
This parameter is the set time interval necessary for integral action
time to increase the Stage 1 output by the current proportional level.
Set to 0 for purely proportional control.
0 to 10,000
Seconds
300 Secs
Stage 1 Derivative Action Time (0 = Off)
This is usually left at zero. It is used where a faster control action is
required and reducing the Proportional Band and/or Integral time
causes hunting. As a guide, the derivative time must be set at less
than a tenth of the Integral Time as a start point.
0 to 10,000
Seconds
0 Secs
Stage 1 Ramp Time
This determines the time in seconds for the output stage to change
from fully closed to fully open (given a continuous demand).
0 to 10,000
Seconds
60 Secs
Stage 2 Proportional Band
This setting is the range over which the Stage 2 output moves
proportionally across its full stroke.
0 to 10,000
10
Stage 2 Integral Action Time (0 = Off)
This parameter is the time interval necessary for integral action time to
increase the Stage 2 output by the current proportional band. Set to 0
for purely proportional control.
0 to 10,000
Seconds
300 Secs
Stage 2 Derivative Action Time (0 = Off)
See Stage 1 Derivative Action Time
0 to 10,000
Seconds
0 Secs
Stage 2 Ramp Time
This determines the time in seconds for the output stage to change
from fully closed to fully open (given a continuous demand)
1 to 10,000
Seconds
60 Secs
Sample Time (0 = as fast as possible)
This is the interval between successive readings of the measured
values at the connected sensors. A short interval of say 10 seconds
permits rapid response but only a small amount of corrective action. It
is suited to systems having short time constants.
0 to 10,000
Seconds
10 Secs
A longer interval such as 20 seconds is slower to react but permits a
larger amount of corrective action. For this reason it is suited to
systems having medium length time constants.
If control action tends to be too slow reduce the setting and if it tends
to hunt increase it. This fine tuning should be done in small steps of
around 10 to 20%.
MODULES AND FUNCTIONS
Bubbleland
Symbol
Module
Range
Default
05/98
7 - 24
DS 2.951A
Summary of Contents for IAC 600
Page 23: ...05 98 23 24 DS 2 951A ...