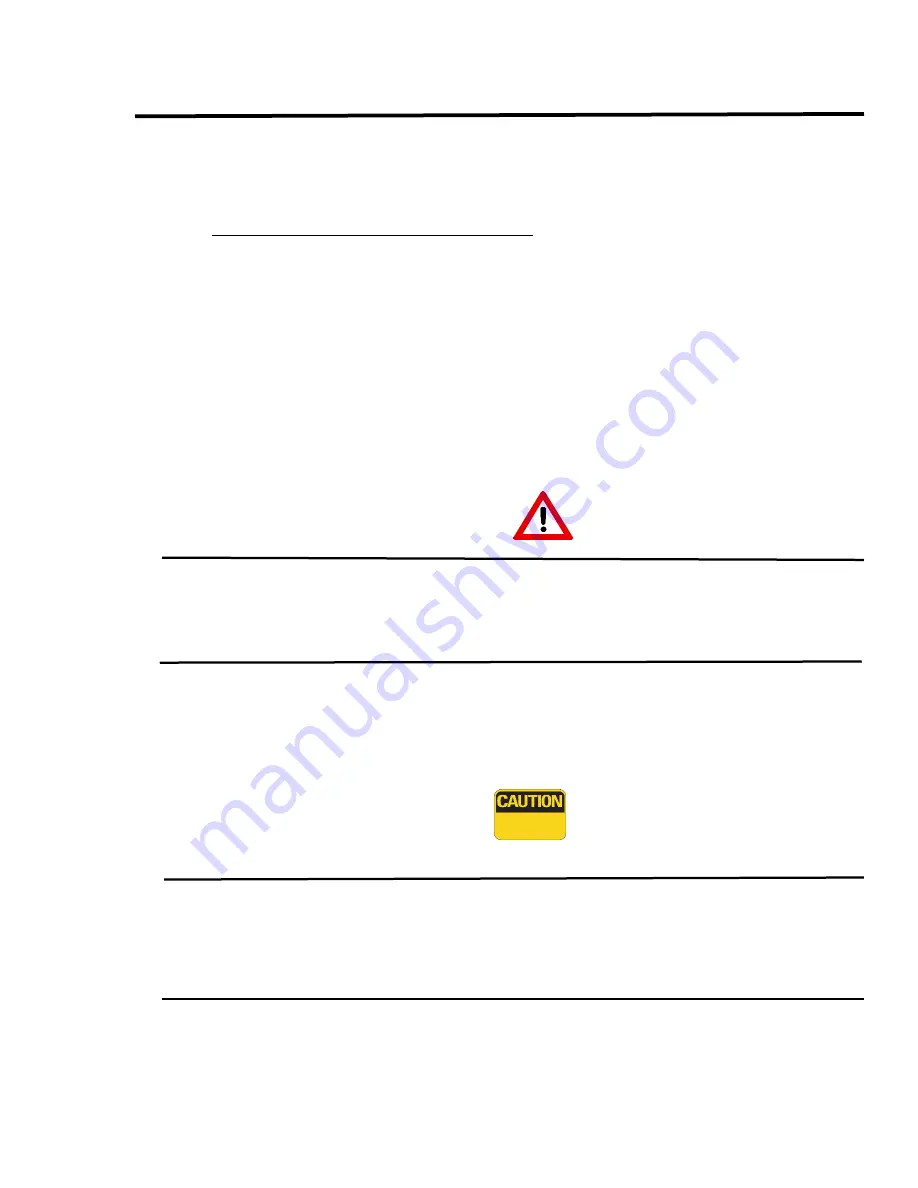
65
SECTION 9 – ROUTINE MAINTENANCE
9.0
ROUTINE MAINTENANCE
Routine inspection and testing (power source)
An inspection of the power source, an insulation resistance test and an earth resistance test
should be carried out
a)
For transportable equipment, at least once every 3 months; and
b)
For fixed equipment, at least once every 12 months.
The owners of the equipment shall keep a suitable record of the periodic tests.
The only routine maintenance required for the power supply is a thorough cleaning and
inspection, with the frequency depending on the usage and the operating environment.
WARNING:
Disconnect Primary power at the source before opening the enclosure. Wait at least
two minutes before opening the enclosure to allow the primary capacitors to
discharge.
To clean the unit, open the enclosure (see Section 9.1, Opening the Enclosure) and use a
vacuum cleaner to remove any accumulated dirt and dust. The unit should also be wiped clean, if
necessary; with solvents that are recommended for cleaning electrical apparatus.
Do not blow air into the power supply during cleaning. Blowing air into the unit
can cause metal particles to interfere with sensitive electrical components and
cause damage to the unit.
Summary of Contents for SANARG 160P
Page 2: ......
Page 4: ......
Page 8: ......
Page 15: ...15 1 3 2 GRAPHIC SYMBOL LEGEND ...
Page 24: ...24 PAGE LEFT INTENTIONALLY BLANK ...
Page 35: ...35 Figure 3 1 Electrical Input Connections 160P ...
Page 47: ...47 PAGE LEFT INTENTIONALLY BLANK ...
Page 64: ...64 PAGE LEFT INTENTIONALL BLA ...
Page 76: ...76 10 1 INTERCONNECT DIAGRAM 160P ...
Page 77: ...77 ...
Page 78: ...78 10 2 EXPLODED VIEW COMPONENT LAYOUT 160P ...
Page 79: ...79 ...
Page 80: ...80 PAGE LEFT INTENTIONALL BLANK ...