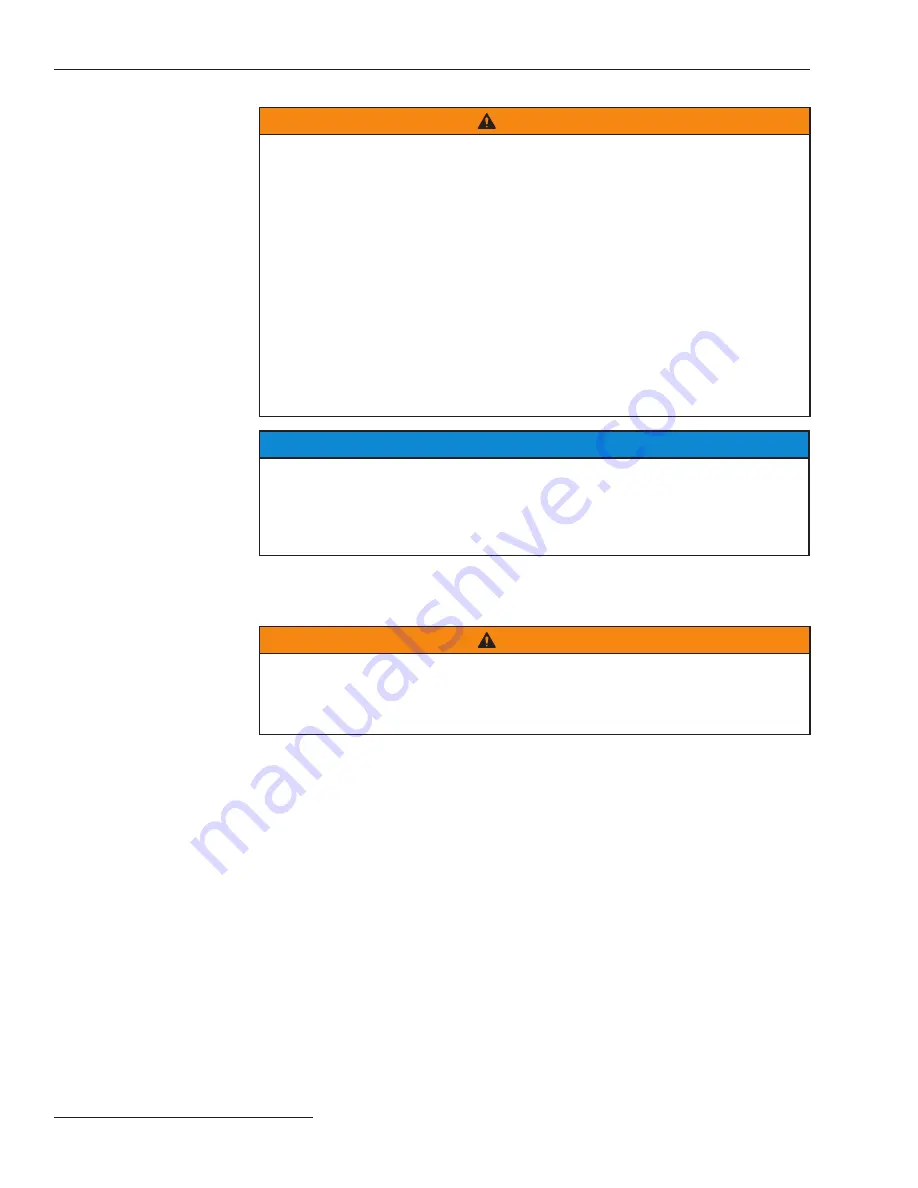
2
S&C Instruction Sheet 761-505
Introduction
Qualified Persons
WARNING
Only qualified persons who are knowledgeable in the installation, operation, and
maintenance of overhead and underground electric distribution equipment, along
with all associated hazards, may install, operate, and maintain the equipment
covered by this publication. A qualified person is someone who is trained and
competent in:
• The skills and techniques necessary to distinguish exposed live parts from nonlive
parts of electrical equipment
• The skills and techniques necessary to determine the proper approach distances
corresponding to the voltages to which the qualified person will be exposed
• The proper use of special precautionary techniques, personal protective
equipment, insulated and shielding materials, and insulated tools for working on
or near exposed energized parts of electrical equipment
These instructions are intended ONLY for such qualified persons. They are
not intended to be a substitute for adequate training and experience in safety
procedures for this type of equipment.
Read this
Instruction Sheet
NOTICE
Thoroughly and carefully read this instruction sheet and all materials included in
the product’s S&C Instruction Handbook before installing or operating your S&C
Alduti-Rupter Switch. Familiarize yourself with the Safety Information and Safety
Precautions on pages 4 through 6. The latest version of this publication is available
online in PDF format at
sandc.com/en/support/product-literature/.
Retain this
Instruction Sheet
This instruction sheet is a permanent part of your S&C Alduti-Rupter Switch. Designate
a location where you can easily retrieve and refer to this publication.
Proper Application
WARNING
The equipment in this publication is only intended for a specific application. The
application must be within the ratings furnished for the equipment. Ratings for the
Alduti-Rupter Switch are listed in the ratings table in Specification Bulletin 761-31.
The ratings are also on the nameplate affixed to the product.