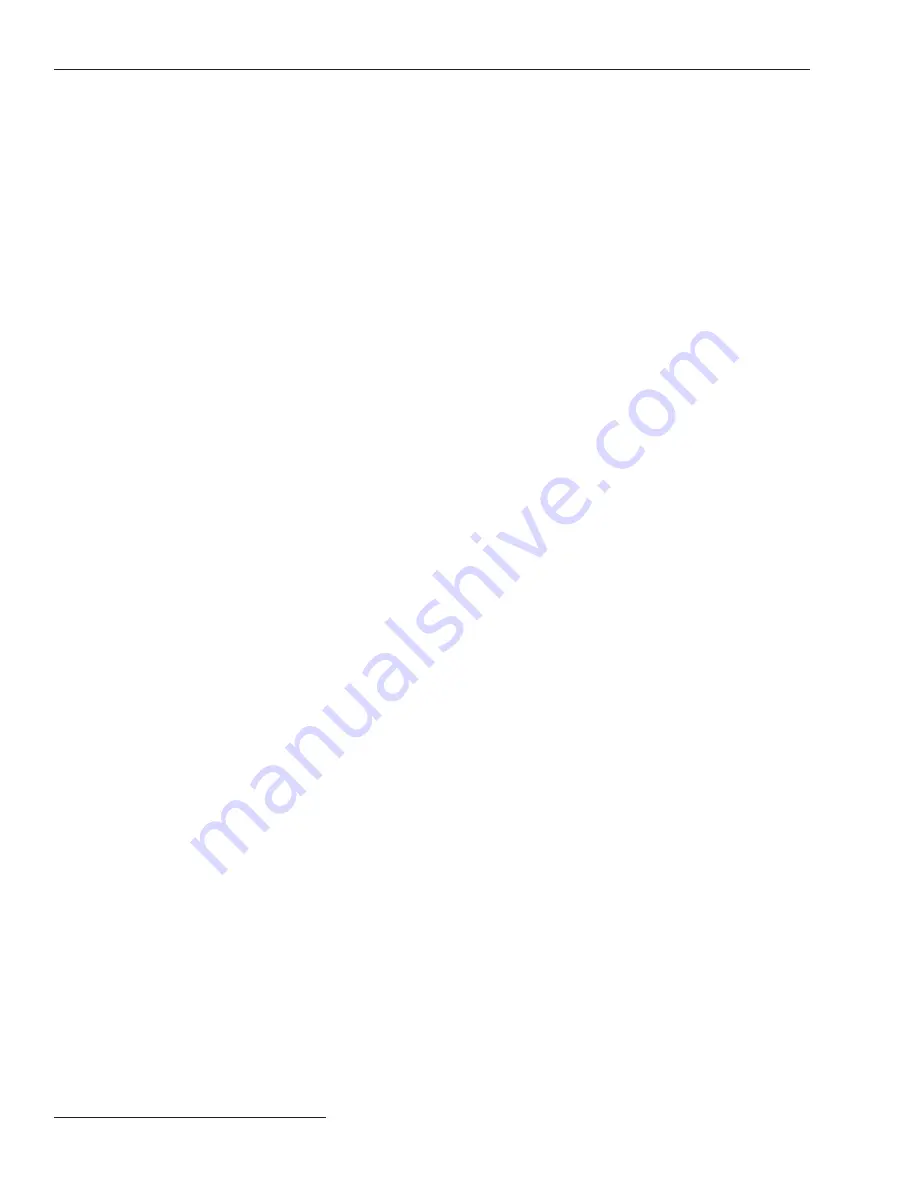
26
S&C Instruction Sheet 1045M-510
Installing the Reciprocating Switch Operator
The switch operator installation consists of several operations. The following
information is specific to the 6801M Reciprocating Switch Operator.
Installing the Switch
Operator and
Connecting the Wiring
STEP 1.
Read, and make sure to understand, the following functional description and
safety instructions before beginning to install or operate this equipment. The
reciprocating switch operator functions differently from the rotating switch
operator because the opening and closing motion is transmitted to the switch
as a reciprocating (up and down) movement instead of a rotating movement. To
create this reciprocating movement, the switch operator uses an additional
mechanical linkage mounted on the back of the switch operator. This linkage
may be protected by an optional, lockable enclosure or shroud.
To operate the switch, the reciprocating switch operator first generates a
rotating movement using the same type of motor and gear box used in the rotat-
ing switch operator. This rotating movement is then transmitted to a rotating
output crank on the back of the switch operator. This output crank creates a
reciprocating (up and down) movement that is transmitted to a pivoting yoke
with a connecting link. The connecting link is clamped to the rod that oper-
ates the switch.
When setting up the switch operator, it is extremely important to make the out-
put crank at the bottom of the control rod move in parallel with the switch operating
lever connected to the top of the control rod. In other words, when the switch is
open, the output crank and the switch operating lever should both be about 45
degrees below horizontal, and when the switch is closed, they should both be
approximately 45 degrees above horizontal. When this is true, the control rod will
accurately transfer rotational movement from the switch operator up to the
switch itself. If the mechanical setup is done in this way, installing the switch
operator will be much easier and faster.
Different brands of switches and installations require different positions for the
output crank yoke. The principle is that the lever at the top of the control rod should
be the same length as the lever at the bottom. This can be adjusted as necessary by
connecting the output crank yoke to a suitable bolt hole in the output crank (see
Figure 16 on page 29). Six bolt holes are provided at one-inch (25 mm) intervals,
from 6 (152 mm) to 11 (279 mm) inches away from the output drive shaft. Note
that when the switch is fully open, the output crank and the switch operating
lever should both be approximately 45 degrees below horizontal. Closing the
switch requires a vertical push on the control rod that is created by a clockwise,
as viewed from the front of the switch operator, rotation of the output crank.
The output crank is fastened to the output drive shaft by the decoupler pin.
During operation of the switch operator, the decoupler pin must be secured
in place with a
⅜
-inch shackle padlock or
⅜
-inch bolt (see Figure 16 on
page 29). By removing this pin, the output crank will be disconnected
from the output drive shaft during the installation procedure (steps 8
through 16, on pages 31 through 34). The
Align
(slow-operation) mode of
the switch operator permits a final adjustment of the output drive shaft
position to ensure that the decoupler shaft pin can be reinstalled when the
output crank is in the correct position.
When manual operation of the switch is required, the decoupler pin is removed.
The switch is then operated by the manual crank handle, which is temporarily
installed over the end of the output crank. Lockout for the switch, under manual
operating conditions, is provided by padlock holes in the lockout bracket that
match similar holes in the output crank.