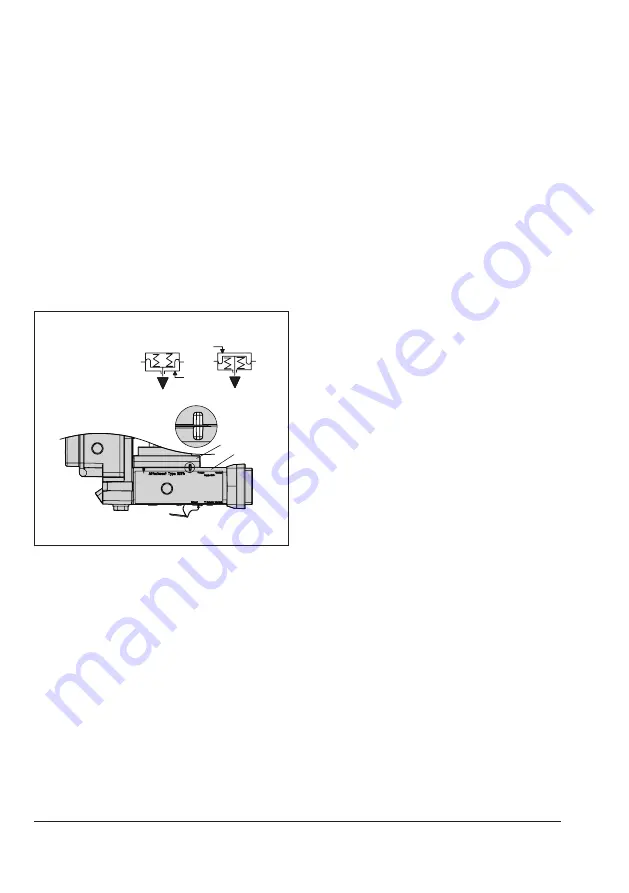
54
EB 8384-6S EN
Mounting and start-up
7. Insert the screws (13.1) through the mid-
dle holes of the adapter block (13).
8. Place the connecting plate (12) together
with the seal (12.1) onto the screws
(13.1) corresponding to the fail-safe ac-
tion "actuator stem extends" or "actuator
stem retracts". The fail-safe action that
applies is determined by aligning the
groove of the adapter block (13) with the
groove of the connecting plate (12) (Fig.
10).
Z
Z
12
13
Actuator stem
retracts
extends
12 Connecting plate
13 Adapter block
Fig. 10:
Fail-safe action
9. Mount the adapter block (13) together
with the connecting plate (12) to the ac-
tuator using the screws (13.1).
10. Insert the vent plug (11.1) into the
Exh.
connection.
11. For fail-safe action "actuator stem ex-
tends", seal the Y1 port with a blanking
plug.
For fail-safe action "actuator stem re-
tracts", connect the Y1 port to the signal
pressure connection of the actuator.
Place positioner on the adapter block
(13) in such a manner that the follower
pin (2) rests on the top of the follower
clamp (3). Adjust the lever (1) corre-
spondingly and open the positioner cov-
er to hold the positioner shaft in position
at the cap or rotary pushbutton.
The lever (1) must rest on the follower
clamp with spring force.
Fasten the positioner to the adapter block
(13) using the two fastening screws (6.3).
Make sure the molded seal (6.2) is prop-
erly seated.
12. Mount cover (11) on the other side to the
yoke. Make sure that the vent plug is lo-
cated at the bottom when the control
valve is installed to allow any condensed
water that collects to drain off.
Summary of Contents for TROVIS SAFE 3730-6
Page 12: ...12 EB 8384 6S EN...
Page 16: ...16 EB 8384 6S EN...
Page 22: ...22 EB 8384 6S EN...
Page 40: ...40 EB 8384 6S EN...
Page 42: ...42 EB 8384 6S EN...
Page 82: ...82 EB 8384 6S EN...
Page 90: ...90 EB 8384 6S EN...
Page 96: ...96 EB 8384 6S EN...
Page 132: ...132 EB 8384 6S EN...
Page 152: ...152 EB 8384 6S EN...
Page 155: ...EB 8384 6S EN 155...
Page 156: ...156 EB 8384 6S EN...
Page 157: ...EB 8384 6S EN 157...
Page 158: ...158 EB 8384 6S EN...
Page 159: ...EB 8384 6S EN 159...
Page 160: ...160 EB 8384 6S EN...
Page 161: ...EB 8384 6S EN 161...
Page 162: ...162 EB 8384 6S EN...
Page 163: ...EB 8384 6S EN 163...
Page 164: ...164 EB 8384 6S EN...
Page 165: ...EB 8384 6S EN 165...
Page 166: ...166 EB 8384 6S EN...
Page 167: ...EB 8384 6S EN 167...
Page 182: ...182 EB 8384 6S EN...
Page 183: ...EB 8384 6S EN 183...