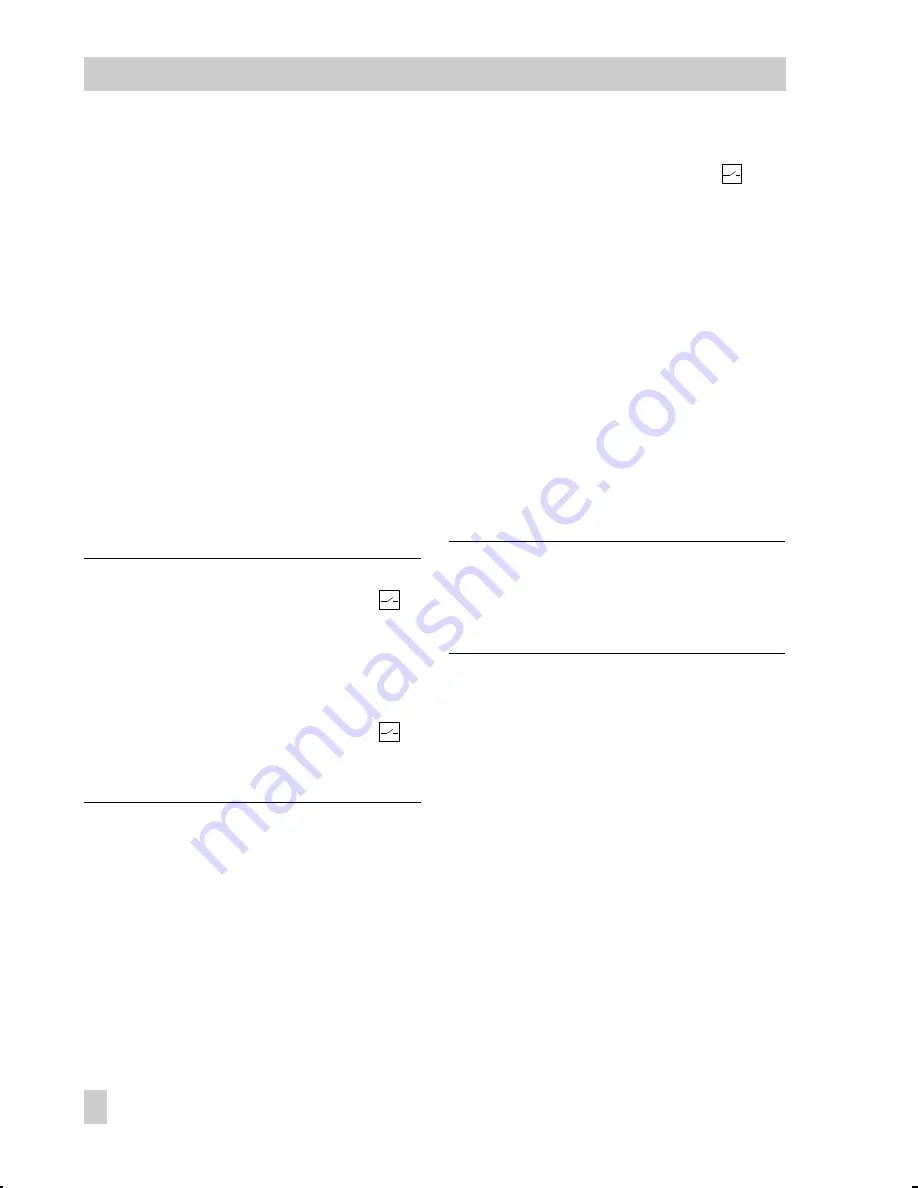
4.3 Setting the digital positioner
In the actuator version with digital posi-
tioner, the travel is calibrated automatically,
so that the travel (controlled variable x) and
the input signal (reference variable w) of the
positioner can be matched in the best
possible way.
Additionally, the digital positioner provides
valve position feedback for remote trans-
mission.
Adjustment and start-up can be carried out
using four different operating modes. Oper-
ating modes
1
and
2
work with set data
stored in the positioner’s memory. The user
only needs to select the operating mode via
the selector switch (2) and press the but-
ton (4) to start travel calibration.
Note!
Setup with operating modes
3
and
0
=
can only be performed using a SAMSON
memory pen as storage medium, or in con-
nection with SAMSON’s TROVIS-VIEW
Configuration and Operator Interface soft-
ware and a PC or bus system.
Setup with operating modes
3
and
0
=
is described in Mounting and Operating
Instructions
EB 8331-2 EN
.
Settings for operating modes 1 and 2
Increasing characteristic: actuator stem re-
tracts or extends as the reference variable
increases.
After the actuator has been mounted on the
valve as described in section 2.2 and the
electrical connections have been installed as
described in section 3, proceed as follows:
1. Set selector switch (2) with the arrow
pointing to operating mode
0
= (con-
trol switched off).
2. Check mounting position of the poten-
tiometer gear (12).
The gear must be put onto the potentiometer
shaft to correspond with the rated travel of
the control valve.
The inscription
Nennhub 15
(for 6 to 20 mm travel) or
Nennhub 30
(for 6 to 35 mm travel) must
be legible from above on the associated
gear side.
If this is not the case, pull the gear off the
shaft and put it back on again with the
reverse side facing upwards, allowing the
intermediate gear to engage properly.
Note!
Actuators with fail-safe action "Actua-
tor stem retracts" or "extends" are only de-
signed for a rated travel of 15 mm. Do not
rearrange the gear!
Make sure that the shaft of the poten-
tiometer (12) is adjusted correctly.
3. Switch on auxiliary power and set the
reference variable to a value > 4 mA.
4. Set selector switch (2) with the arrow
pointing to operating mode
1
for 4 to
20 mA or 2 to 10 V input and alarm
signal,
or set it to operating mode
2
for 0 to
20 mA or 0 to 10 V input and alarm
signal.
5. Press button (4) to start travel calibra-
tion.
12
EB 8331-1 EN
Setting the digital positioner
Summary of Contents for 3374
Page 21: ...EB 8331 1 EN 21...