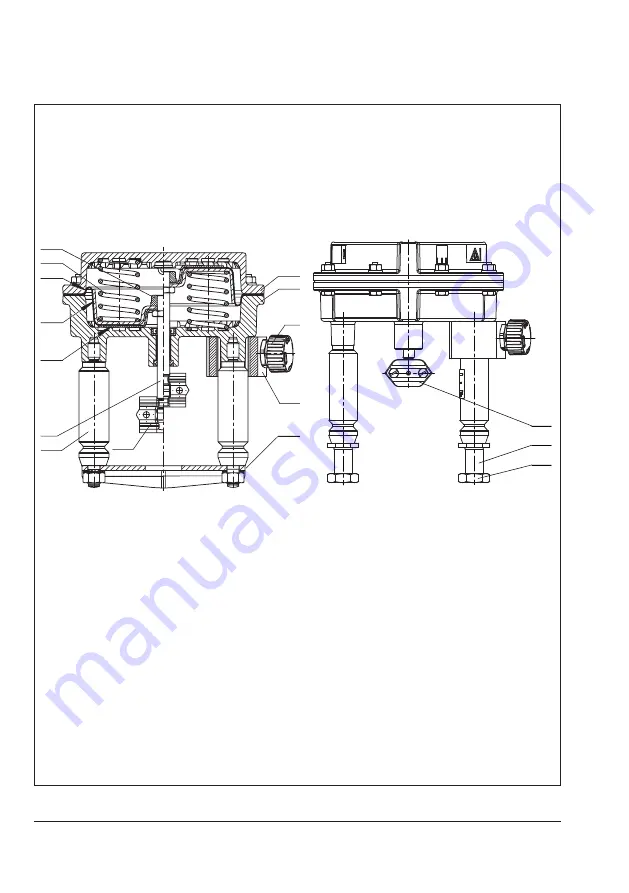
9-6
EB 8317 EN
Servicing and conversion
A1
Vent plug
A2
Bottom diaphragm case
A3
Actuator stem
A10
Spring
A11
Rod
A12
Bushing
A13
Diaphragm plate
A14 Diaphragm plate
A16 Top diaphragm case
A17 Crossbeam
A18
Diaphragm
A26 Collar nut
A30/
A31
Stem connector clamps
A35
Pneumatic connection
A72 Rod nut
Mounting with crossbeam
Mounting without crossbeam
A31
A72
A12
•
•
•
A3
A30
A26
A10
A18
A13
A14
A11
A2
A16
A35
A1
A17
•
•
•
•
•
•
•
•
•
•
Fig. 9-1:
Functional diagram of Type 3371 Actuator with 120 cm² actuator area
Summary of Contents for 3371 Series
Page 12: ...2 2 EB 8317 EN ...
Page 20: ...3 8 EB 8317 EN ...
Page 24: ...4 4 EB 8317 EN ...
Page 32: ...5 8 EB 8317 EN ...
Page 50: ...9 10 EB 8317 EN ...
Page 52: ...10 2 EB 8317 EN ...
Page 56: ...11 4 EB 8317 EN ...
Page 58: ...12 2 EB 8317 EN ...
Page 60: ...13 2 EB 8317 EN ...
Page 62: ...14 2 EB 8317 EN ...
Page 69: ......