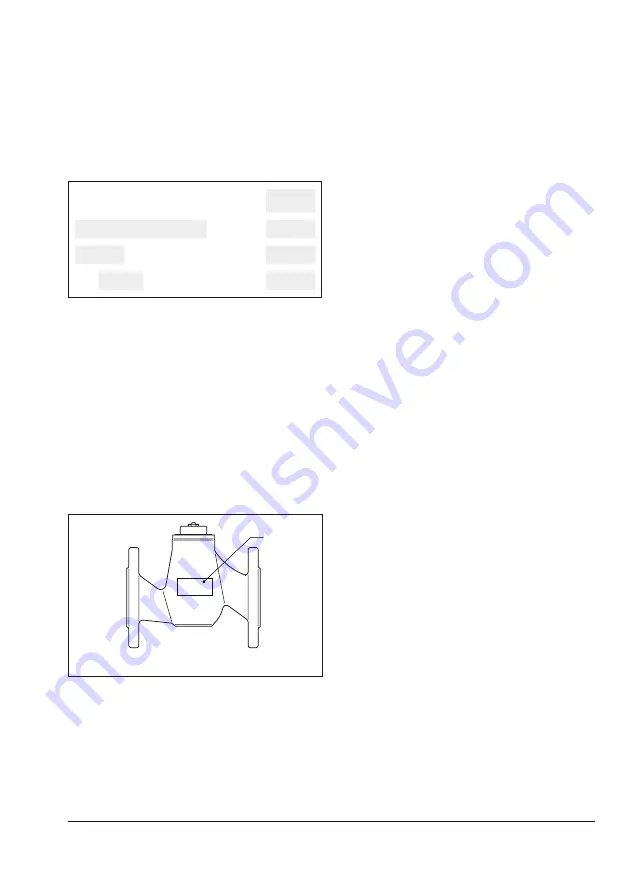
EB 5866 EN
2-1
Markings on the device
2 Markings on the device
2.1 Valve nameplate
SAMSON
1
2
3
4
5
kvs
6
Δp
7
1
Type designation
2
Configuration ID
3
Date of manufacture
4
Model number
5
Max. permissible temperature
6
K
VS
coefficient
7
Max. perm. differential pressure
The nameplate (48) is affixed to the valve
body (see Fig. 2-1).
48
Fig. 2-1:
Location of the nameplate
2.2 Actuator nameplate
See associated actuator documentation.
Summary of Contents for 3222 Series
Page 14: ...2 2 EB 5866 EN...
Page 36: ...5 8 EB 5866 EN...
Page 40: ...7 2 EB 5866 EN...
Page 46: ...9 4 EB 5866 EN...
Page 52: ...12 2 EB 5866 EN...
Page 54: ...13 2 EB 5866 EN...
Page 56: ...14 2 EB 5866 EN...
Page 57: ...EB 5866 EN 14 3...
Page 58: ...14 4 EB 5866 EN...
Page 60: ...15 2 EB 5866 EN...
Page 61: ......
Page 62: ......
Page 63: ......