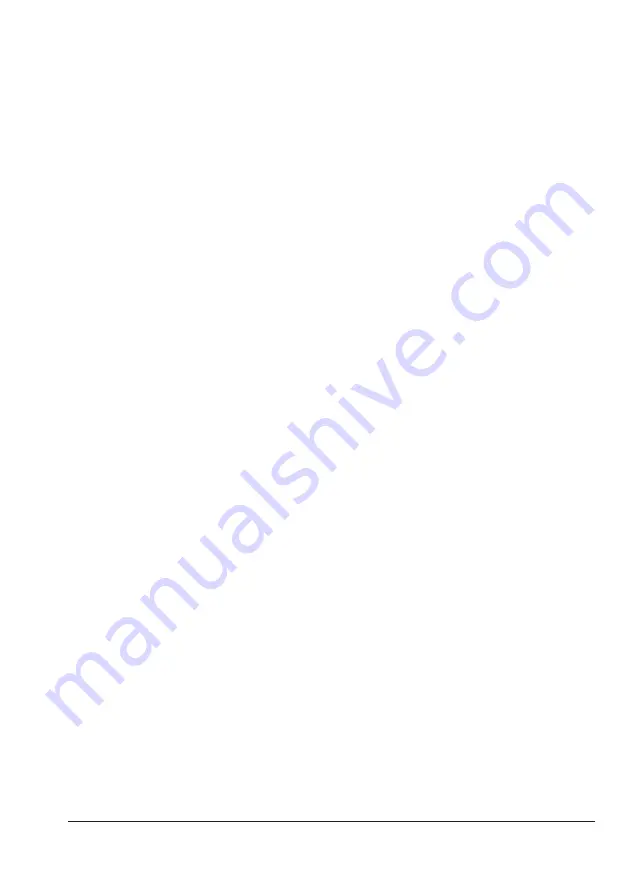
EB 2540 EN
9-3
Servicing
9.2
Installing the regulator
after service work
Î
Put the regulator back into operation (see
the 'Start-up' section). Make sure the re-
quirements and conditions for start-up or
putting the valve back into operation are
met.
9.3
Service work
Î
Before performing any service work,
preparations must be made to the regu-
lator (see section 9.1).
Î
After all service work is completed, check
the regulator before putting it back into
operation (see the 'Testing the regulator'
section).
Summary of Contents for 2404-2
Page 12: ...1 8 EB 2540 EN Safety instructions and measures...
Page 18: ...2 6 EB 2540 EN Markings on the device...
Page 34: ...3 16 EB 2540 EN Design and principle of operation...
Page 60: ...11 2 EB 2540 EN...
Page 62: ...12 2 EB 2540 EN...
Page 64: ...13 2 EB 2540 EN...
Page 72: ...14 8 EB 2540 EN...
Page 75: ......