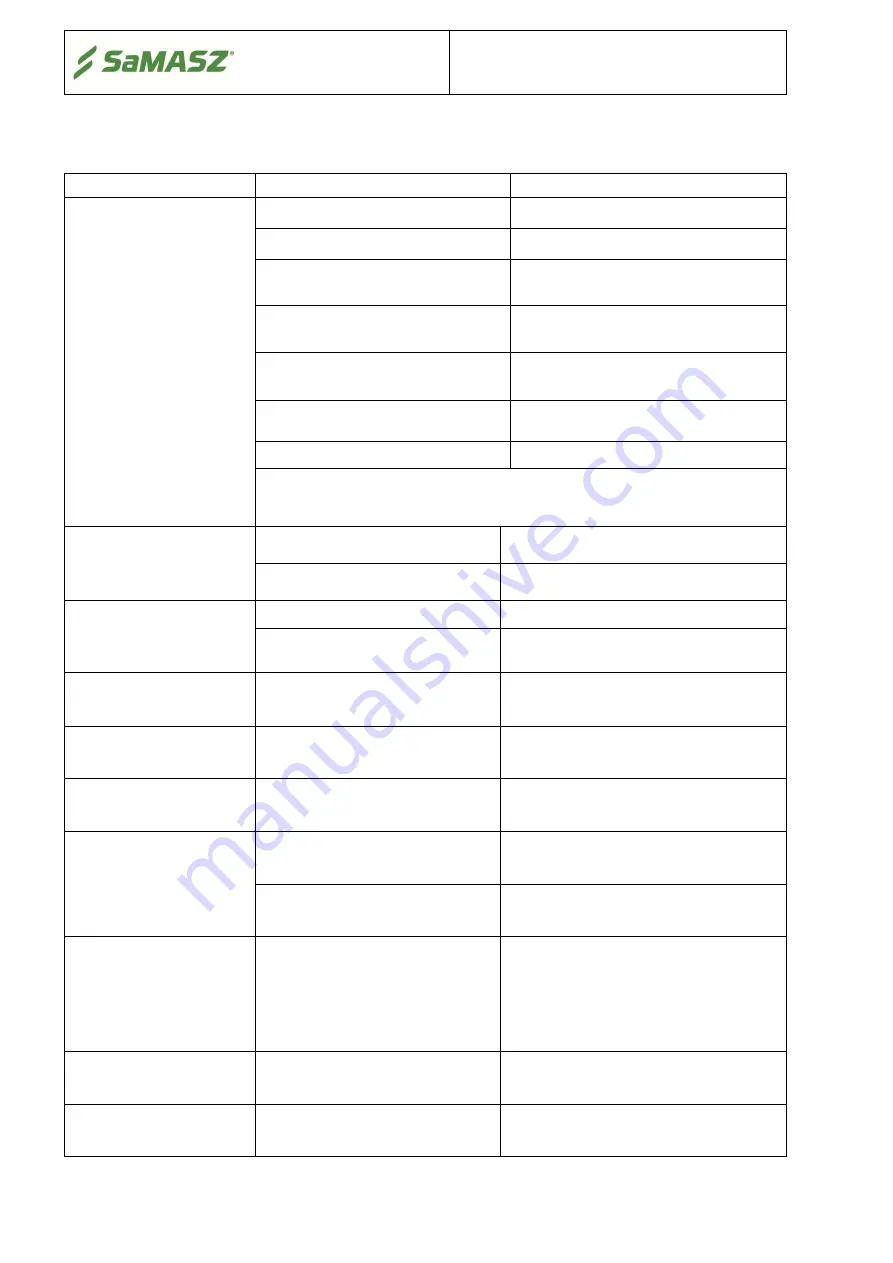
Operator's manual
Trailed disc mowers
KDC
- 44 -
8.
DEFECTS AND THEIR REPAIR
Tab. 12.
Possible defects and their repairs
Defect type
Reason
Recommendations
Mower fails to mow or
leaves strip of uncut grass
between discs
Some of knives are missing
Mount knives
Worn knives
Replace knives with new ones
Improperly mounted knives
(left – right)
Mount knives strictly keeping
provisions found in manual
Too high tractor's engine rpm
(the most frequent mistake)
Reduce rpm
Too low operating speed
Increase driving speed above
V
≥
10 km/h
Damaged tractor's PTO shaft, drive
not transmitted
Remove defect
Laid grass
Low mowing on each occasion
It is tolerable for a mower with conditioner or rollers to mow improperly in
case of very low grass or during a rainfall
Mower is blocked
Damaged bearings in disc hub
Replace bearings
Damaged cogs in cutterbar
Examine condition of all cogs
Mower is not mowing even
though drive is transmitted
from tractor
Torn roller inside gear
Replace gear
Torn or cut down hollow on
cutterbar drive shaft
Put new hollow
Mower works excessively
loud
Too low oil level in cutterbar
Examine oil level and refill oil
Mower slows down even
though rpm value is stable
Damaged friction clutch in
cutterbar
Replace clutch
Conveyor is clogged with
grass
Too low conveyor speed
Increase – adjust so as corresponds to
grass weight
Mower is clogged with
grass – no grass guiding or
guiding is uneven
Too low mowing speed
Increase driving speed above 10 km/h or
more
Swath guides are set too narrow
Widen swath guides to the maximum
Leaking cylinder
Dirty oil in hydraulic unit of the
tractor
Replace oil in hydraulic unit of the
tractor (recommended class of
cleanliness of oil according to NAS 1638
is minimum 9-10).
Purchase repair kit of the cylinder and
replace damaged sealings
Excesive vibration during
work
Damaged PTO shaft
Check the condition of PTO shaft and if
need be replace
Oil leak in gear
Not tight assembly
Examine tightness and check oil level