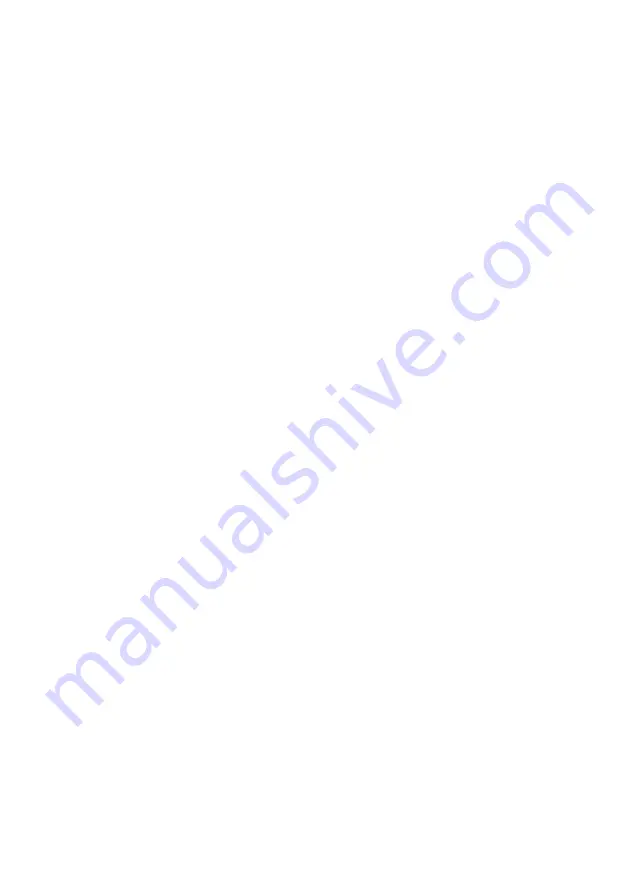
13
7. Final Commissioning
- Flush all air from pipework before connecting AccuBoost unit
- Connect AccuBoost unit to pipework
- Close all outlets and ensure isolation valve(s) are open to and from the AccuBoost
- Turn on stopcock to begin filling the vessel
- Turn on the electrical supply to the pump (if applicable). The pump will begin to run to help
fill the vessel
- Open each outlet that is supplied by the AccuBoost system until all air has been expelled
- Close all outlets and allow the vessel to fully fill. The fill time of the vessel depends on
the mains water flow and also the size of the vessel
- The pump (if applicable) will continue to run even when all outlets are closed, until the
vessel is full and the correct system pressure has been reached
- The AccuBoost (including pump if applicable) and all system pipework should be checked
for leaks whilst the vessel is filling, when the vessel is full and while water is being drawn
from an outlet. Any leaks should be rectified and then the checks performed until no leaks
are present.
Note: The pump responds to the pressure within the system. When the system pressure drops
below the pre-programmed level due to an open outlet, it will automatically turn on. If a small
amount of water is drawn from the system that does not allow the pressure to drop below
the pre-programmed level, the pump will not turn on. When outlets are closed the pump will
continue to run until the vessel has filled to the correct pressure.
If you have any queries regarding the installation of AccuBoost please call PumpWise on
0191 516 2002
It is critical to discharge water through the pump into a container using natural flow before
connecting the outlet of the pump to the pipework. This ensures the air has been discharged
from the inlet pipe work and pump chambers. The best method is :-
- Connect the inlet pipework to the inlet anti-vibration hose
- Check that all isolating valves on anti-vibration hoses are open
- Turn on stopcock and allow water to flow from the pump outlet anti-vibration hose into a
suitable container (such as a bucket)
- Turn off the stopcock and connect the pump outlet anti-vibration hose to the pipework
DO NOT RUN PUMP DRY- to do so will cause irrepairable damage to your pump and will
invalidate your warranty
Priming (pumped versions only)
For all units