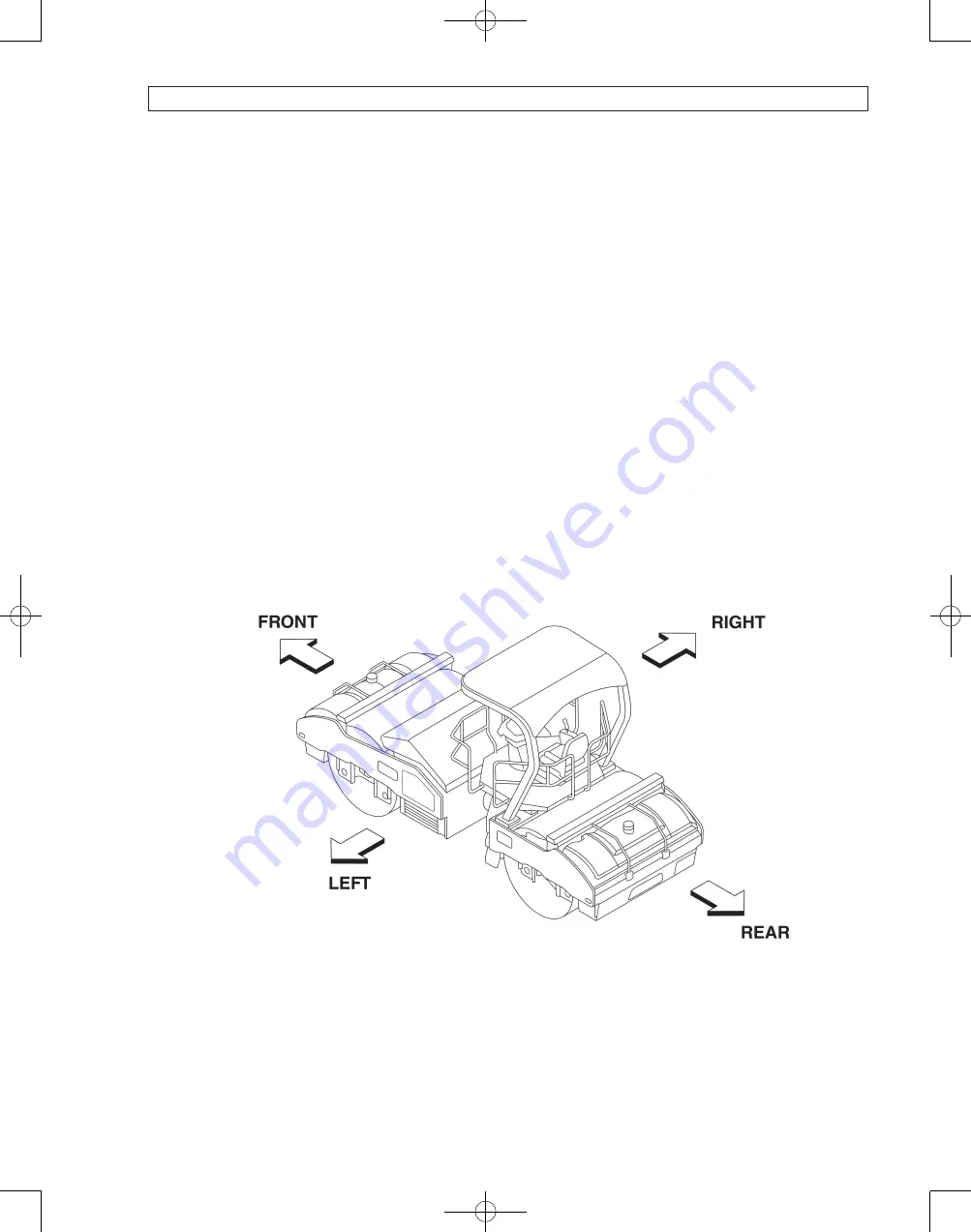
PREFACE
PREFACE
This operator’s manual serves as a guide for the use of your SAKAI SW880
-1
, SW990
-1
Vibrating Roller for those who are new to the machine, and also for the people who have
experience in using the machine and want to refresh their knowledge for the machine.
Read this manual thoroughly and try to fully understand the information before operating your
machine. Keep this handbook at hand whenever you do your work.
When an instruction manual is lost or is damaged and is not legible, replace it immediately.
The main subjects of this manual are:
(1) Basic precautions for safety, (2) Operation, (3) Daily maintenance and (4) Specifications.
For operation and maintenance of the engine, refer to the Engine Instruction Manual
furnished separately. Descriptions in this manual can differ from the machine instructions of
your machine due to the results of the investigation and improvement in its design. If you have
any inquiry regarding your Machine or this manual, contact our distributors.
SW880
-1
, SW990
-1
Summary of Contents for SW880-1
Page 4: ......
Page 82: ...3 PERIODIC MAINTENANCE 78 3 3 Periodic Maintenance Points...
Page 101: ...3 PERIODIC MAINTENANCE 97...
Page 104: ...3 PERIODIC MAINTENANCE 100...
Page 110: ......