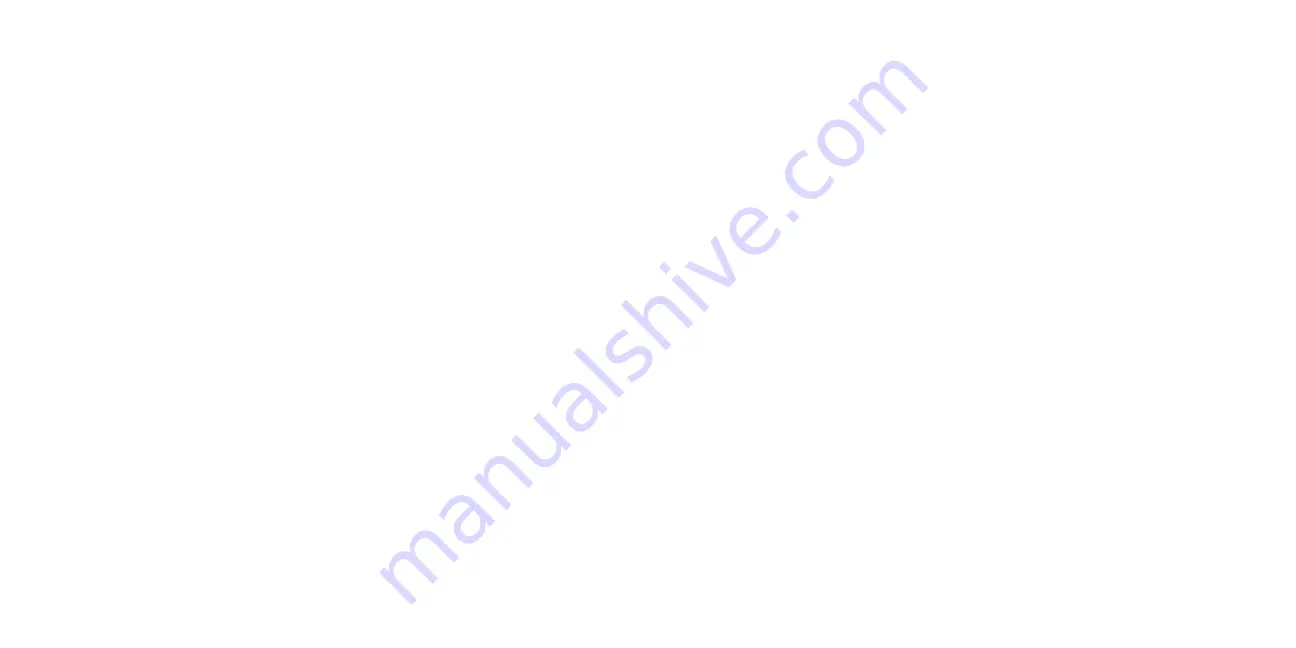
Needle Issues
The needle is breaking:
Ensure the needle is large enough for the thickness and type of leather being sewn. Also make
sure the point of the needle is the correct type for the material being sewn.
Needles will also snap if there are jams or tangles in the bobbin. Before installing your bobbin
make sure it is wound correctly and unwinds smoothly.
The needle hits the needle throat plate when reversing sewing directions:
This is most likely caused by a bent needle. To avoid bending needles when changing sewing
direction, stop the machine with the needle positioned either at the top or bottom of its stroke.
When the needle is completely up, the foot can move the material but cannot bend the needle.
When the needle is completely down, the outer portion of the walking presser foot is up and
cannot move the material which also would bend the needle.
The Power Plus™ Flywheel rotates, but the needle does not penetrate
the fabric:
The Posi-Pin
®
clutch may slip if the pin is not pushed all the way into the bushing hole that locks
the bushing to the Power Plus Flywheel or if the bushing itself is loose.
1.
Make sure the spring-pin is properly inserted.
2.
If slipping still occurs, remove the Posi-Pin nut (p. 77,
2
), pull out the spring-pin (
1
,
3
&
5
),
and slide the Power Plus Flywheel (
6
) off the bushing.
3.
Use a 2.5mm Allen wrench to tighten the two set screws (
17
) that fasten the bushing to the
machine’s upper shaft, then reinstall the Power Plus Flywheel and check for proper operation.
Bobbin Winding Issues
The bobbin is not filling evenly, either too much thread on the top or bottom:
Refer to p. 27 on “Winding Bobbins”. Locate the bobbin tensioner (p. 27,
44
C
) and loosen the
screw just under the tensioner on the front of the machine. Move the tensioner down if the bobbin
is filling with too much thread on the top. Move the tensioner up if there is too much thread on the
bottom. Tighten the screw after correct positioning.
The bobbin winder stops before the bobbin is full or after the bobbin has
too much thread:
There is a bobbin stop (p. 67,
3
) right next to the bobbin winder. It disengages the bobbin winder
when a certain thread level is reached. Simply loosen the screw found on top of the black lobe
and turn the stop to change the thread level. Turning it will either push the bobbin away earlier or
later. Tighten the screw once the correct position is found.
Stitch Master
®
Guidebook: Troubleshooting
56
55