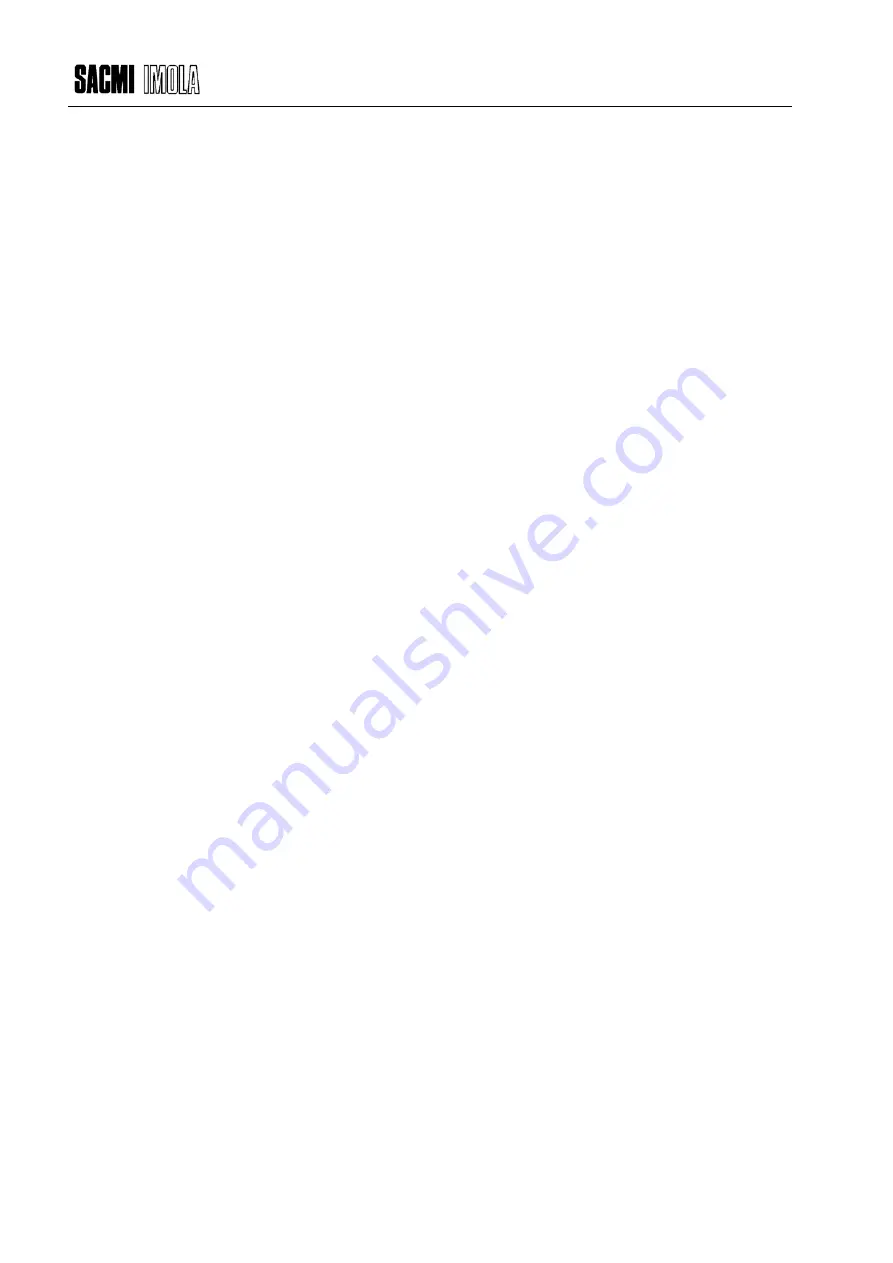
CHS100.86.011 Rev.02 Date 23/07/2018
30
STOPPAGE MESSAGES
2001 CYCLE STOP BUTTON (STOPPAGE)
The automatic cycle stop button was pressed during the automatic cycle.
2002 CAP FEED LINE NOT READY (OKR3M) (STOPPAGE)
The cap feed line did not provide the trigger pulse signal in “Automatic-Local” mode.
Input OKR3 is open; this input must be closed so as to start the cap feed line in automatic
mode.
2003 OVERTEMPERATURE INSIDE CABINET (ST113) (STOPPAGE)
The temperature inside the CHS cabinet has been higher than the threshold set for
thermostat ST113 for 5 consecutive minutes.
Make sure air conditioner EV113 works efficiently.
Make certain thermostat ST113 is properly set and works efficiently.
2004 CHECK VACUUM PUMP/JET STREAM BLOWER (M11/M32) (STOPPAGE)
A fault has been found in the feed circuit of the vacuum suction devices or of the blower (if
provided).
Make sure the overload cut-outs have not tripped.
Make sure the suction circuits or the cap feed blower are operating efficiently.
2005 NO TRIGGER PULSE FROM THE LINE (OKR3) (STOPPAGE)
The line did not provide the trigger pulse signal in “Automatic-Remote” mode.
Input OKR3 is open; this input must be closed so as to start the line in automatic mode.
2006 NO TRIGGER PULSE FROM CVS (STOPPAGE)
The vision system is not inspecting. Check the CVS settings and data items.
2007 OVERTURNED CAPS ENTERING MACHINE (SQ2, SQ2S)(STOPPAGE)
An overturned cap was found in the machine infeed side during the cycle.
An inconsistency was found in photocells SQ2 and SQ2S in the feed channel.
Remove the overturned cap and restart the line.
Make sure photocells SQ2 and SQ2S are in the correct position and are properly set.
2008 CHECK SPARK-TESTER (STOPPAGE)
The control system for micro-holes (spark tester) is either off or deactivated.
Make sure the spark tester is properly connected and operates efficiently.
2009 CHECK REJECT ON SPARK-TESTER (STOPPAGE)
The spark tester consecutively rejected too many caps during the automatic cycle.
Make sure the spark tester operates efficiently and test voltage is properly set.