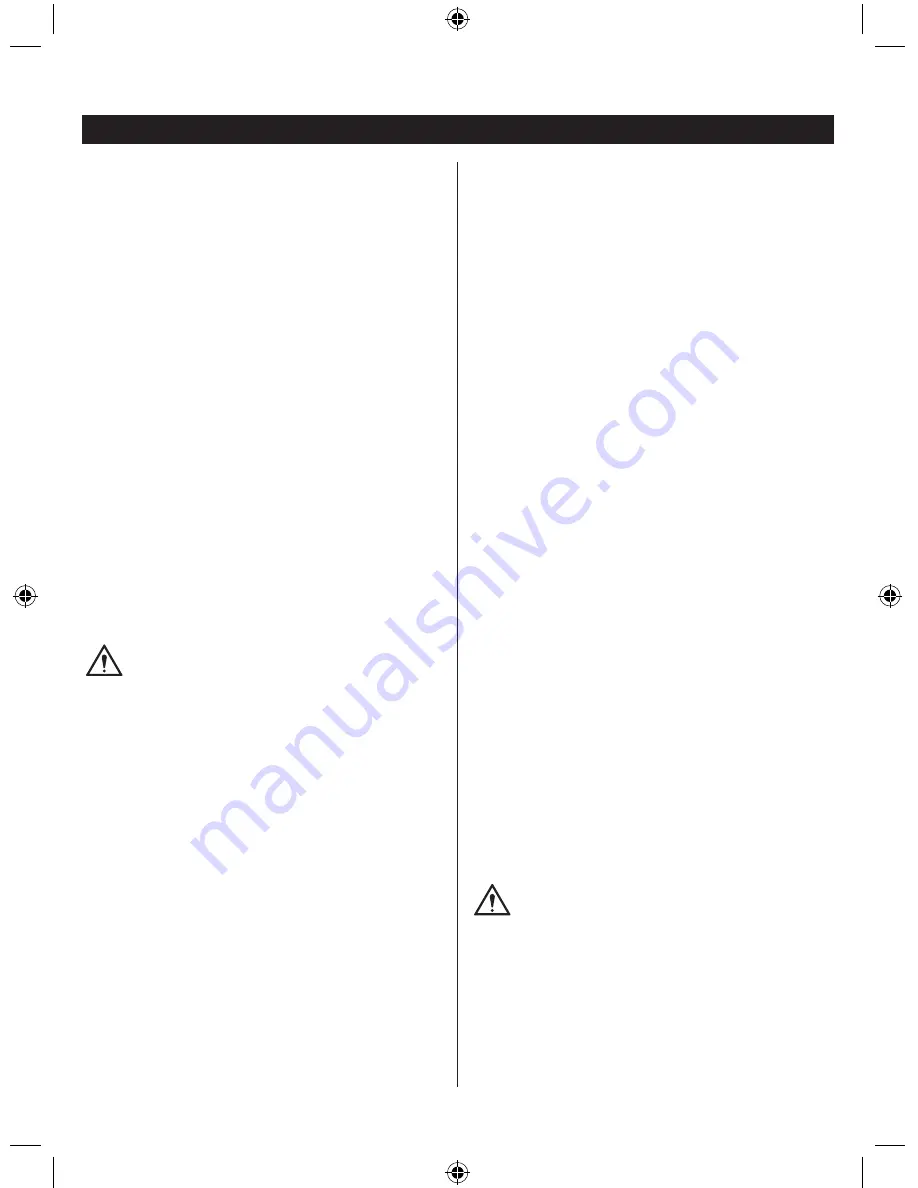
20
English (Original Instructions)
n
HOOK – “Grabs” and dulls quickly; increases the
potential of KICKBACK. Results from using a file with
a diameter too small or a file held too low.
n
BACKWARD SLOPE – Needs too much feed
pressure; causes excessive wear to the bar and
chain. Results from using a file with a diameter too
large or file held too high.
MAINTAINING DEPTH GAUGE
CLEARANCE
See Figures 54 - 56.
n
Maintain the depth gauge at a clearance of 0.64mm.
Use a depth gauge tool for checking the depth gauge
clearances.
n
Every time the chain is filed, check the depth gauge
clearance.
n
Use a flat file and a depth gauge jointer to lower
all gauges uniformly. Use a 0.64mm depth gauge
jointer. After lowering each depth gauge, restore
original shape by rounding the front. Be careful not to
damage adjoining drive links with the edge of the file.
n
Depth gauges must be adjusted with the flat file in the
same direction the adjoining cutter was filed with the
round file. Use care not to contact cutter face with flat
file when adjusting depth gauges.
MAINTAINING THE GUIDE BAR
See Figure 57.
WARNING
Check that the switch is in the STOP “0” position
on the saw.
Every week of use, turn over the guide bar on the saw to
distribute the wear for maximum bar life. The bar should
be cleaned every day of use and checked for wear and
damage. Feathering or burring of the bar rails is a normal
process of bar wear. Such faults should be smoothed
with a file as soon as they occur.
A bar with any of the following faults should be replaced:
n
Wear inside the bar rails that permits the chain to lay
over sideways
n
Bent guide bar
n
Cracked or broken rails
n
Spread rails
Lubricate guide bar sprockets weekly. Using a grease
syringe, lubricate weekly in the lubricating hole. Turn the
guide bar and check that the lubrication holes and chain
groove are free from impurities.
CLEANING THE AIR FILTER
See Figures 58 - 59.
n
Activate the chain brake.
n
Remove the two screws holding the Engine cover.
n
Lift the front of the Engine cover past chain brake
lever.
n
Lift the back of the Engine cover past the handle.
n
Before removing the air filter from the carburettor,
blow or brush as much loose dirt and sawdust from
around the carburettor and chamber as possible.
Note:
Make sure to pull the choke rod out to keep the
carburettor from being contaminated.
n
Lift the air filter off the air filter base.
Choose one of the following cleaning options:
n
To lightly clean, tap the filter against a smooth, flat
surface to dislodge most saw dust and dirt particles.
n
After every 5 hours of operation, clean in warm soapy
water, rinse, and let dry completely. Replace with a
new filter after every 25 hours of use.
Note :
An alternate method is to clean the filter with
compressed air. Always wear eye protection to avoid
eye injury.
n
Reinstall the air filter.
Note :
If you use an air hose for drying, blow through
both sides of filter.
CAUTION:
Make sure the air filter is correctly replaced before
reassembly. Never run the engine without the air filter,
serious damage could result.
CLEANING THE STARTER UNIT
See Figure 60.
Use a brush to keep the cooling vents of the starter
assembly free and clean of debris.
ADJUSTING THE CARBURETTOR
See Figure 61.
Before adjusting the carburettor:
n
Use a brush to clean the starter cover vents.
n
Clean the air filter. Refer to
Cleaning the Air Filter
in
the
Maintenance
section of this manual.
n
Allow the engine to warm up prior to adjustment of
engine idle speed.
WARNING:
Weather conditions and altitude may affect
carburetion. Do not allow bystanders close to the
chainsaw while adjusting the carburettor.
Idle Speed Adjustment
- The idle speed adjustment
controls how much the throttle valve stays open when the
throttle trigger is released. To adjust:
n
Turn idle speed screw
“T”
clockwise to increase idle
speed.
n
Turn idle speed screw
“T”
counter clockwise to
decrease idle speed.