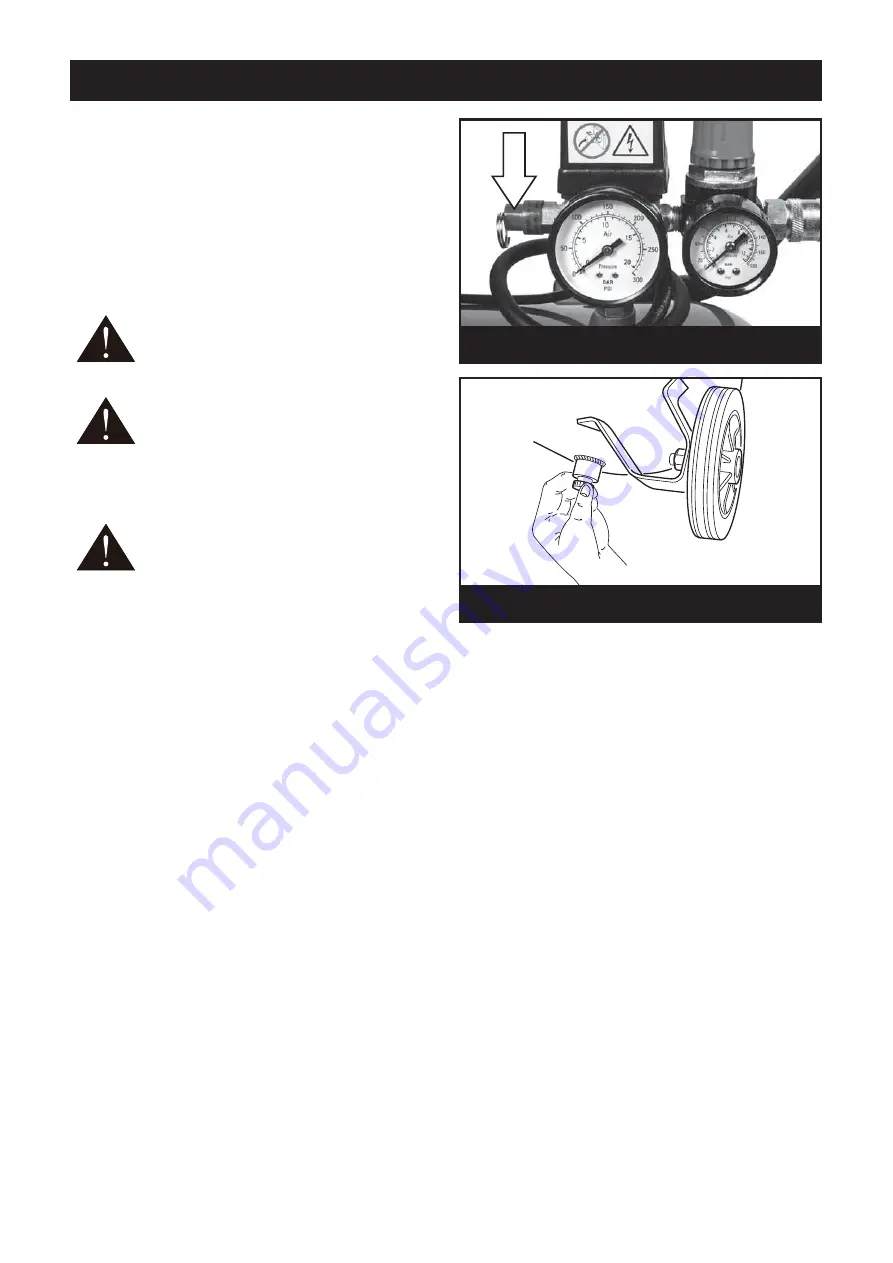
12
OPERATION
SAFETY VALVE
Check the operation of the safety valve, under
pressure, daily by pulling the ring as shown in
Fig.14. Air should be released when you pull the
ring and stop when the ring is released.
•
If the valve does not operate as described, or
if the valve is stuck, it must be replaced by
qualified service personnel before using the
compressor.
WARNING.
Do not remove or attempt to
adjust the safety valve.
DANGER.
Do not attempt to tamper with
the safety valve. Anything loosened from
this device could fly up and hit you.
Failure to heed this warning could result
in death or serious personal injury.
DRAINING THE RESERVOIR
CAUTION.
It is important to drain the
reservoir before storage to help prevent
tank corrosion.
Switch the air compressor off, by pressing the
On/Off button to the off position (pressed down),
and remove the plug from the mains supply.
Pull the ring on the safety valve to release pressure
until pressure gauge reads less than 20 psi.
Release the ring.
Place a suitable container beneath the compressor
to catch any condensation.
Carefully undo the drain valve nut anti-clockwise
until you hear a hissing noise, this is the reservoir
depressurising (Fig.15).
When the gauge indicates zero and the hissing has
stopped, tighten the drain valve nut again.
OIL CHANGING
Replace the oil after the first 100 hours of
operation and every 300 hours subsequently.
Remember to check the oil level at regular
intervals.
For changing the pump oil, be sure to do the
following:
1. Turn the unit off and unplug the power cord
from the receptacle.
2. Allow the compressor time to cool if it has been
in operation.
3. Open the drain valve to bleed all air from the
tank.
4. Close the drain valve.
5. Remove the dipstick on the pump.
6. Remove the oil drain plug with a box end
wrench or socket. Drain the oil into a suitable
container and dispose of properly. The
compressor may need to be tipped slightly
towards the drain hole to allow all of the oil to
drain.
7. Reattach the oil drain plug.
8. Refill the compressor pump with an air
compressor oil such as SAE-30 non-detergent
(API CG/CD Heavy Duty) oil at slow intervals
until the oil reaches between the minimum and
maximum marks on the dipstick. Take care not
to exceed the maximum mark. Use SAE-10
during extreme winter conditions.
Fig. 14
Fig. 15