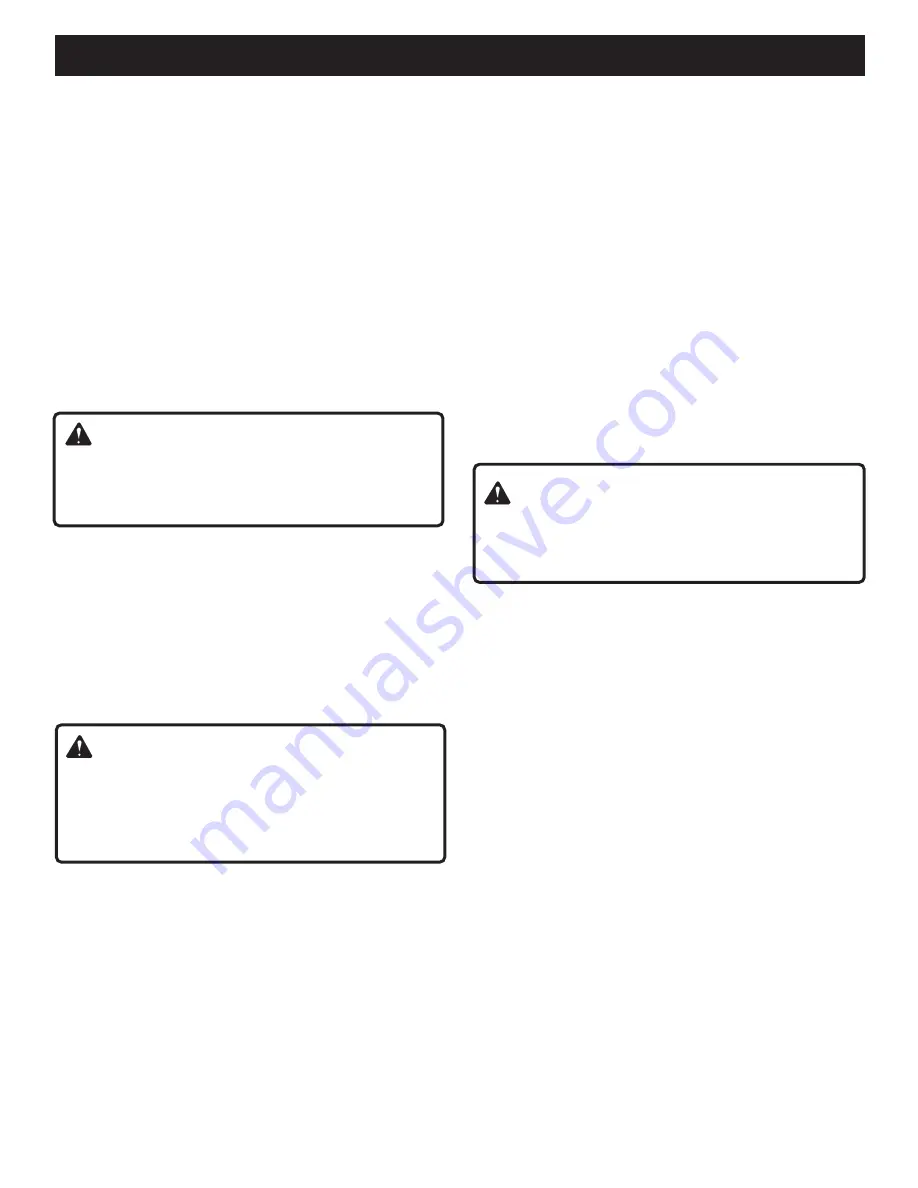
17
UK
Choose one of the following cleaning options:
9.
To lightly clean, tap the filter against a smooth, flat surface
to dislodge most saw dust and dirt particles.
10.
For a more thorough cleaning, clean in warm soapy water,
rinse, and let dry completely.
NOTE:
An alternative method is to clean the filter with
compressed air (always wear eye protection to avoid
eye injury).
11.
Reinstall the air filter, making sure that the tabs on the air
filter are located in channels on the air filter bottom before
tightening filter retainer screw.
■
Clean the pre-filter (
D
) every 25 tanks of fuel or sooner, if
required. Remove the cylinder cover (
B
), starter assembly
(
E
) and the fan housing baffle (
F
) for access to the pre-filter
in the engine housing.
NOTE:
If you use an air hose for drying, blow through both
sides of filter.
CAUTION:
Never run the engine without the air filter: serious
damage could result.
Make sure the air filter is correctly placed in the air filter
cover before reassembly.
CLEANING THE STARTER UNIT
See Figure 67.
Use a brush or compressed air to keep the cooling vents of the
starter assembly free and clean of debris.
CLEANING THE ENGINE
See Figures 68 and 69.
Clean the cylinder fins and flywheel fins with compressed air or
a brush periodically. Dangerous overheating of the engine may
occur due to impurities on the cylinder.
WARNING
Never run the saw without all the parts, including the
drivecase cover and starter housing, securely in place.
Because parts can fracture and pose a danger of thrown
objects, leave repairs of the flywheel and clutch to trained
Ryobi service dealer personnel.
NOTE:
Depending on the type of fuel used, the type and amount
of oil used, and/or your operating conditions, the exhaust port
and silencer may become blocked with carbon deposits. If you
notice a power loss with your petrol-powered tool, you may
need to remove these deposits to restore performance. We
highly recommend that only qualified service technicians
perform this service.
CHECKING THE FUEL FILTER
See Figure 70.
Check the fuel filter (
A
) periodically. Replace it if contaminated
or damaged.
REPLACING THE SPARKING PLUG
See Figure 71.
This engine uses a Champion RCJ-4 with 0.63 mm
(0.025”) electrode gap. Use an exact replacement and replace
every six months, or more frequently if necessary.
1.
Loosen the sparking plug by turning it anticlockwise with
a spanner.
2.
Remove the sparking plug.
3.
Hand-thread the new sparking plug, turning it clockwise.
NOTE:
Be careful not to cross-thread the sparking plug.
Cross-threading will seriously damage the product.
CLEANING THE SPARK ARRESTING
SILENCER
See Figure 72.
The silencer (
A
) is equipped with a spark arrester screen (
B
).
A faulty spark arrester screen can create a fire hazard. Through
normal use the screen can become dirty and should be
inspected weekly and cleaned as required. Always keep the
silencer and spark arrester on your saw in good condition.
WARNING
Silencer surfaces are very hot during and after operation
of the chainsaw. Keep all body parts away from the
silencer. Serious burns may occur if contact is made with
the silencer.
1.
Allow the silencer to cool.
2.
The spark arrester screen (
B
) is retained by the deflector
(
C
). Remove the nuts (
D
) and screen retainer to access
the spark arrester screen.
3.
Replace the spark arrester screen if it is cracked or
otherwise deteriorated.
CHAIN BRAKE
See Figures 73 and 74.
■
■
■
■
■
Remove the clutch cover and clean the chain brake
components. Check wear on the brake band (
A
). If brake
band is worn or deformed, have it serviced at your nearest
authorised service dealer. The band thickness should not
be less than 0.60 mm (0.024 in.), or worn halfway through.
■
■
■
■
■
Always keep the chain brake mechanism clean (
B
) and
lightly lubricate the linkage (
C
).
■
■
■
■
■
Always test the chain brake performance after servicing or
cleaning. Refer to “Operation – Operating Chain Brake”
earlier in this manual for additional information.
■
■
■
■
■
Check and, if damaged, replace the chain catcher (
D
).
MAINTENANCE