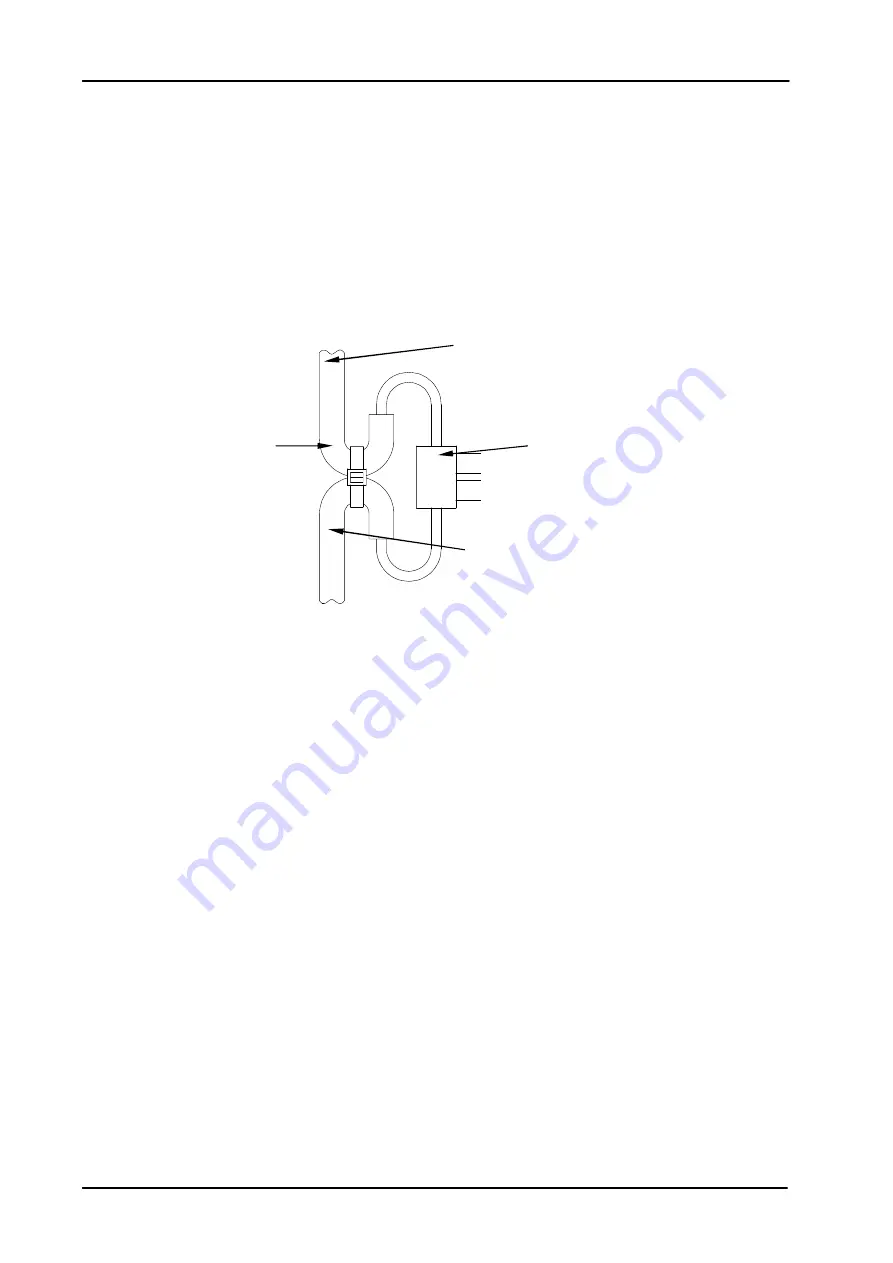
Rutland FM1803-2
Installation & Operation
Document No: SM-146 Issue D 14.03.08
Marlec Engineering Co Ltd
20
FITTING THE GENERATOR TO THE TOWER
Connect the wind generator flying leads to the cable protruding from the tower
using the connector block supplied or other suitable connector.
(The generator
output is 3 phase ac, therefore these connections can be made in any sequence)
.
Wrap the connection with insulation tape to secure/protect from the environment.
It is recommended that cable restraint is fitted to prevent the weight of cable
applying excessive load to the connections, a simple method of achieving this is
shown in Fig 11.
Carefully locate the wind generator post adaptor into the top of the tower
ensuring the flat on the post adaptor aligns with the pipe seam if necessary.
Push the adaptor into the tower while the cable is gently pulled from the tower
base to ensure it is not trapped, continue until the post adaptor is fully inserted
into the tower and the fixing holes align.
Secure the wind generator to the tower using the four M12 x 25mm screws and
shakeproof washers provided. Tighten using an 8mm Allen key.
Final Mechanical Check
Check the tightness of the blade screws and nose dome.
Check the free rotation of the hub and yaw axis.
Check for free movement of the tail fin.
Connector Block
Cable Tie
Cable From WG
Fig 11. Cable strain relief
Cable to Controller