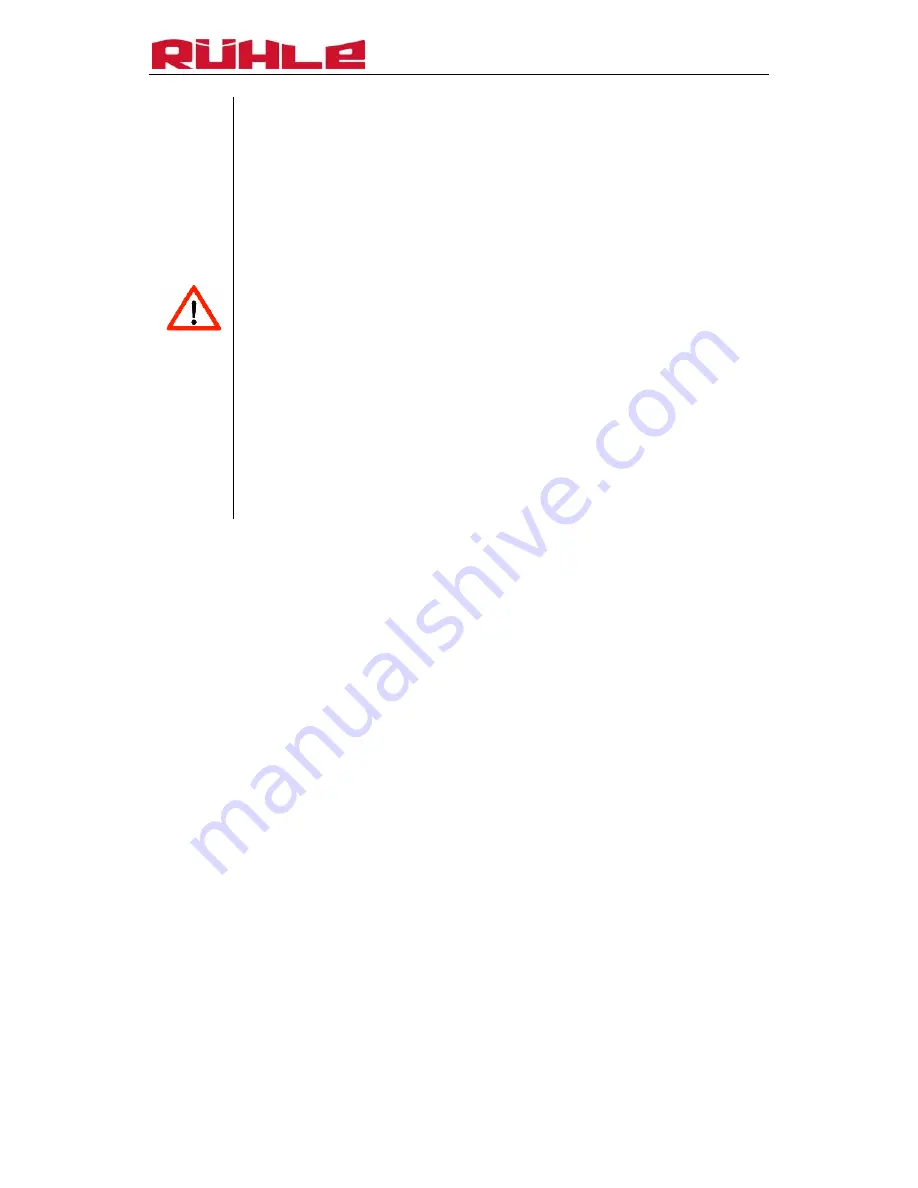
Injector IR 29
11
Cleaning with high-pressure cleaners
is permitted only for:
all external surfaces (all outside stainless steel sur-
faces + machine bases),
reach-protection (inlet),
reach-protection (outlet),
curing chamber door,
softer,
needle bar,
transport belt
filter
The control panel must be cleaned manually and may not
be exposed to a water jet!
All other parts and surfaces may be cleaned only with
normal water pressure!