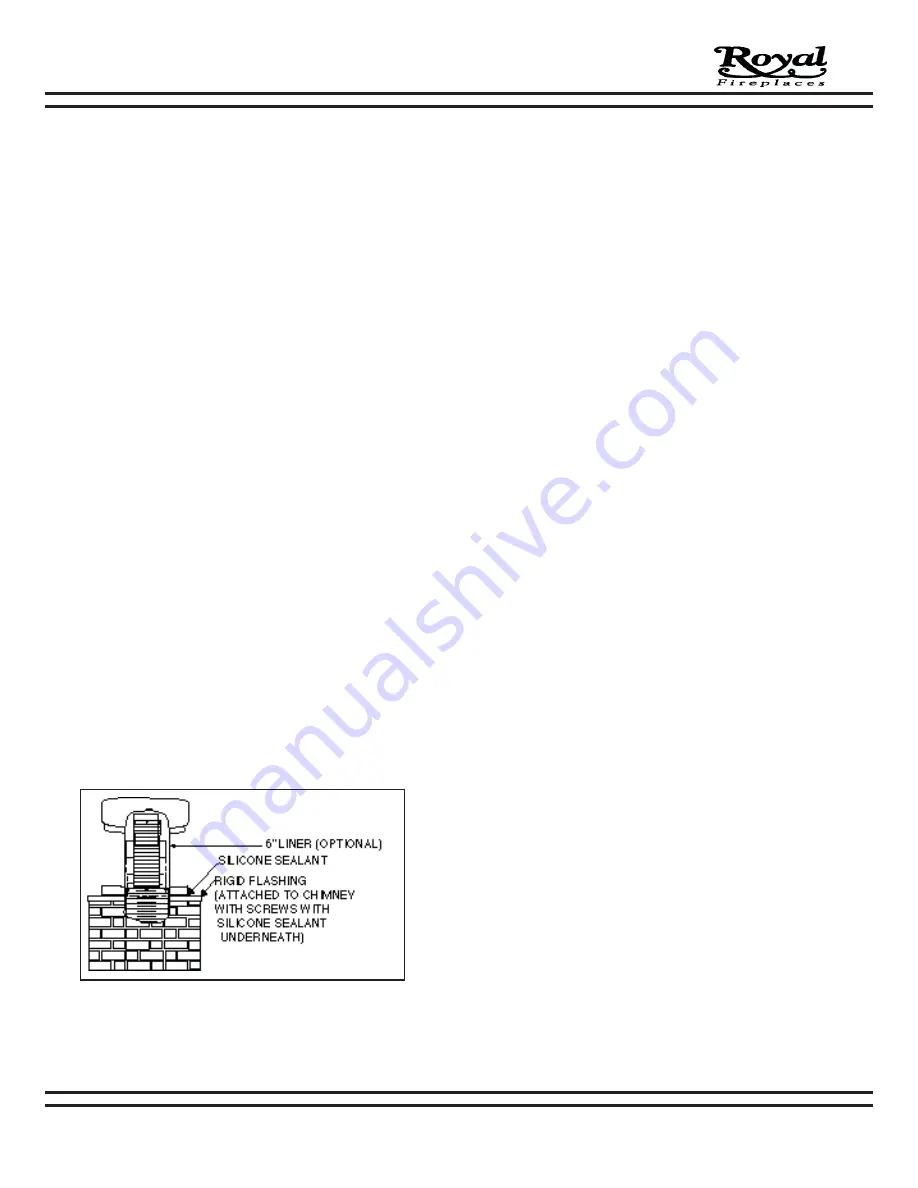
12-99
15 30750B
R-CAST SERIES WALL FURNACE
(Existing Masonry Chimney Installation
Requirements Continued.)
Figure 13
Masonry Termination
D. Existing Class A Metal Chimney
Termination.
In many cases where an R-CAST is replacing a
woodstove, much of the existing Class A Metal
Chimney can be incorporated into the direct vent sys-
tem.
The existing chimney must comply with NFPA-211
codes and any local code requirements.
The chimney should be cleaned and examined to
verify it is unobstructed and in good structural
condition. Any structural weaknesses such as
cracks, leaky joints, corroded or warped surfaces
can have an adverse effect on the performance of
this heater and should be replaced or repaired.
Whenever an existing Class A Metal Chimney is on
an outside wall, removal of the chimney and the use
of the minimum horizontal direct vent termination kit
may be less expensive.
When using an existing Class A Metal Chimney the
following requirements are necessary:
Minimum size diameter is 6 inches.
Minimum height from the base of the stove to the top
of termination cap is 9 feet.
The vent from the top of the heater to the Chimney
must be rigid vent sections. A 4'' UL 1777 listed gas
vent aluminum flexible liner can be used inside the
chimney. The flexible liner must be secured to the
last rigid section with three [3] sheet metal screws. A
minimum 3 inch overlap is required. Remove and
discard the existing chimney termination cap.
Determine the length of the 4'' UL 1777 listed gas
vent flex liner required to meet the vent sections at
the top of the heater.
Follow the liner manufacturer’s instructions for
installing the liner in the chimney. Attach a flexible
liner puller to the liner and secure a rope to the puller.
One person should feed the liner through the chim-
ney, and another person should pull the liner from the
bottom, with the rope, guiding the liner down the
chimney. Extend and run the 4'' gas vent liner down
the chimney leaving 10'' extending from the top of the
chimney stack.
Install and secure the vertical termination adapter
onto the chimney.
Place and secure the Termination Cap on the vertical
termination adapter with the screws provided.
See Figure 14.
Measure and record the chimney dimensions to
determine total flexible liner requirements.
Follow the liner manufacturer’s instructions for
installing the liner in the chimney. Attach a flexible
liner puller to the liner and secure a rope to the
puller. One person should feed the liner through the
chimney, and another person should pull the liner
from the bottom, with the rope, guiding the liner down
the chimney. After feeding the liner down the chim-
ney, form a 90˚ angle and bring the liner through the
hole in the chimney wall. (If running two liners, run
the 6” liner first and then the 4” inside of it.) Extend
the liner through the wall of the chimney and attach it
to the venting system extending from the top of the
heater.
Construct a metal flashing large enough and strong
enough to cover the chimney opening and support
the heater Vertical Termination Cap. The flashing
needs to fold down over and around the outside of
the masonry chimney so that it can be secured to the
chimney by 4 screws. See Figure 13. The flashing
will require a hole at least 6
1
/
2
'' in diameter. (If using
a 6” liner, extend the 6'' flexible liner through the
flashing and attach it to the vertical termination
adapter. Secure the vertical termination adapter to
the flashing with the screws provided and seal the
vertical adapter/flashing joint with a silicone sealant
to prevent moisture from running down the liner into
the chimney.
Attach the 4'' gas vent liner to the vertical termina-
tion cap with screws provided, then attach the
Termination Cap. See Figure 13.