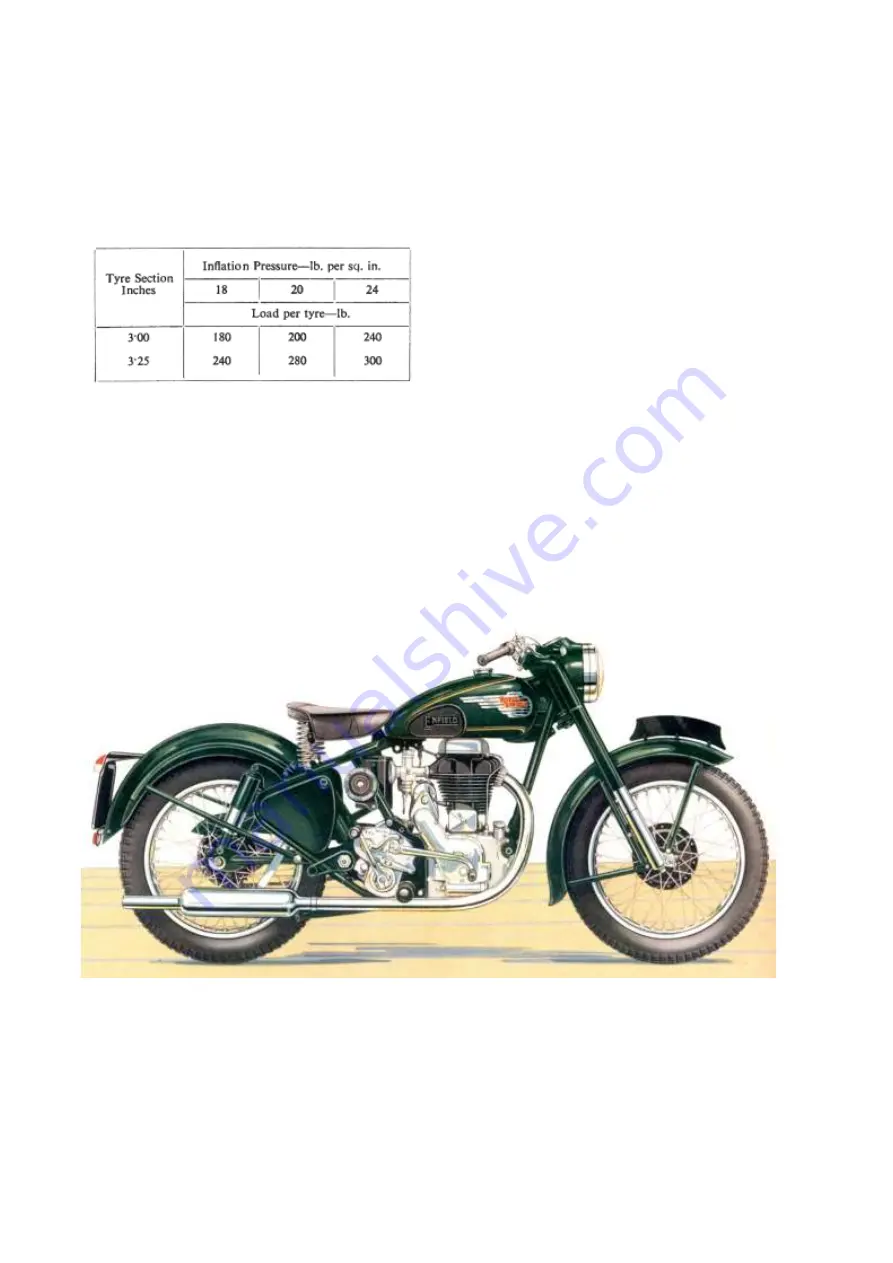
Page 57
ROYAL ENFIELD 350cc and 500cc O.H.V. WORKSHOP MANUAL
16. Tyre Pressures
The load which the tyre will carry at different
inflation pressures is shown below :
17. Lubrication
A greasing point is provided in the centre of the
hub barrel. Unless the barrel is packed full with
grease on assembly (which is apt to lead to trouble
through grease finding its way past the felt seals on to
the brake linings) this greasing point is of little value
and the best way to grease the bearings is by packing
them with grease after dismantling the hub as
described above.
Note
that the brake cam is drilled for a grease
passage but the end of this is stopped up with a
countersunk screw instead of being fitted with a
grease nipple. This is done to prevent excessive
greasing by over-enthusiastic owners. If the cam is
smeared with grease on assembly it should require no
further attention but in case of necessity it is possible
to remove the screw, fit a grease nipple in its place
and grease the cam by this means.
350 CLIPPER OTHERWISE KNOW AS MODEL G DELUXE
1956
www.hitchcocksmotorcycles.com