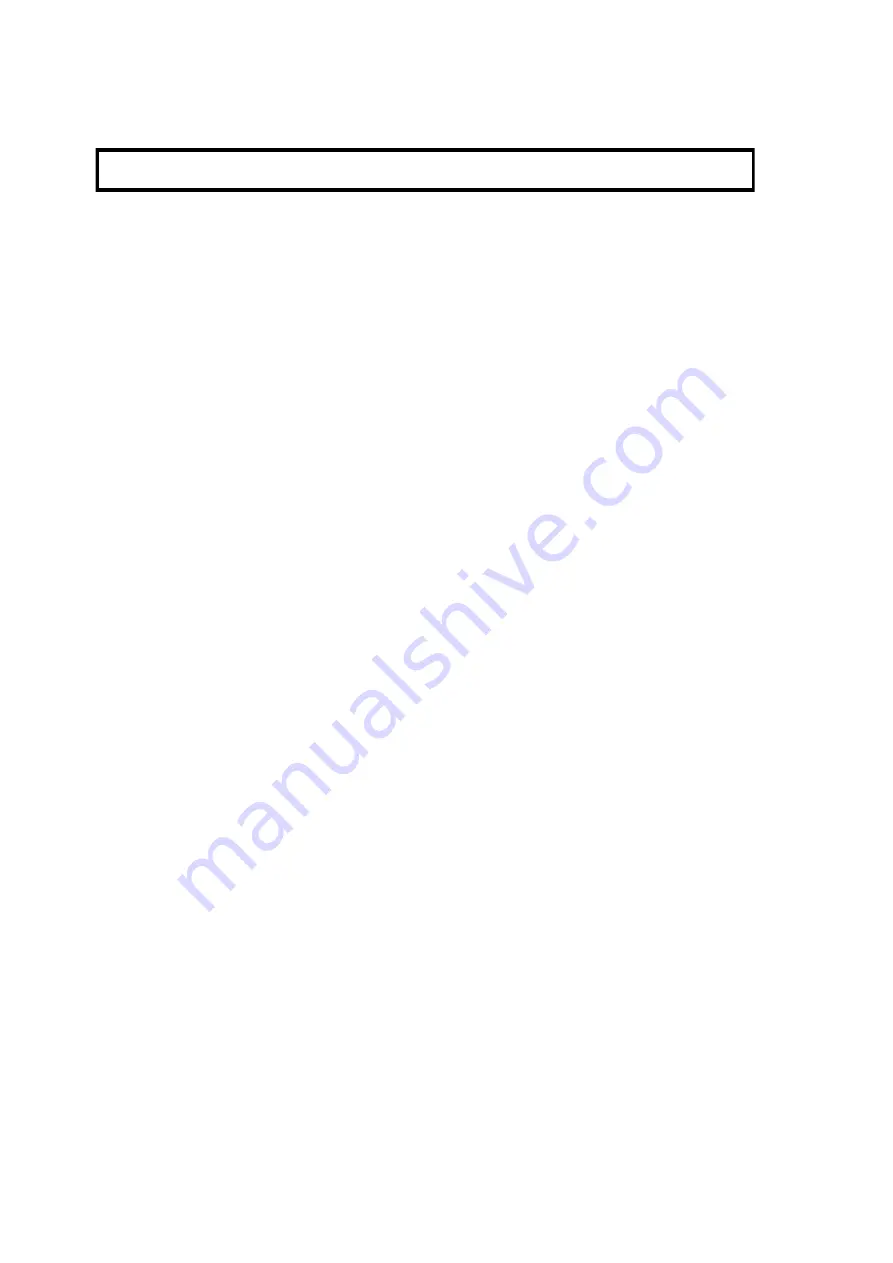
ROYAL ENFIELD WORKSHOP MANUAL
PAGE 19
C18
12. Removal of Carburettor
Disconnect the petrol pipe from the float
chamber and remove the two nuts holding the
carburettor to the cylinder head.
Where fitted disconnect the air filter sleeve
from the carburettor intake, push the sleeve to
one side and draw the carburettor back clear of
the studs.
Remove the throttle and air slides.
13. Removal of the Cylinder Head
Remove the petrol tank as described in
Subsection 4.
Disconnect the engine steady.
Remove the exhaust pipe.
Disconnect the plug lead and oil pipe.
Push the carburettor back, clear of the studs,
after removing the fixing nuts.
Remove the rocker box cover as described in
Subsection 3.
Turn the engine until both valves are
closed.
Remove the rockers and bearings
completely.
(a) Early Models : Remove the four ¼ in. nuts
on each bearing block, or
(b) Later Models : Remove the four ¼ in.
nuts and the single central
5
/
16
in. nut from the
bearing housing.
Lift out the push rods. (Note: It is possible
to extract the push rods without dismantling the
rockers if the cylinder head is lifted slightly first.)
Remove the four sleeve nuts inside the rocker
box and the single plain nut near the plug hole.
Earlier alloy heads have in addition a single Allen
screw situated between the two nuts on the push
rod side, and later alloy heads have two Allen
screws in the push rod tunnel. After removal of
the appropriate nuts and screws, the head may be
lifted. To break the carbon seal, tap the head
gently with a hide hammer beneath the exhaust
and inlet ports. Do not tap the fins.
When fitting the head again, first remove the
remains of any old compound and make sure that
the faces are quite clean. Then apply a thin
coating of compound to each side of the gasket.
It is advisable to fit a new gasket each time the
head is removed.
Place the head on the cylinder barrel, and
replace the five washers and nuts, not forgetting
the single Allen screw in the earlier alloy head,
and the two Allen screws in the later one. Tighten
down diagonally from one side to the other to
prevent distortion.
Replace the push rods with the adjustable
parts upwards. The inlet push rod is the one
adjusted to the greater length, and connects the
outside follower to the rear rocker.
Refit the rockers and bearings, making sure
that the oil feed holes of earlier "250 Clippers,"
"Crusader 250's" and "Crusader Sports" are at the
bottom, and that the caps and bases are in line
when tightened down. A sharp tap with a hammer
on the end of the rocker will help to ensure this.
When fitting the one-piece rocker housing, to
be found on later "250 Clipper," "Crusader 250,"
and "Crusader Sports" models, and on all "Super
5," "Continental," "GT", "350 Bullet" and "250
Trials" models, be sure that it is squarely home on
the five studs, then tighten down the nuts evenly.
See that the valve stem caps, where used, are
in place.
See that the rocker box gasket is intact. If
necessary, fit a new one. Replace the rocker box
cover and tighten down the fixing nut.
After the engine has been run long enough to
get thoroughly hot, the tightness of the nuts
should be rechecked.
After tightening the cylinder head nuts with
the engine hot, recheck the rocker clearance at
some convenient time when the engine is cold.
14. Removal of the Valves
Remove the cylinder head and rockers
(Subsection 13). Prise away the hardened steel
thimbles or end caps where these are fitted. If they
have stuck they can be removed by means of a
screwdriver.
Using a suitable compressing tool, compress
the valve springs and remove the split conical
collets from the ends of the valve stems.
Slacken back the compressing tool, and release
the springs.
Withdraw the valves and place the springs, top
spring collars (and bottom collars, if loose), the
end caps and split conical collets separately so that
they may be reassembled, each set with the valve
from which it was removed.
If either of the valves will not slide easily in its
valve guide, remove any slight burrs on the end of
the valve stem with a carborundum stone before
taking the valve out of the guide. If the burrs are
not removed the guide may be damaged.
15. Dismantling the Rockers (later models)
If for any reason the rockers must be
dismantled, it is only necessary to remove one nut
from each spindle. Draw off the washer and
rocker arm and the spindle, complete with the
other rocker arm, may be withdrawn.
When reassembling, note that the rocker with
the rounded end fits on the pushrod side with a
plain washer and nut to secure it.
The broad groove round the rocker spindle
should be nearest to the push rod side, and the
large double spring washer should be between the
rocker bearing and the rocker which bears on the
valve.
16. Fitting New Valve Guides
To remove the valve guides from the head, it is
necessary to have two special tools, which can
easily be made.
The first is a piece of tube with an internal
bore of not less than
7
/
8
in.
The second is a mandrel about 4 ins. long
made from
9
/
16
in. diameter bar with the end
turned down to
11
/
32
in. diameter for a distance of
1
/
2
in. (See Section M.)
Support the cylinder head on the tube, which
fits over the collar of the valve guide. Using the
mandrel, force the guide out of the head with a
hand press or by using a hammer.
To fit a new guide, support the head at the
correct angle and use a hand press and the same
mandrel. If a hand press is not available and the
guide is replaced by a hammer, use the mandrel to
prevent damage to the guide, which is easily
damaged and must be treated with great care.
It is necessary to re-cut the valve seat to the
correct profile and to grind-in the valve after a
guide has been replaced (see Subsection 20).
17. Removal of the Cylinder Barrel
Remove the cylinder head (see Subsection 13).
Lift the barrel off the piston, taking care that
any pieces of broken ring do not drop into the
crankcase.
Before replacing the cylinder barrel, clean off
the joint faces and fit a new paper washer.
18. Removal of the Piston
Remove the cylinder head and cylinder barrel
(see Subsections 13 and 17).
With the tang of a file remove the wire circlip
retaining the gudgeon pin on the left hand or
driving side.
Extract the gudgeon pin using Special Tool
No. E.5477 having first marked the pin so that it,
and the piston, may be replaced the same way
round (the front of the piston is marked).
During this operation put a piece of clean rag
in the top of the crankcase to prevent foreign
matter from getting in. In particular take care not
to drop the circlip in the crankcase.
19. Decarbonising
Having removed the cylinder head, as
described in Subsection 13, scrape away all carbon
gently and avoid scoring the combustion chamber
or the valve seats, taking particular care with an
alloy head which is very easily damaged. Be careful,
too, not to injure the joint face which beds down
on to the head gasket.
Scrape away all carbon from the valve heads
and beneath the heads, being careful not to
damage the valve faces. In clearing the top of the
piston remember that it is made of aluminium
alloy and is easily damaged.
If the piston rings are removed, the grooves
can be cleaned out and new rings fitted. For
cleaning the grooves a suitable tool is a piece of
broken ring thrust into a wooden handle and filed
to a chisel point.
If the piston ring gaps exceed
1
/
16
in. when the
rings are in position in the barrel, new rings should
be fitted. The correct gap for new rings is
.015-.020 in. The gap should be measured in the
least worn part of the cylinder, which will be found
to be at the extreme top or bottom of the bore.
While the cylinder and piston are not in
position, cover the crankcase with a clean cloth to
prevent the ingress of dust and dirt of any kind.
Do not, of course, attempt to scrape the carbon
from the piston when the mouth of the crankcase
is open.
20. Grinding-in the Valves
To grind a valve, smear the seating with a little
grinding in compound, place a light short coil
spring over the valve stem and beneath the head,
insert the valve into its appropriate guide, press it
on to the seat using a tool with a suction.
www.hitchcocksmotorcycles.com
Summary of Contents for 250 CLIPPER
Page 40: ...ROYAL ENFIELD WORKSHOP MANUAL PAGE 40 w w w h i t c h c o c k s m o t o r c y c l e s c o m ...
Page 46: ...ROYAL ENFIELD WORKSHOP MANUAL PAGE 46 w w w h i t c h c o c k s m o t o r c y c l e s c o m ...
Page 52: ...ROYAL ENFIELD WORKSHOP MANUAL PAGE 52 w w w h i t c h c o c k s m o t o r c y c l e s c o m ...
Page 62: ...ROYAL ENFIELD WORKSHOP MANUAL PAGE 62 w w w h i t c h c o c k s m o t o r c y c l e s c o m ...
Page 72: ...ROYAL ENFIELD WORKSHOP MANUAL PAGE 72 w w w h i t c h c o c k s m o t o r c y c l e s c o m ...
Page 76: ...ROYAL ENFIELD WORKSHOP MANUAL PAGE 76 w w w h i t c h c o c k s m o t o r c y c l e s c o m ...
Page 88: ...ROYAL ENFIELD WORKSHOP MANUAL PAGE 88 w w w h i t c h c o c k s m o t o r c y c l e s c o m ...