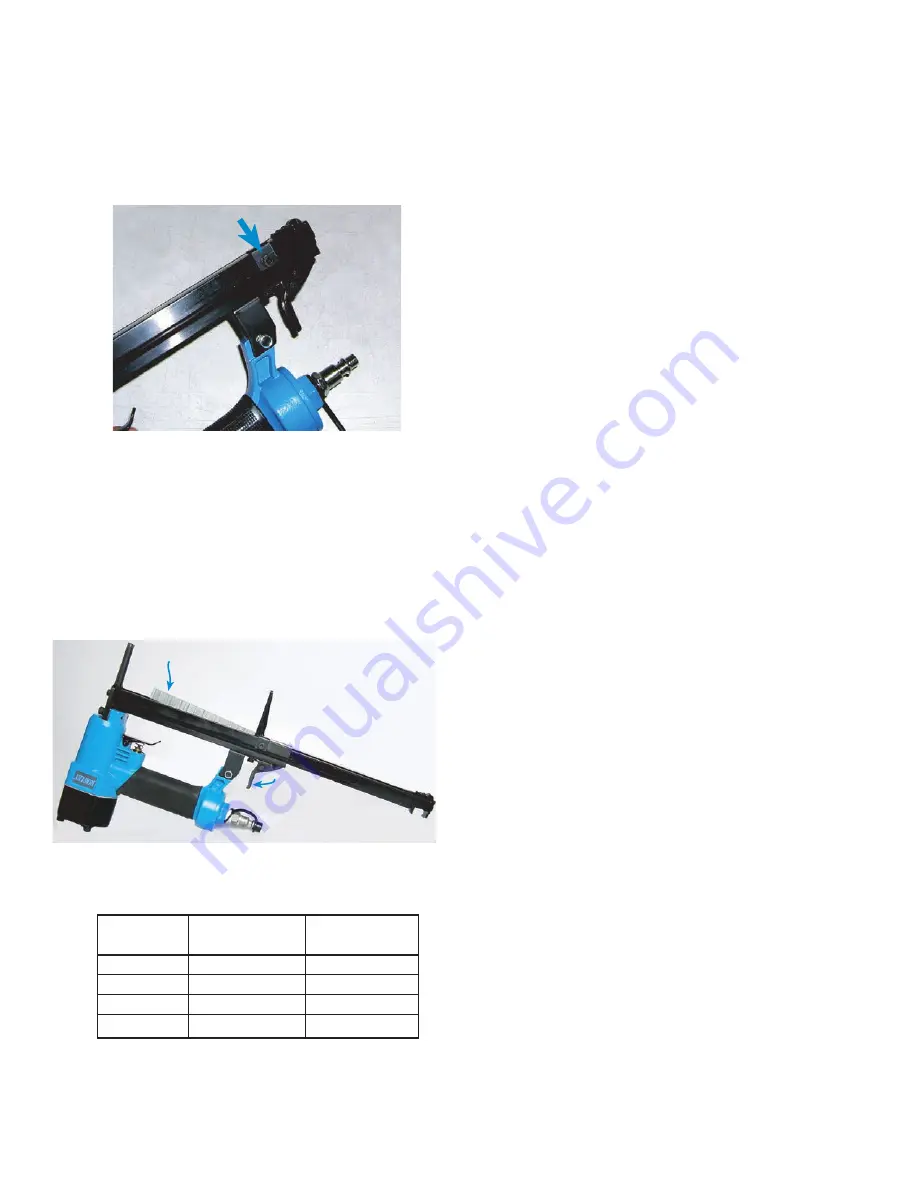
5) Shoot Staples:
Caution:
Always wear safety glasses and ear plugs.
1. Connect the stapler to the air supply.
2. Regulate air pressure to 70 psi.
3. Rotate trigger safety to the side. Test stapling
action by driving a few staples into a piece of
wood.
Note:
Do not press the stapler firmly against the
stapling surface to fire staples. The compressed
air is sufficient to drive the staples in. Just lightly
rest the stapler nose against the stapling surface
and press the trigger. Pressing stapler firmly
against the surface will cause the staples to
penetrate too deep, cut fabrics and could damage
both stapling surface and stapler piston. Apply
slightly more pressure only when stapling through
very thick layers of fabrics to wood.
4. If staples are still driven too deep, first try to tilt the
stapler slightly, so stapler nose is at an angle from
the stapling surface. If this does not correct the
problem, the air pressure may be too high. Adjust
the air regulator to reduce the pressure, then try
again.
5. If staples do not penetrate sufficiently, especially
when stapling into hardwood or if stapler misfires
occasionally, or the piston does not return to full
up position at the end of cycle, the air pressure
may be too low. Adjust regulator to increase air
pressure gradually and try again.
Warning:
Do not exceed maximum operating pressure of
100 psi.
6. After use, always disconnect stapler from air
supply and unload the staples.
4) Load Staples (Fig. 7):
1. We strongly suggest using staples from Rowley
Co. See size chart below.
2. Make sure tool is
not
connected to air supply.
3. Turn tool upside down. Depress the magazine
latch, and magazine cover will slide open.
4. Drop in a strip of staples with staple legs pointing
up.
5. Push the magazine cover forward until latch
catches.
Staples:
The following Rowley Co. staples fit both
NS10
and
NS11
.
3) Make Sure All the Screws Are Tight:
Make sure the screw holding the L bracket (
Fig. 6
) is
tight. If not, tighten it. If the screw is missing, it may
be found at a home center. It is a metric screw, and
the size is M4x0.7x6
-3-
Operation Instructions (Continued):
Insert staples
(legs up)
Press latch
to open cover
Fig. 7
Approx.
Stock #
Leg Length
Leg Length
NS32
6mm
1/4"
NS33
10mm
3/8"
NS34
13mm
1/2"
NS35
16mm
5/8"
Fig. 6