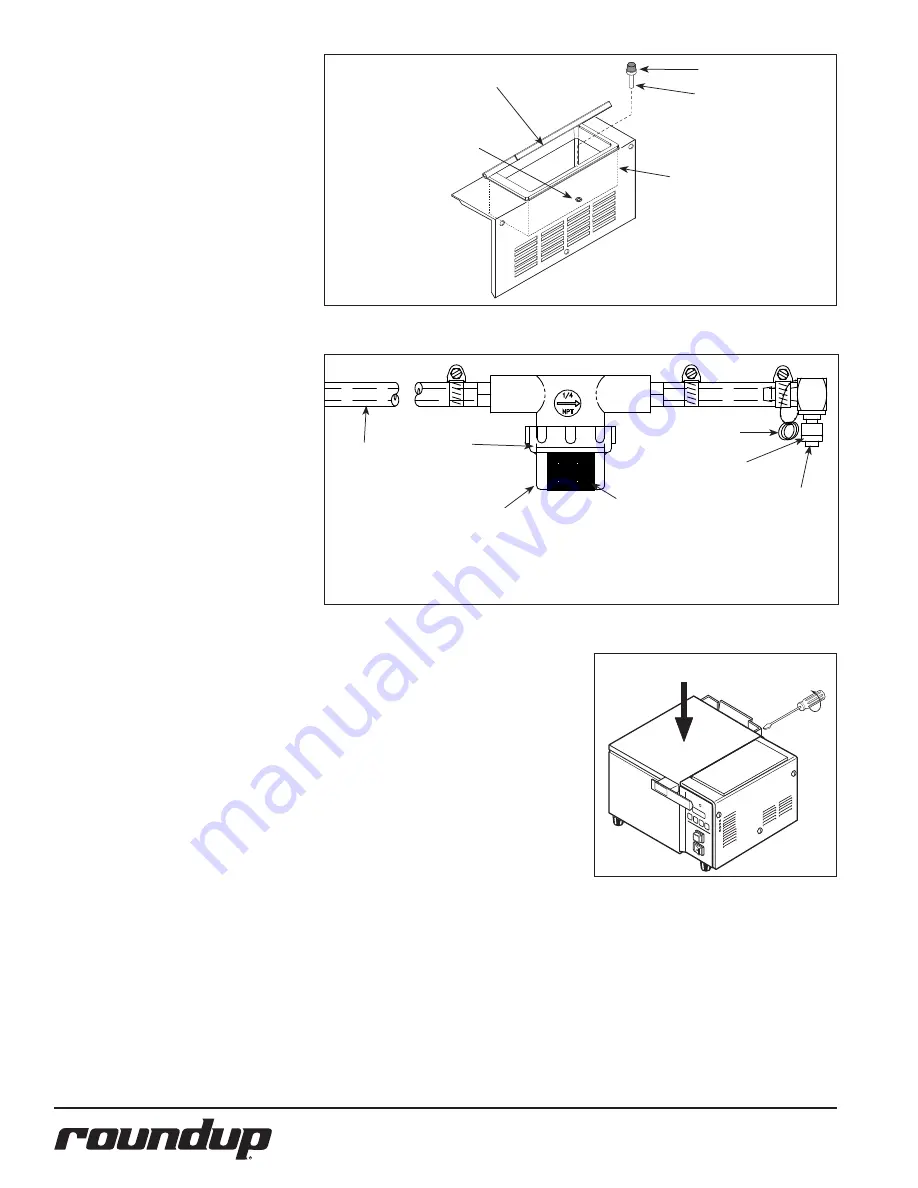
10
P/N 1010678 Rev. K 08/12
Male Quick
Disconnect
Insert
Strainer Cup
Tubing
Mesh
Screen
O-ring
Water Tank Filter
Filter Stem
Access Cover
with Tank
(dotted line)
Bottom Hole
of Water
Tank
Tank Cover
Spare O
Rings (3)
O Ring
NOTE: If the Male Quick Disconnect Fitting leaks water while it is engaged
into the rear of the Steamer, then the O-ring must be replaced. Three (3)
spare O-Rings are supplied.
MONTHLY MAINTENANCE
WATER TANK FILTER
(DFW/DFWT-100/150 ONLY)
The water tank filter is used to prevent par-
ticles or food products from entering and
damaging the water pump. Inspect and clean
this filter monthly or more regularly using the
following procedure.
1. Turn the power off, unplug the power
cord, and allow the unit to cool down
before proceeding.
2. Open the slide door (Figure 7).
3. Remove the water tank filter, located
inside the tank, by pulling it upwards
and out of the bottom hole.
4. Clean the filter by running it under tap
water. Replace the water tank filter if
the screen is torn or damaged.
5. Reinstall the filter stem into the bot-
tom hole of the tank (Figure 7).
6. Fill the water tank and test the unit.
TOP COVER ADJUSTMENT
It is normal for a small amount of steam to
escape around the front and sides of the top
cover. However, excessive steam may indicate
the top cover gasket is worn and/or the cover
is out of adjustment or damaged.
1. With the top cover closed, loosen the
four rear hinge bracket screws (Figure
9) one turn only.
2. Push down on the top cover heavily
(Figure 9). This ensures the gasket is
seated squarely around the Generator.
While maintaining the downward
pressure, re-tighten the screws.
WATER STRAINER
(DIRECT WATER HOOKUP MODELS)
The water strainer protects your equipment
from any foreign debris in the water line that
could damage the unit’s solenoid (causing the
unit to leak/flood) To ensure proper and con-
sistent steaming results, check the water pres-
sure regulator and strainer cup regularly. If the
pressure on the gauge has dropped, check the
strainer cup and clean out the accumulated
debris as follows:
1. Shut off the water supply valve to the
unit, unscrew the strainer cup, and care-
fully remove the mesh strainer Screen.
2. At the sink, gently flush all of the
accumulated debris from the strainer
cup and mesh strainer screen. Be
especially careful not to damage the
mesh strainer screen.
3. Carefully place the mesh strainer
screen into its seat at the bottom of
the strainer cup and confirm that the
orange O-ring is properly seated in its
place before screwing the strainer cup
and top back together.
4. Purge the air out of the strainer and
tubing by disconnecting the male
quick disconnect insert from the
equipment and, over a bucket, push
the white plastic tip in until there is
good water flow.
5. Replace damaged or worn parts.
6. Verify that the water pressure regula-
tor is set to 20–25 psi (1.4–1.7 kg/
cm2 or 138–172 kPa).
Figure 7. Water Tank Filter
Figure 8. Inlet Hose Assembly
Press Firmly On The Top
Cover
Figure 9. Top Cover Adjustment