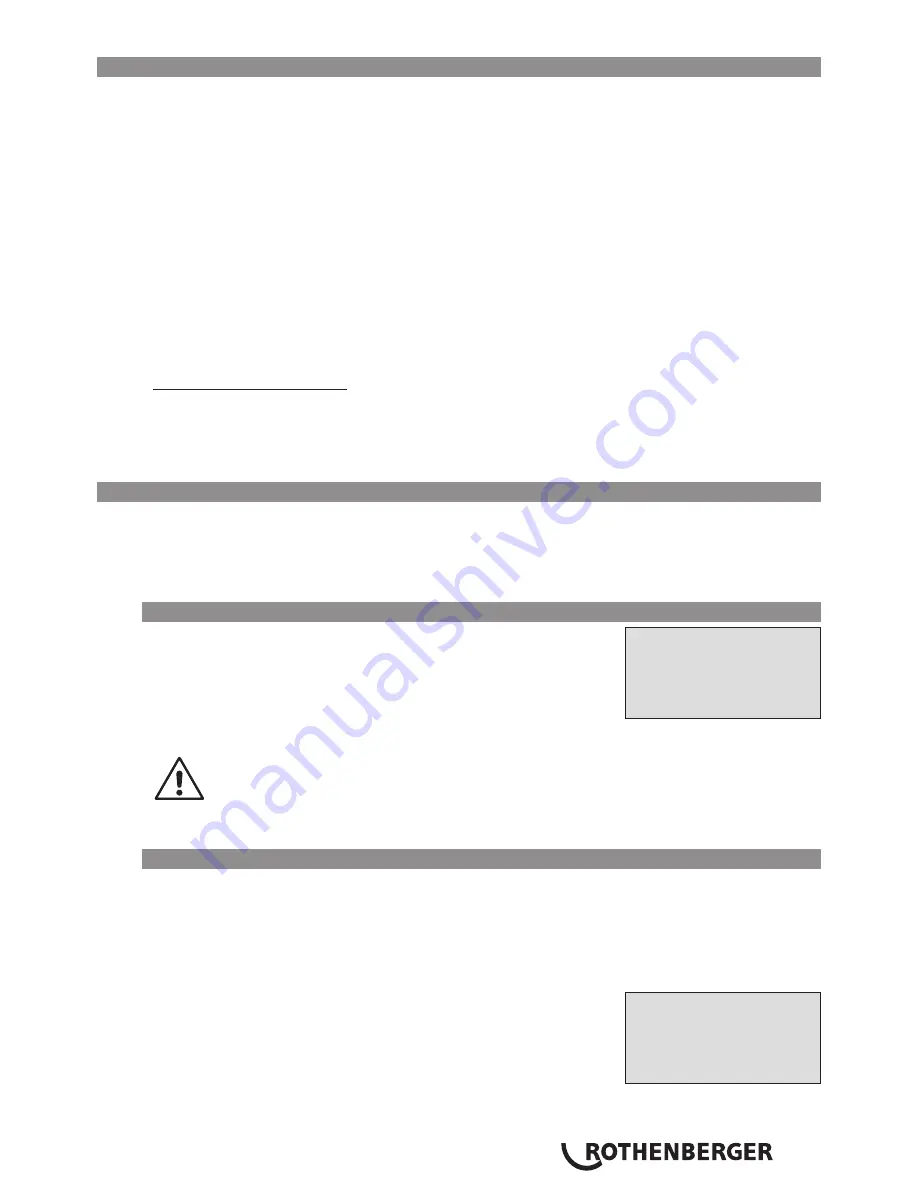
ENGLISH
19
4
Principles of Operation
The ROWELD ROFUSE Basic 48 V2.0 allows welding electrofusion fittings that feature a bar code.
Every fitting is provided with a tag with one or two bar codes on it. The structure of this code is
internationally standardized. The first code, encoding the data on proper welding, complies with
ISO 13950, the second code, if present, encodes component traceability data, some of which are
managed by the welding unit.
The welding parameters can also be entered manually. The microprocessor-controlled ROWELD
ROFUSE Basic 48 V2.0 Welding Unit
•
controls and monitors the welding process in a fully automated fashion,
•
determines welding duration depending on ambient temperature,
•
shows all information on the display in plain text.
All data that are relevant for the weld or for traceability are saved to the internal memory and can
be sent to a USB stick.
Welding data transfer is enabled through an interface of the USB A type, which is compatible
with a USB stick.
Further Optional Accessories
•
PC software
for downloading and archiving data on PC (for all common Windows operating
systems)
•
USB stick
for data transfer from the welding unit on the worksite to the printer or PC in your
office (see details at the end of this booklet)
5
Check-out and Operation
To operate the welding unit, be sure that it is set on a proper, level surface.
Be sure that power supply/generator protection is 16 A (slow blow).
Plug the power supply cord into the mains power supply or the generator.
Read and comply with the User’s Manual of the generator, if applicable.
5.1
Turning the Welding Unit On
After connecting the power supply cable to mains power or a
generator, turn the welding unit on using the On/Off switch. This
causes Display 1 to show
Display 1
Roweld
Welder
ROFUSE BASIC 48
Version 2.0
.
Then the screen changes to Display 2.
CAUTION in case of System Errors! If during the auto-test that the unit performs
at start-up, an error is detected, a “System Error” message shows on the display.
When this happens, the welding unit has to be disconnected immediately from
the power suppy and the fitting, and it has to be shipped to the manufacturer
for repair.
5.2
Entering the Welder ID Code
The welding unit can be configured to ask for the welder identification code before the fitting
code is entered. The display screen then shows the message “Enter Welder Code.” (Later this
screen can be accessed by a quick access routine; see Sect. 6.1.) The numeric code can be entered
either by reading it from a tag with the scanner or by using the
ï
,
ð
,
ñ
,
ò
keys. Whether the
welder identification code has to be entered and if so, when or how often, is determined in the
“Settings” sub-menu of the configuration menu (see Sect. 10.1).
When the welder code is read from a bar code using the scanner,
an
Display 2
Enter Fitting Code
14:32:11 21.10.12
Inp.Volt. 230V 50Hz
No Contact
audible signal confirms this and the screen shows the read code
and switches to the next input display. When the code is entered
manually, it is saved by pressing the START/SET key. If the code
entered is not correct, a “Input Error” message appears; check the
sequence of numbers and correct as needed.