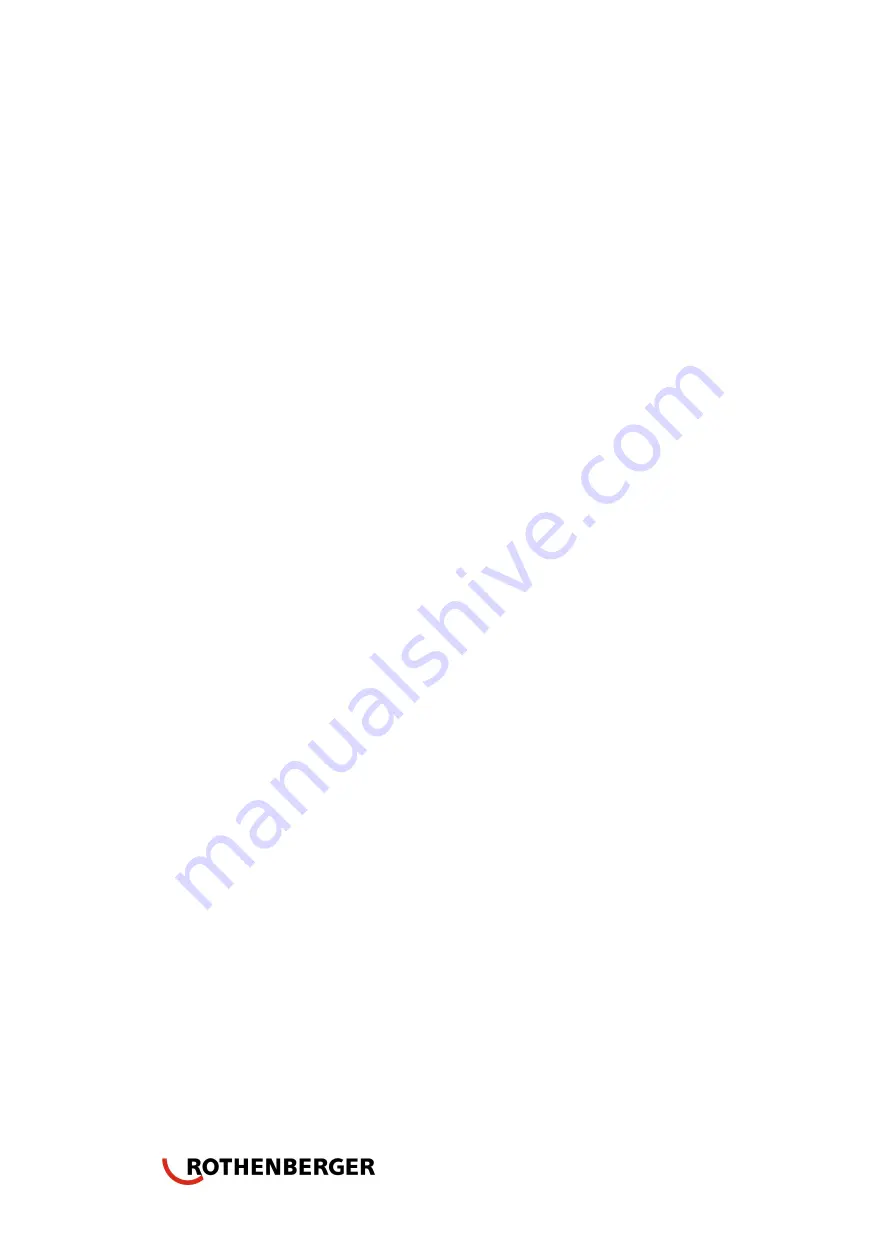
43
3.4 Welding Steps
3.4.1 Pipes
Before welding, firstly, check if the material and its pressure grade are the required ones.
Secondly check if there are scratches or fissures on the surface of pipes/fittings. If the depth
of scratches or fissures exceeds 10% of the wall thickness, cut the section of scratches or
fissures. Clean the pipe end’s surfaces with clean cloth to keep the pipe’s ends clean.
3.4.2 Clamping
Place the pipes/fittings in inserts of frame and keep the ends to be welded be the same length
(no effect on the planning and heating of the pipe). The pipe out of the basic frame should be
supported to the same central axial of clamps. Fasten the screws of clamps to fix the
pipes/fittings.
3.4.3Adjust the pressure
3.4.4 Planing
Open the pipes/fittings ends after turning swing check valve anti-clockwise to the end. Put the
planning tool between the pipes/fittings ends and switch it on, close the pipes/fittings ends by
acting on the direction valve meanwhile slowly turn swing check valve clockwise until there
are continuous shavings appearing on both sides. Turn the swing valve anti clockwise to relief
the pressure, in a moment later open the frame, switch off the planing tool and remove it.
Close the pipes/fitting ends and checks the alignment of them. The maximal misalignment
should not exceed 10% of the wall thickness, and it could be improved by loosening or
tightening the screws of clamps. The gap between two pipe ends should not exceed 10% of
wall thickness; otherwise the pipes/fittings should be planed again.
Caution: The shavings thickness should be within 0.2~0.5 mm and it can be adjusted by
adjusting the height of the planning tool blades.
3.4.5 Heating
Clear the dust or slit on the surface of heating plate (Caution: Don’t damage PTFE layer on
the surface of heating plate.), and make sure the temperature has reached the required one.
Put the heating plate between the pipe ends after it reaches required temperature. Close the
pipes/fittings ends by operating direction valve and raise the pressure to specified pressure by
swinging pressure regulation valve till the bead reaches specified height.
Summary of Contents for ROWELD E Series
Page 1: ...1 ...
Page 22: ...22 7 Electrical draw diagram and Hydraulic schematic diagram 7 1 Electrical draw diagram ...
Page 23: ...23 7 2 Hydraulic schematic diagram ...
Page 53: ...53 7 Electrical draw diagram and Hydraulic schematic diagram 7 1 Electrical draw diagram ...