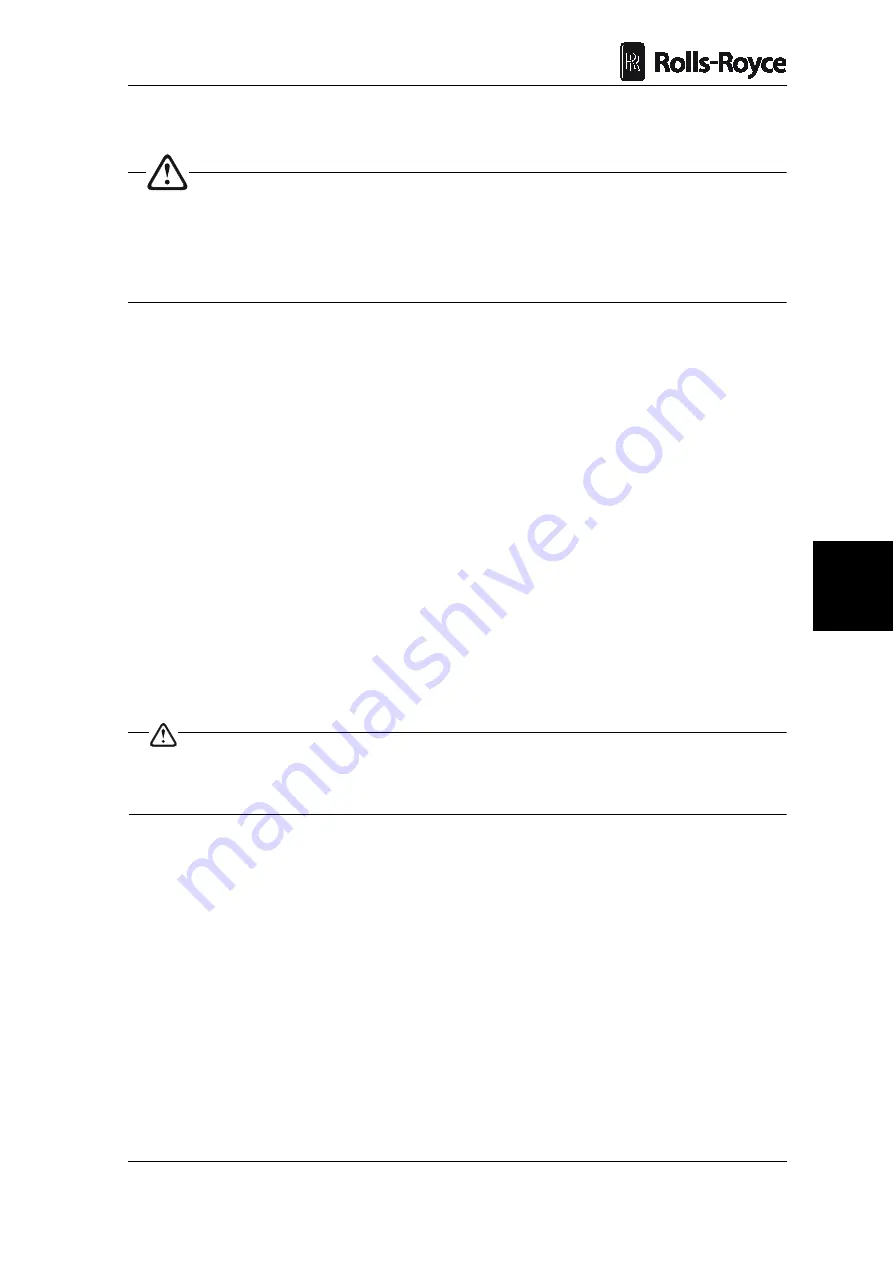
Maintenance Instructions
7
Page 3 of 22
Doc. No.: 13S000411
Revision: A
Copyright © 2010 Rolls-Royce plc
1 Safety and Precautions
Warning: Risk of personal injury.
Changes or modifications to the system not expressly approved by the
Rolls-Royce department responsible for compliance, could void the
warranty or the user's ability to operate the equipment.
The following warnings and cautions are for your safety, for the prevention of injury
from electric shock and for a safe operation of the equipment. Also see chapter
2 Safety
.
• While performing maintenance tasks, always position the equipment (and yourself) on
a stable and safe surface.
• Ensure that all accessible cables cannot be walked on, tripped over or damaged by
transportable items.
• If a device is damaged or fails to function correctly, disconnect it from the power
source. Refer to the system drawings to locate the nearest fuse/circuit breaker, see
chapter
12 Design Drawings
.
• Do not attempt to repair any sub-component yourself – consult a qualified Rolls-Royce
service technician.
• A serious electrical shock hazard exists within the covers of some components (i.e.
displays) and on marked locations inside the cabinets (marked with 220 VAC or
24 VDC).
2 Electrostatic Discharge (ESD)
Caution: It is very important that you are connected to ground before touching any
electronic components or printed circuit boards.
The life span of electronics can be affected by damage caused by electrostatic discharge.
This can happen if a charged tool or person touches a component. Therefore it is very
important that all tools and personnel are discharged by touching a grounded point
before the printed circuit board or any of the components are touched. It is equally
important to discharge the package with the new component before opening it. A person
walking on a carpet can be charged with up to fifteen thousand volt (15000 V). In worst
case, some sensitive components can be destroyed when discharged with about 100 V.
Summary of Contents for Helicon X3
Page 2: ......
Page 4: ...Copyright 2010 Rolls Royce plc Doc No 13S000411 Revision A...
Page 8: ...Introduction Page 6 of 6 Doc No 13S000411 Revision A Copyright 2010 Rolls Royce plc...
Page 10: ...Copyright 2010 Rolls Royce plc Doc No 13S000411 Revision A...
Page 16: ...Copyright 2010 Rolls Royce plc Doc No 13S000411 Revision A...
Page 30: ...System Description Page 16 of 16 Doc No 13S000411 Revision A Copyright 2010 Rolls Royce plc...
Page 32: ...Copyright 2010 Rolls Royce plc Doc No 13S000411 Revision A...
Page 34: ...Delivery Specification Page 4 of 4 Doc No 13S000411 Revision A Copyright 2010 Rolls Royce plc...
Page 50: ...Copyright 2010 Rolls Royce plc Doc No 13S000411 Revision A...
Page 54: ...Copyright 2010 Rolls Royce plc Doc No 13S000411 Revision A...
Page 76: ...Copyright 2010 Rolls Royce plc Doc No 13S000411 Revision A...
Page 98: ...Copyright 2010 Rolls Royce plc Doc No 13S000411 Revision A...
Page 112: ...Trouble Shooting Page 16 of 16 Doc No 13S000411 Revision A Copyright 2010 Rolls Royce plc...
Page 114: ...Copyright 2010 Rolls Royce plc Doc No 13S000411 Revision A...
Page 118: ...Contact Information Page 6 of 6 Doc No 13S000411 Revision A Copyright 2010 Rolls Royce plc...
Page 120: ...Copyright 2010 Rolls Royce plc Doc No 13S000411 Revision A...
Page 124: ...Spare Parts Page 6 of 6 Doc No 13S000411 Revision A Copyright 2010 Rolls Royce plc...
Page 126: ...Copyright 2010 Rolls Royce plc Doc No 13S000411 Revision A...
Page 128: ...Tools Page 4 of 4 Doc No 13S000411 Revision A Copyright 2010 Rolls Royce plc...
Page 130: ...Copyright 2010 Rolls Royce plc Doc No 13S000411 Revision A...
Page 132: ...Design Drawings Page 4 of 4 Doc No 13S000411 Revision A Copyright 2010 Rolls Royce plc...
Page 134: ...Copyright 2010 Rolls Royce plc Doc No 13S000411 Revision A...
Page 136: ...Revision Page 4 of 4 Doc No 13S000411 Revision A Copyright 2010 Rolls Royce plc...
Page 138: ...Copyright 2010 Rolls Royce plc Doc No 13S000411 Revision A...
Page 140: ...Subsuppliers Manuals Page 4 of 4 Doc No 13S000411 Revision A Copyright 2010 Rolls Royce plc...