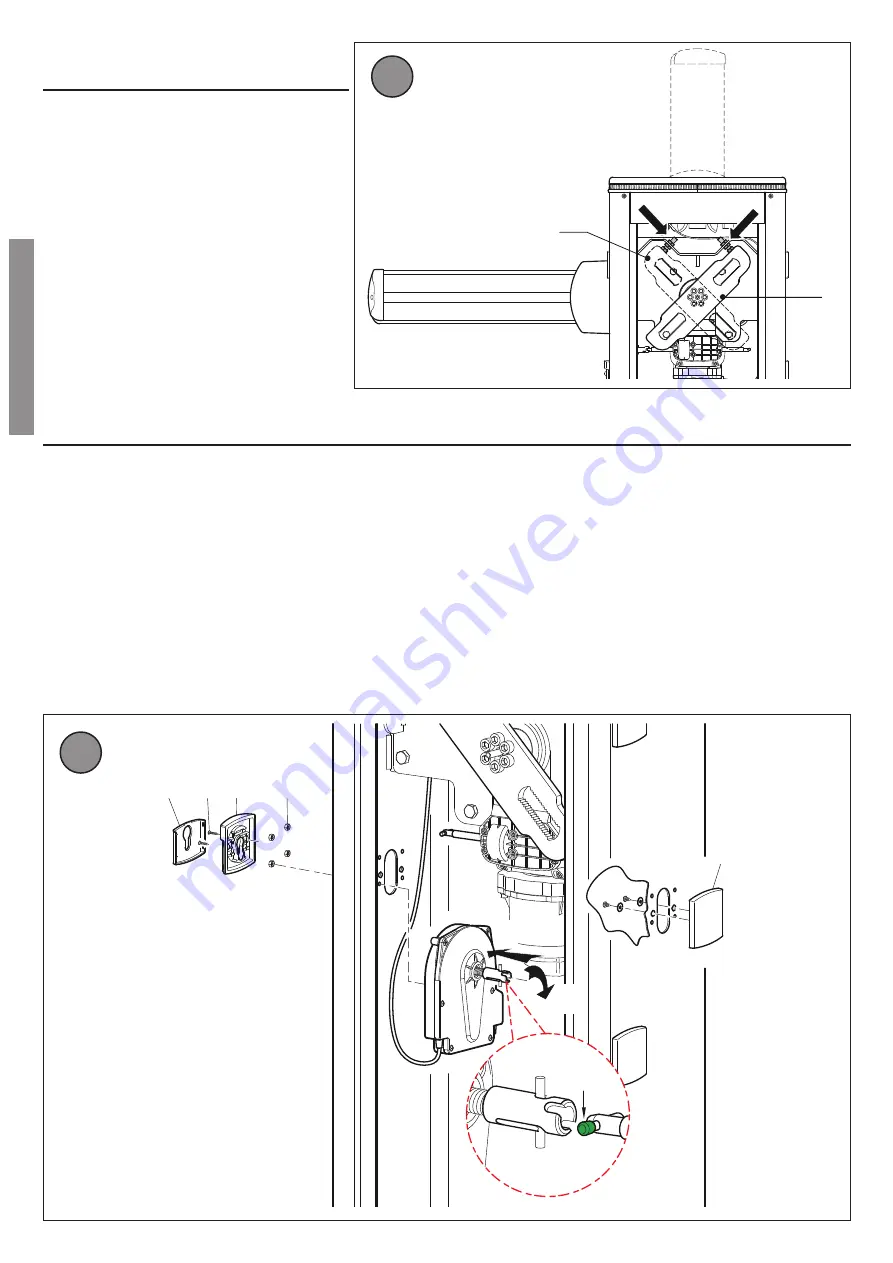
EN
14 ADJUSTING
THE
MECHANICAL STOP
Figure 21 shows the mechanical stop on a barrier installed on the
RIGHT hand side. For barriers installed on the LEFT, perform the
mirror images of the procedures illustrated.
• Unlock the barrier (see chapter 23).
• Set the completely open
AP
and completely closed
CH
positions by adjusting the relative mechanical stops.
• Lock the barrier (see chapter 23).
AP
CH
15 INSTALLING THE LOCK RELEASE SYSTEM
The lock release system is already installed in the factory on one of the two side of the barrier.
If it is necessary to install the system on the opposite side:
• Open the inspection hatch.
• Remove the screws fastening the plastic cover [A].
• Remove the escutcheon plate [B] of the lock release system, prising the lateral clips open to detach.
• Undo the two self-tapping screws [C] and remove the aluminium front panel [D].
• Undo the four M5 nuts [E].
• Push the steel connector [F] outwards to compress the spring and rotate by 45°.
• Detach the lock release system and install on the opposite side, taking care not to damage the safety cable.
NOTE
: two coloured caps (red and green) are fitted to check that the lock release system is installed correctly, regardless of which side it is fitted on.
When the barrier is locked, the green cap must face towards the inspection hatch (installer view). If not, the lock release system is installed incorrectly.
• Tighten the nuts [E].
• Fit the aluminium front panel [D] and fasten with the screws [C].
• Fasten the escutcheon plate [B] on the lock release system.
• Fit the plastic cover [A] on the opposite side.
A
F
E
D
C
B
VERDE
GREEN
G
21
22