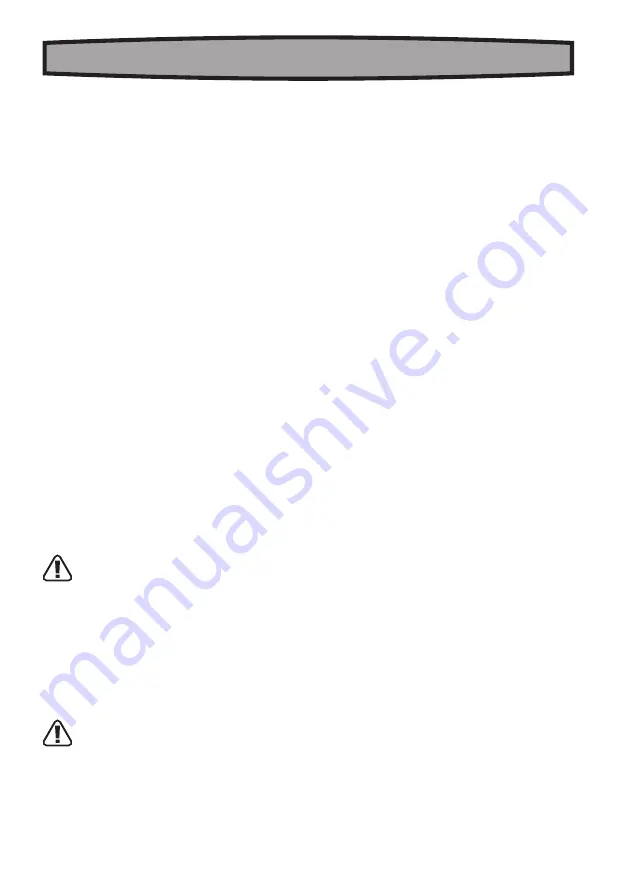
10
13MM DRILL PRESS
EN
contents against check list. Retain packaging until
all parts are accounted for and assembly has been
completed.
Lift out base plate and remove protective paper and
place on workbench.
Inside the small box you will find the chuck, three
handles, three set bolts, three washers, allen key and
chuck key. Place on workbench.
Lift worktable out and remove protective paper. Put on
workbench. Remove headstock and motor assembly
and put on workbench. Remove column and plastic
guard. Put plastic guard away for time being.
2. ASSEMBLY
Take base plate and select a suitable place on
workbench for mounting (See Fig. B). Be aware of
table legs and anything, which might reduce access to
underneath:
Locate the four mounting holes (with 12mm diameter).
Select suitable length bolts (at least 45mm length),
washers and nuts (not supplied). Using base as a
template drill four holes through the workbench. Bolt
the base plate to the bench. Do not overtighten as this
could crack the cast base.
Take the protective paper or plastic bag off the column.
Align with the three threaded holes on the base plate.
(See Fig. C) Secure with the three bolt sets supplied.
Again do not use excessive torque.
Slide the adjustable height work table over the column.
Secure midway with the clamping lever. (See Fig. D)
CAUTION: The head stock and motor assembly
is heavy and may require two person
handling.
Use the allen key to loosen the two screws.
Lower the headstock and motor assembly all the way
onto the column.
Position the headstock and motor assembly so the
front aligns with the centre of the base plate.
Use the allen key to tighten the two screws. Retain the
allen key for further adjustments. (See Fig. E)
CAUTION: Do not connect to power supply yet.
Loosen the securing screw (a) of the safety
guard, insert the guard into the spindle and tighten the
screw (See Fig. F). Open the safety guard, and insert
the chuck into the spindle. The chuck is mounted
firmly when you can not pull it out with your hand (See
Fig. G).
Attach the three handles into the feed shaft. (See Fig. H)
Raise the table and place a piece of scrap wood on it.
Locate the depth stop into the hole and hold it using
one hand, then rotate clockwise to lock it using another
hand. Keep the red depth mark with the 0mm level. (See
Fig. I1, I2).
Rotate the handles to keep the red depth mark with any
depth you want, then rotate the lower screw (a) onto the
hole to fix the depth. (See Fig. I3, I4)
NOTE:
It has a tapered shaft and the chuck locates onto
this. Bring the chuck into contact with the wood on the
work table and gently apply pressure to lock the chuck
onto the spindle.
OPERATING INSTRUCTIONS
1. OPERATING THE PILLAR DRILL
NOTE: Remove the plug from the socket before
carrying out any adjustment, servicing or maintenance.
1) SELECTING THE CORRECT SPEED FOR DIFFERENT WORK
Refer to speed selection label inside of motor housing
and select the speed required for the job in hand. The
tool has five speed settings: 500-2500/min. Choose
the setting nearest to the speed selection label
recommendation.
2) WORK TABLE ADJUSTMENT
The table can rotate Bevel ± 45 degrees. Loosen the
table securing bolt and rotate to desired angle. Re-
tighten lock nut. (See Fig. J)
Loosen the locking lever to the rear of the table. (See
Fig. K)
Move the column up or down to desired height. When
desired height is reached lock into position.
3) DEPTH STOP ADJUSTMENT
Bring the drill bit in contact with the work piece to be
drilled. Take a measurement from the scale on front of
tool (See Fig. L). Move work piece and add the amount
on to the previous measurement. Move lock nuts down
to that required position and lock. This will give a
consistent depth when drilling.
4) STARTING AND STOPPING THE PILLAR DRILL
The tool is fitted with a no volt switch assembly (See
Fig. M). This means in the event of a power failure
when drilling, the motor will not start once the power is
restored until the switch is reactivated.
NOTE:
The cover is fitted with a safety interlock switch
(See Fig. N). If the cover is not correctly located and