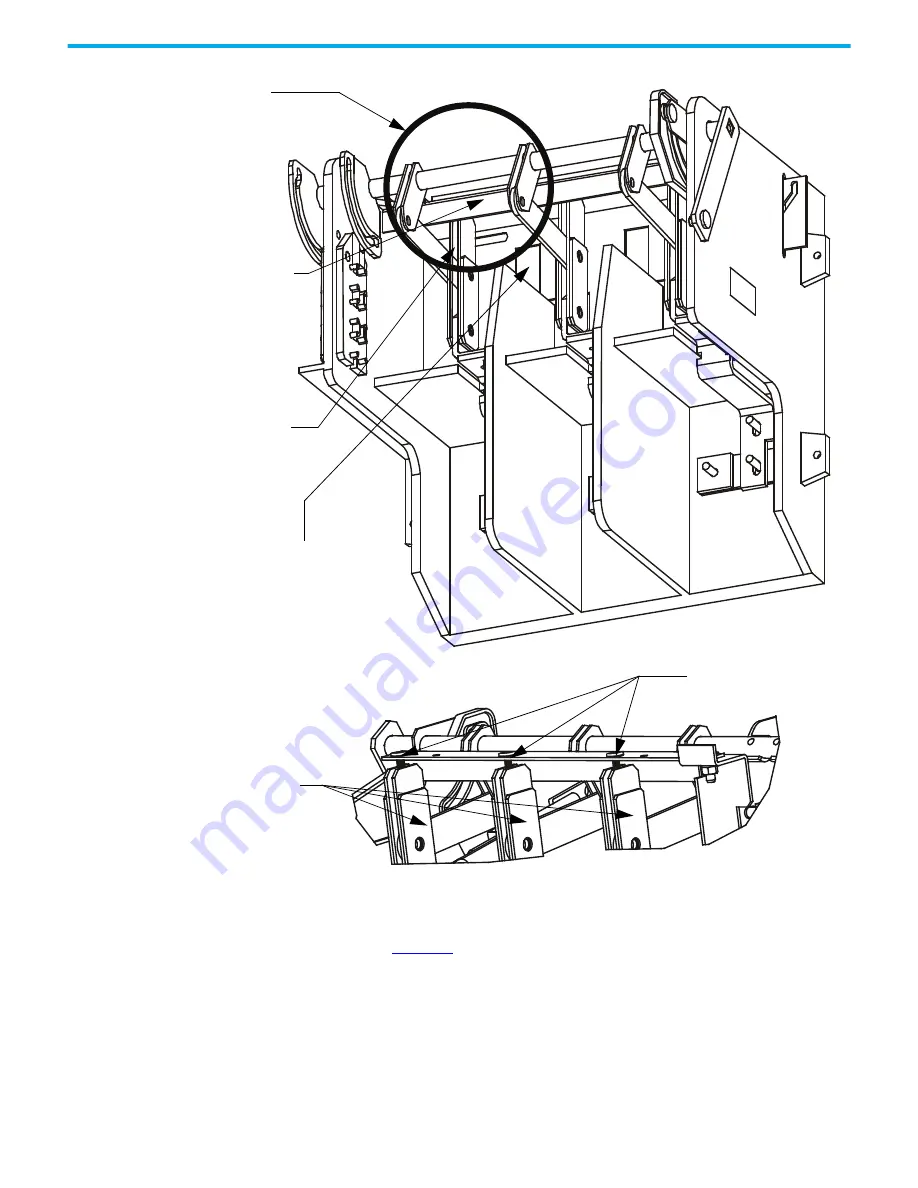
Rockwell Automation Publication 1512A-UM101B-EN-P - December 2021
51
Chapter 5 Maintenance
Figure 38 - Inspecting Isolation Switch in Open Position
6. Check the line and load sides of the contactor with a hot stick or
appropriate voltage measuring device to verify that they are voltage free
(see
).
a. Check for line-side voltage at the top vacuum bottle terminals.
b. Check for load-side voltage at the bottom vacuum bottle terminals.
See Detail A
Grounding Bar
Isolation Switch Blades
must fully engage
Grounding Pins of
Grounding bar
(Verify for each phase)
Isolation Switch Shutters
must be closed
(Verify for each phase)
Detail A
Grounding Pins
Isolation Switch
Blades in open
position
Viewed from back with components
removed for clarification