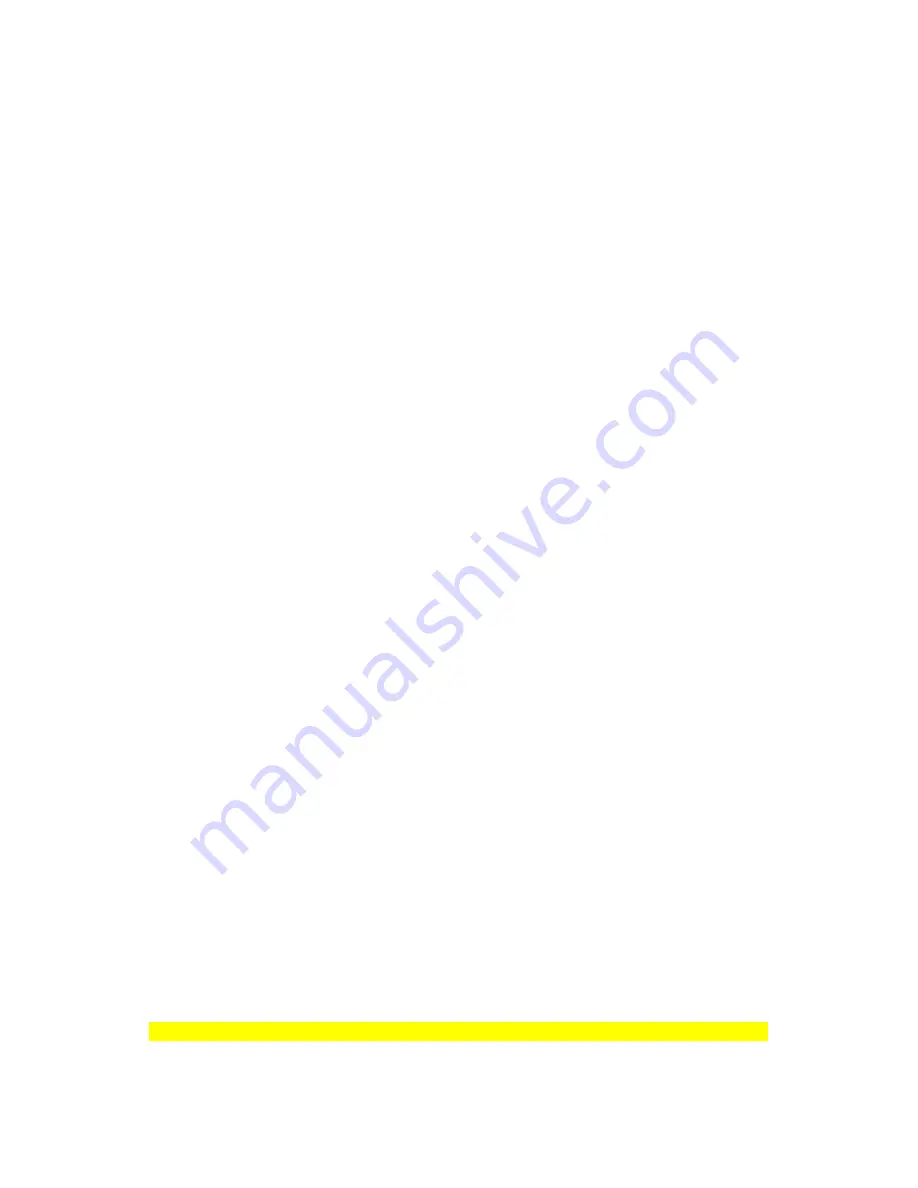
16
TAILSTOCK DOES NOT SLIDE NICELY ONTO TILT‐AWAY
: See the Tilt‐Away page for instructions on realignment. Start with
the “Minor Misalignment” section.
BANJO, TAILSTOCK OR HEADSTOCK WILL NOT SLIDE EASILY:
Clean the bottoms and apply a light coating of wax. Also
clean the cam shafts and cam sleeves and very lightly oil. Also make sure the clamp levers are vertical before you try to
move the component.
VIBRATION:
All lathes will vibrate if you have out of balance work and run the speed to fast. For systemic vibration
problems, start with the feet. All four feet should be carrying about the same weight. This is more important than having
your lathe level. Settle the lathe as described elsewhere. Also use the hard rubber pads supplied with your lathe.
Another source of vibration is loose mounting of your work. Chucks and faceplates must seat on the spindle shoulder.
Use a thin nylon washer between the spindle shoulder and the chuck or faceplate. If your chucks or faceplate won’t seat,
see the next section on spindle maintenance.
SPINDLE THREAD MAINTANCE
: Your faceplates and chucks should spin on and off freely. To do so, the threads on your
spindle, chucks and faceplates must be clean and burr‐free. Every time you put something on the spindle you should
clean the spindle threads and the accessory being mounted with compressed air and visually inspect both items for
debris. Put a drop of mineral oil (won’t stain wood) on the spindle every now and then.
MORSE TAPER MAINTENANCE
: Morse tapers need to be clean and burr‐free to work properly. If they are not, the
inserted component can spin which may damage both the internal and external tapers. The “TaperMate” Morse Taper
Cleaner” available at many woodturning supply houses is a good at getting soft debris out of internal tapers. If your
spindle or tailstock tapers have burrs or galls get a Morse taper hand reamer of the appropriate size. Do not attempt to
fully restore a shiny internal surface with the reamer, just get the high spots off. Use cutting oil liberally. For the external
surfaces, light passes with a smooth‐cut file or a little sandpaper is usually all you need. Concentrate on the burrs, and
leave good surfaces alone.
FINISH
: The lathes are powder coated and the parts are either semi‐gloss black or Silvervein. Powder coating is quite
durable, but not indestructible. Certain solvents can negatively affect the finish. We have been told that Camphor, a
wood common in the southeast, can also negatively affect the powder coat finishes. Silvervein is hard to touch up, so if
you want to keep the lathe nice, cover surfaces when using glues and finishes.
TAILSTOCK QUILL
: The tailstock quill should turn in and out easily. If your quill is not going in and out easily, remove the
quill and clean and lubricate the mechanism. Spray grease is handy for the threads and inside of the quill hole.
Sometimes burrs will form along the groove that the spindle lock rides in. It doesn’t take much of a burr to cause the quill
to bind. Take a small file and remove the burr. Filing a small chamfer on the edge of the groove is also a good idea.
LATHE MAINTENANCE TOOL KIT
: Here
are a few things to have in your tool kit to keep your lathe in good order:
Paraffin or paste wax for lathe bed and underside of banjo, tailstock and sliding headstock
Sharp three corner file with one side ground safe for deburring spindle threads
Bottoming tap the same size as your spindle for cleaning chuck and face plate internal threads
Spray grease for quill
Scotch Brite for cleaning lathe bed and underside of banjo, tailstock and sliding headstock
Small stiff brush for cleaning belt and pulleys
Mineral oil for lubricating spindle threads
Light lube oil, like WD‐40 or 3‐in‐1
TaperMate Morse Taper Cleaner or similar
Morse taper reamer
Single cut file (aka: mill file or bastard file). A sharp one.
General hand tools needed to maintain your lathe (wrenches, screwdrivers, Allen wrenches).
! Please see our website information section for a more complete discussion of lathe maintenance !