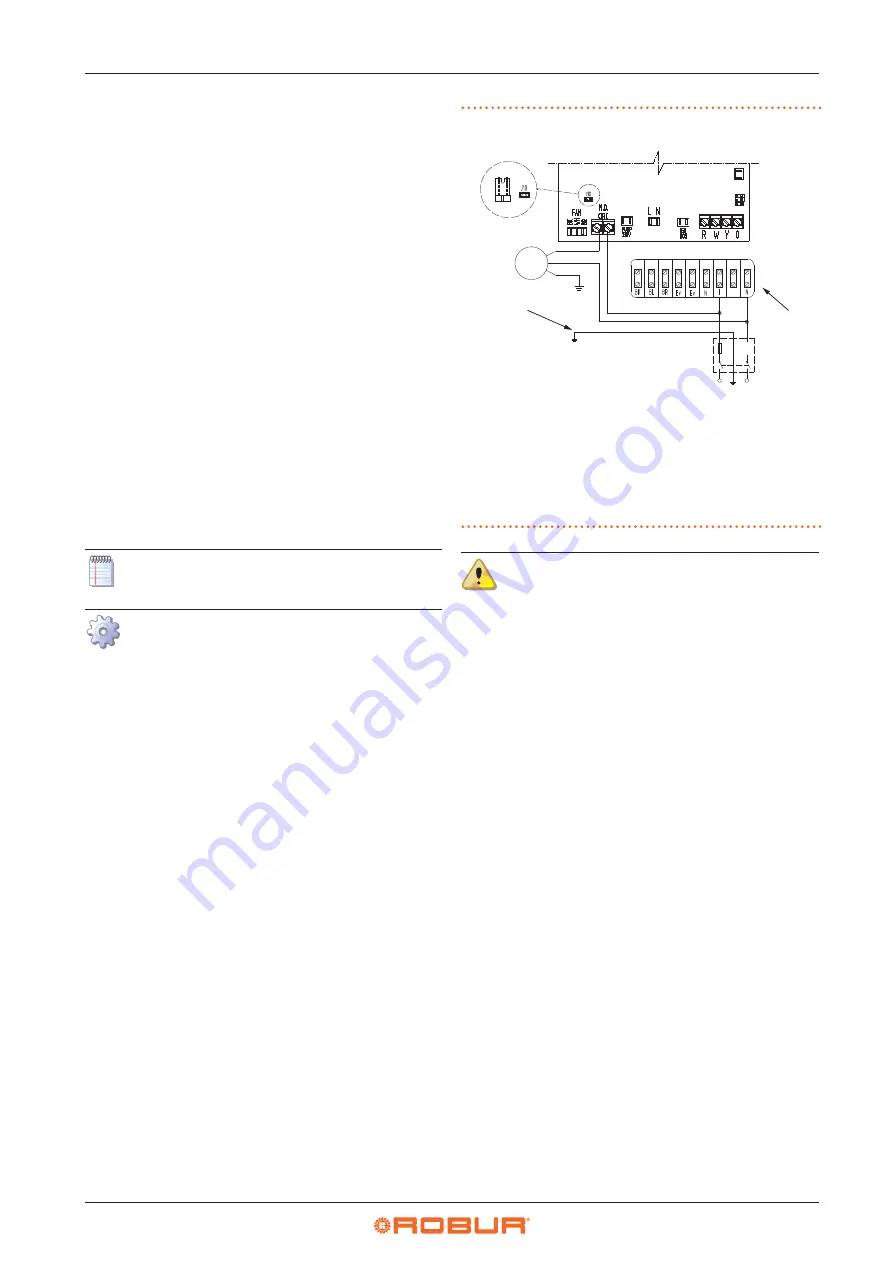
Electrical installer
26
4
2.
Remove the front panel of the appliance and the cover of the
electrical panel.
3.
Run the cables through the suitable holes in the connection
plate.
4.
Run the cables through the suitable cable glands in the elec-
trical panel.
5.
Identify the appropriate connection terminals.
6.
Make the connections.
7.
Close the electrical panel and fit the front panel back on.
4.3
ELECTRICAL POWER SUPPLY
Power supply line
The appliance electrical system is wired for single-phase, 208-
230 V and 60 Hz operation. The electrical control box includes
a 208-230 - 24 V transformer to supply low voltage to the con-
trol system. The high voltage line connections to be made at the
time of installation consists of connecting 208-230 V, 60 Hz to
the high voltage terminal board of the control panel. A fused dis-
connect switch should be installed in the 208-230 V supply line
within sight of and not over 50 feet from the unit.
Provide (by the installer) a protected single phase line (208-230
V 1-N 60 Hz) with:
▶
1 three-pole cable type FG7(O)R 3Gx1.5
▶
1 two-pole switch with two 5 A type T fuses, (GS) or one 10 A
magnetothermic breaker.
The switches must also provide disconnector capability,
with min contact opening 4 mm.
How to connect the power supply
To connect the three-pole power supply cable (Figure
1.
Access the electrical board of the appliance according to
the Procedure 4.2
2.
Connect the three lead-in wires to the terminal block
(TER) in the electrical panel on the machine.
3.
Provide the earth ground lead-in wire longer than live
ones (last to be torn in the event of accidental pulling).
Figure 4.1
Wiring for a single unit with pump absorbed current less
than 4 A
1
General switch
2
Use a 15 A time lag fuse on L wire
3
Ground pin
4
Ground cable has to be connected by a suitable eyelet to the ground
pin into the electrical panel, and fixed to it by the proper preset nut.
5
L, N wiring to the terminal board must be done respecting the correct
polarity
6
Jumper closed
1
2
3
4
5
6
PUMP
TER
L
F
N
GS
SCH
Do not operate the appliance
unless the water system
is filled with water and antifreeze.
4.4
SET-UP AND CONTROL
Control systems, options (1) or (2)
Two separate control systems are provided, each with spe-
cific features, components and diagrams (Figures 4.3
4.6
▶
System (1), with
DDC control
(with CAN bus connection).
▶
System (2), with an
external request
.
CAN bus communication network
The CAN bus communication network, implemented with the
cable of the same name, makes it possible to connect and re-
motely control one or more Robur appliances with the DDC con-
trol device.
It entails a certain number of serial nodes, distinguished in:
▶
Intermediate nodes, in variable number.
▶
Terminal nodes, always and only two (beginning and end).
Each component of the Robur system, appliance (GAHP, GA, AY,
...) or control device (DDC, RB100, RB200, ...), corresponds to a
node, connected to two more elements (if it is an intermedi-
ate node) or to just one other element (if it is a terminal node)
through two/one CAN bus cable section/s, forming an open lin-
ear communication network (never star or loop-shaped).
CAN bus signal cable
The DDC controller is connected to the appliance through the
CAN bus signal cable, shielded, compliant to Table 4.1
(admissible types and maximum distances).
For lengths ≤650 ft and max 4 nodes (e.g. 1 DDC + 3 GAHP), a
simple 3 x 18 AWG shielded cable may even be used.
Summary of Contents for GAHP-AR
Page 43: ......