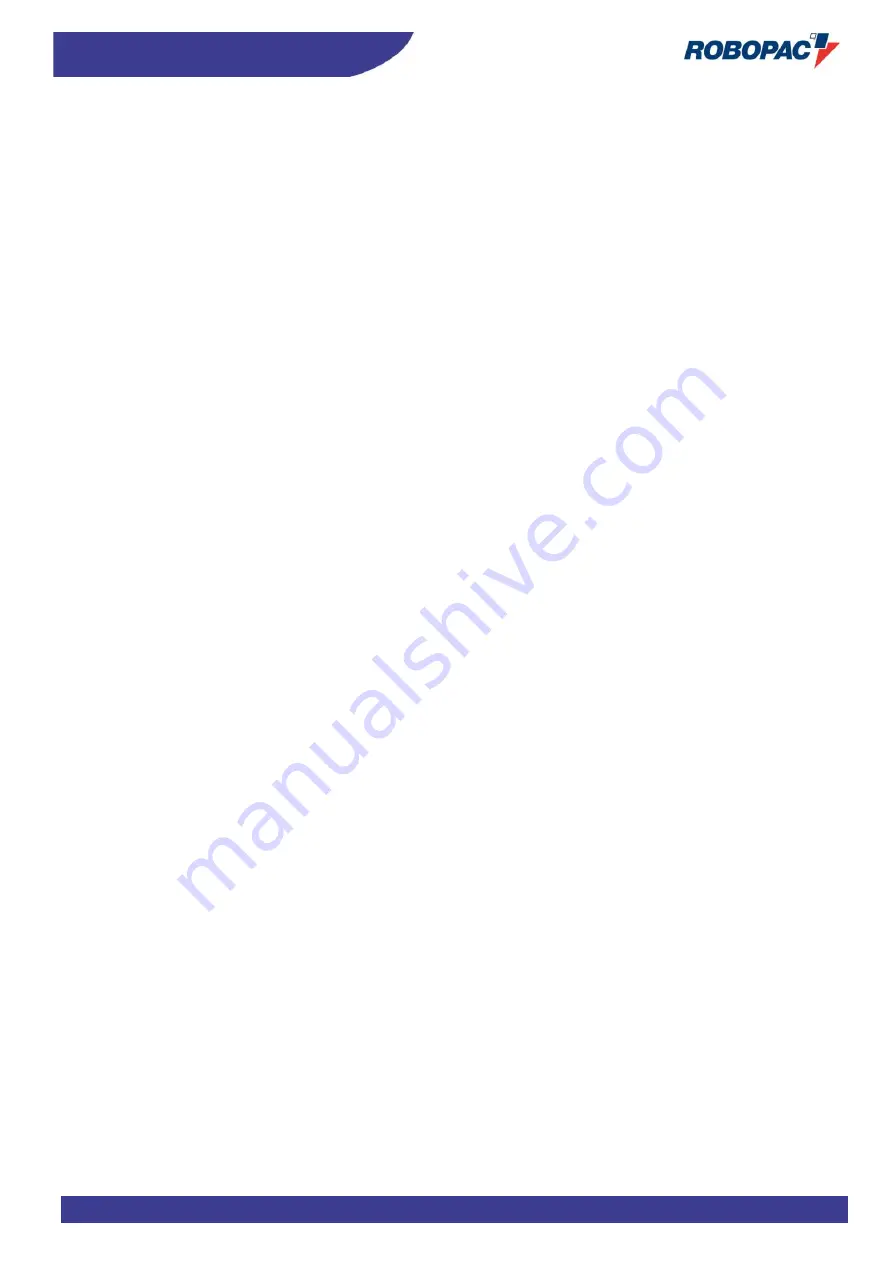
4
INDEX
ENG
"P3GS” REEL CARRIAGES FOR CHANGING PRE
-STRETCH RATIOS ................................................. 47
“HOME MULTILEVEL CONTROL” PAGE
“PRODUCTION COUNTERS (PALLETS)” PAGE
............................................................................................. 70
“ENTER PASSWORD” SCREEN (USER LOGIN)”
....................................................................................... 73
BLE TO "P3GS" AND "PVS” CARRIAGES ONLY)
.................................. 78
Summary of Contents for ROBOT S7
Page 2: ...2 INDEX ENG Page left blank intentionally ...
Page 21: ...ENG SAFETY INFORMATION 21 ...
Page 26: ...26 TECHNICAL INFORMATION ENG ...
Page 32: ...32 TECHNICAL INFORMATION ENG ...
Page 54: ...54 INFORMATION ABOUT THE USE ENG ...
Page 55: ...ENG INFORMATION ABOUT THE USE 55 ...
Page 91: ...ENG ANNEXES 91 ...