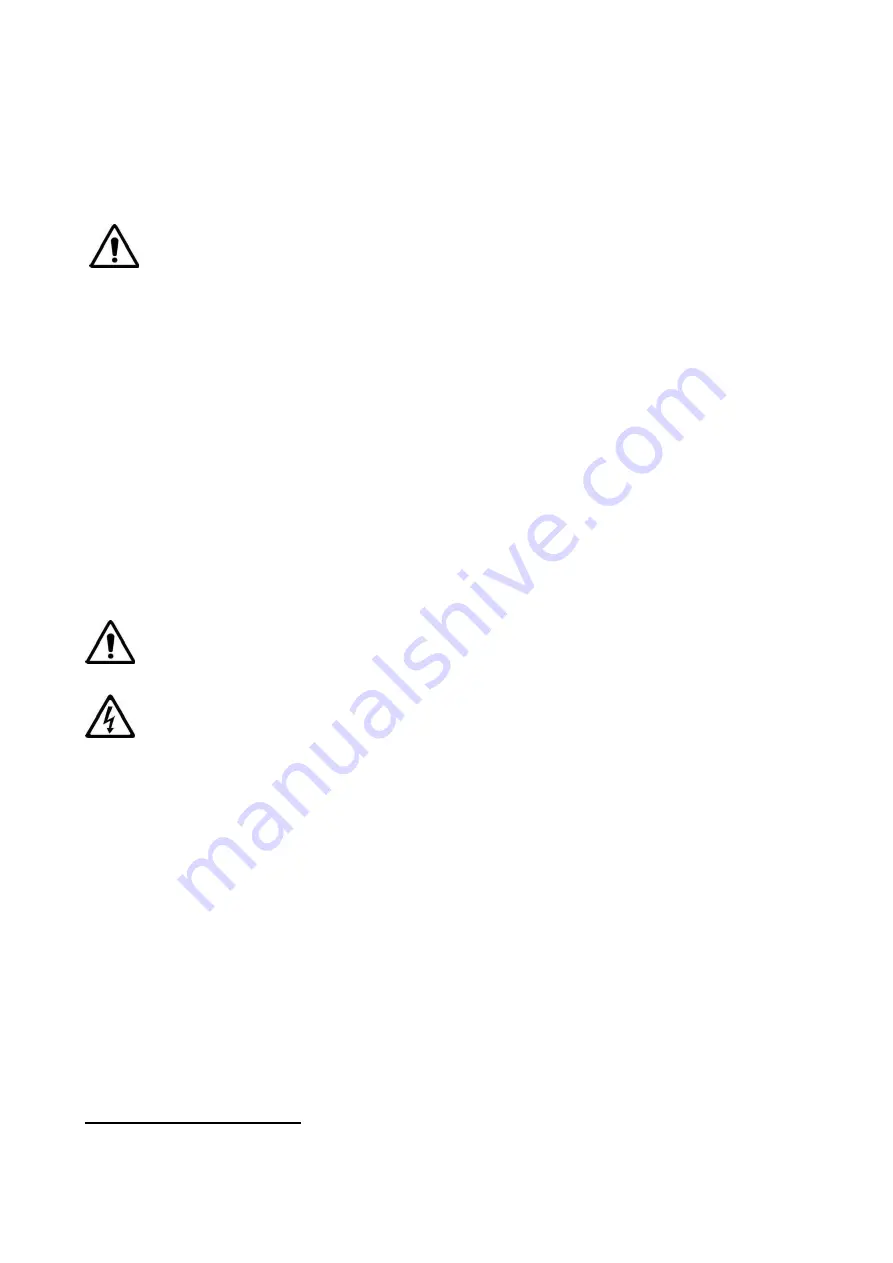
tm2627 Jan-20
16
3. Technical maintenance
3.1. General instructions
ATTENTION! THIS PART OF OPERATION MANUAL IS INTENDED ONLY FOR TRAINED PERSONNEL
EXPERIENCED WITH ELECTRICAL EQUIPMENT.
The purpose of technical maintenance is extend the working life of the machine
while fulfilling all safety requirements.
The following schedule
3
is recommended:
PROCEDURE
PERIOD
Cleaning machine and pan surfaces removing sugar and cotton candy
Once a day
Sidewall and heater cleaning
Twice a month
Brush unit maintenance
Every 6 months
3.2. Safety measures
DO NOT CLEAN THE SPINNING HEAD OR COMPONENTS WITH SHARP OR METAL PARTS. HOT
WATER, A SPONGE OR SOFT BRISTLE BRUSH IS ALL THAT IS REQUIRED OR PERMITTED!
DISCONNECT THE POWER SUPPLY BEFORE CLEANING OR PERFORMING TECHNICAL
MAINTENANCE!
3.3. Cleaning instructions
Spinning head cleaning
During long-term operation, the heating element and sidewall slits can become
clogged with sugar and carbon deposits. This may significantly reduce both
productivity and the quality of the cotton candy produced.
To clean the sidewall and heating element it is necessary to disassemble the
spinning head, remove the heating element and sidewall and wash them
carefully with hot water.
3
Technical maintenance may be required sooner if individual parts become fouled prior to
scheduled service.