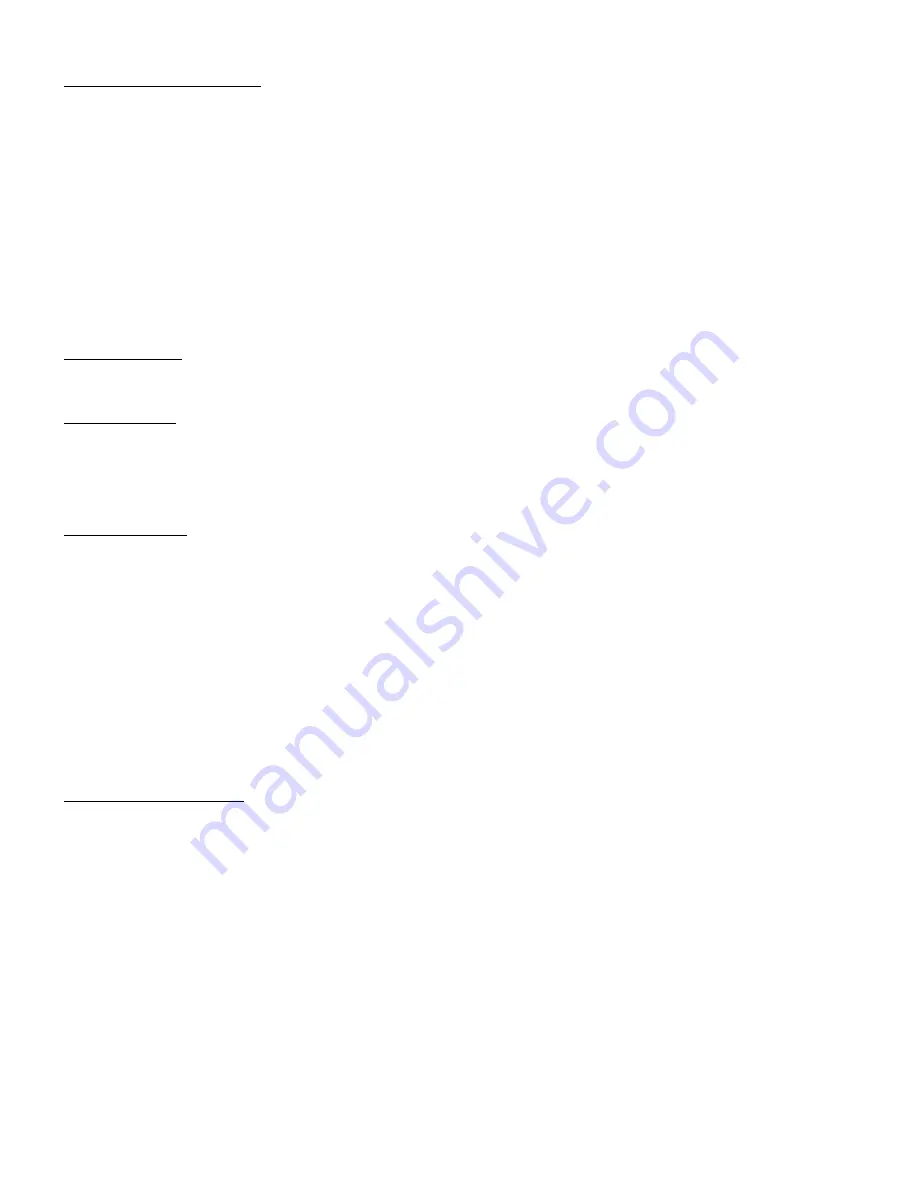
ISSUE 2016 Rev 1 - Installation Manual
3
RM Cylinders
Commissioning - filling the system
Check all connections for water tightness including factory made connections such as the temperature and pressure relief valve, as these may
have been loosened during transit.
The hot tap furthest away from the cylinder should be opened before filling the system to purge air and flush any disturbed particles
The system should be flushed before use. The remaining taps should be opened in turn to purge air from the system before turning on the
electrical supply.
For Direct Units
: The system must be fully filled and flushed before switching on the power to the immersion heaters and allowing the unit
to heat up. The immersion heater is supplied pre-set at 60°C. Turning fully to + sets to approximately 65°C.
For Indirect Units
: Ensure the lever on the two port valve is set to the filling position and use the boiler manufacturer’s commissioning
instructions to fill the primary circuit. When full, release the lever. Switch the programmer to Domestic Hot Water (DHW) and allow the unit
to start to heat. It is usual to set the thermostat to 60°C.
Storage Temperature
A storage temperature of 60°C is normal for both direct and indirect units. In hard water areas, consider reducing this to 55-60°C.
Safety Valve Check
If water is being released from either the expansion relief or the temperature and pressure relief valve during heat up, then this is indicative of
a problem that needs rectifying. Both valves should be opened slowly one at a time, and then together, allowing as much water to flow
through the tundish. Check that the discharge pipework is free from debris and the discharge can flow freely, without spillage over the
tundish. Check that the valves reseat correctly when released.
Draining the Cylinder
Isolate from the electric supply to prevent the immersion heaters burning out. Isolate the unit from the cold mains. Attach a hose to the
draining tap ensuring it reaches to a level below the unit, as this will ensure an efficient siphon is set up and the maximum amount of water is
drained from the unit. Open the hot tap closest to the unit and open the draining tap.
Note:
Water drained off may be hot.
SERVICE AND MAINTENANCE
Servicing must be carried out annually and should only be carried out by competent installers. Any spare parts used must be purchased from
RM Cylinders. Never bypass any safety devices or operate the unit without these being fully operational
Your guarantee may be void without proof of annual servicing via the Service record within this manual. The installer upon installation of the
unit must also complete the accompanying commissioning certificate.
Annual Servicing Requirements
A competent installer should carry out the following checks on an annual basis, ideally at the same time as the annual boiler service.
1.
The expansion relief valve on the inlet control set should be eased open allowing water to flow for a minimum of 5 seconds. The
valve should then be closed making sure it resets correctly. Repeat this procedure with the pressure/temperature relief valve. Insure
that the discharge pipework is allowing the water to flow freely, and clear any blockages if this is not the case.
2.
Ensure that all immersion heaters fitted are working correctly and are controlling the water temperature between 55°C and 60°C.
3.
This cylinder has no external expansion vessel. Expansion of heated water is accommodated by an entrapment of air in the upper
section of the cylinder separated by a composite disc interface which rises and falls as the stored water heats and cools. At an annual
service, it is necessary to ensure the level of the disc is correct by the following steps.
a)
Isolate the cold mains supply to the cylinder.
b)
Turn on a hot tap outlet
c)
Open the Temperature and Pressure Relief Valve until water stops flowing from both the Relief Valve and the hot tap.
d)
Close both the Relief Valve and the hot tap.
e)
Turn the incoming cold mains on and allow the cylinder to fill
f)
Re-open the hot tap until water flows and then close
g)
The correct level for the interface disc will then have been re-established.
4.
Remove the head on the inlet control set by unscrewing it, and clean the mesh filter within
5.
The benchmark service record supplied within this manual should be updated at each service.
9