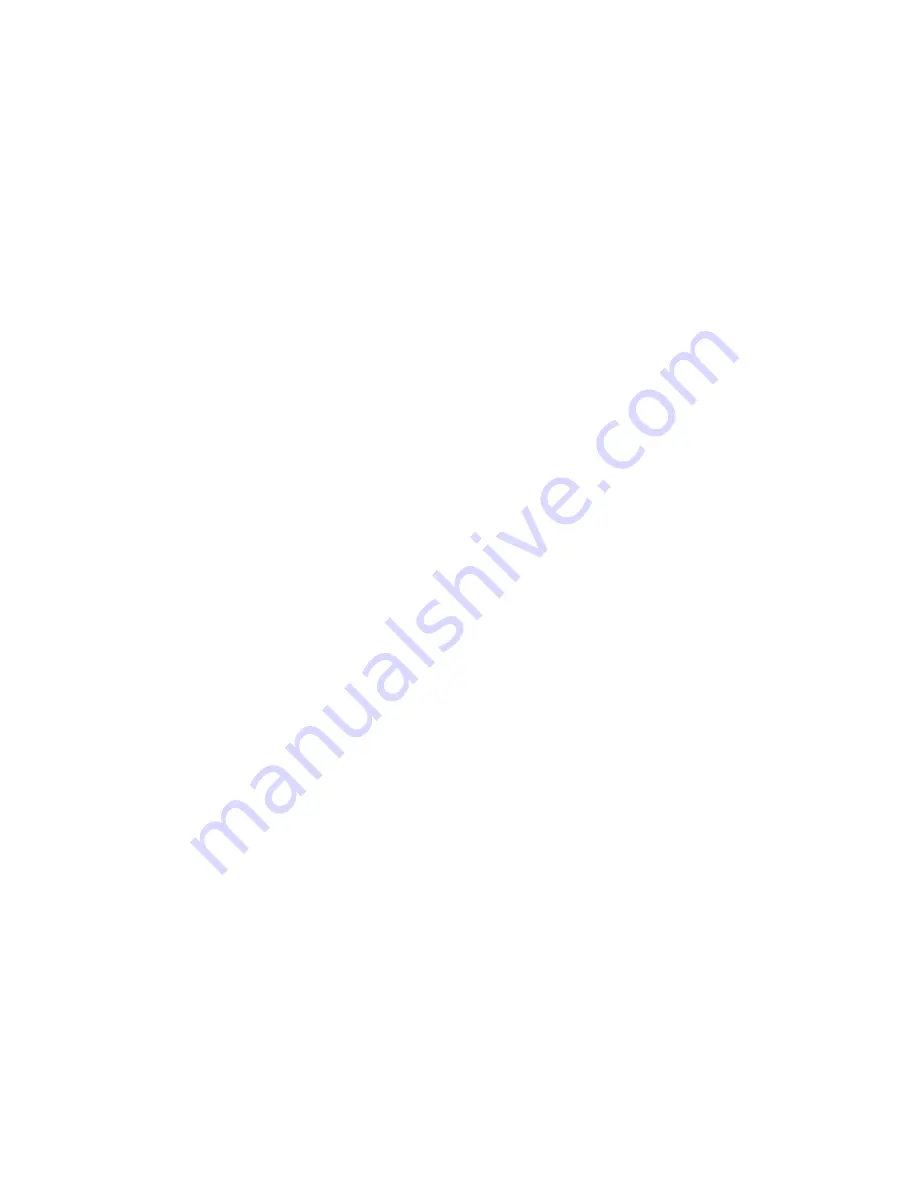
G. SYSTEM EVACUATION (SPLIT SYSTEM ONLY)
1.
With refrigerant piping completed and leak tested, equipment is ready to evacuate. Do not use compressor to evacuate system. A
quality vacuum pump capable of 350 micron vacuum is necessary for adequate and dependable system vacuum. Moisture in a
refrigeration system can cause corrosion, expansion valve freeze-up and oil sludge.
2.
attach vacuum pump to both high and low side of system through compressor service valves and evacuate to 350 microns (all
service valves, hand valves, and solenoids must be open during evacuation). It is suggested that vacuum pump be run for a period
of time after vacuum has been reached.
3.
Service should be provided by a qualified EPA refrigeration technician only.
H. START-UP
1.
This will involve checking and adjusting of all safety and operation controls (pressure and temperature controls have been set at
the factory; however, it is still desirable to confirm that settings are correct and controls function properly). Do not attempt to
disengaged or bypass safety controls without some means of stopping compressor in event of extreme high or low pressure
conditions that could damage the equipment. If controls fail to function at set point, determine cause and correct. Jumping any
safety control other than for testing purposes is dangerous to personnel and equipment, and nullifies equipment warranty.
2.
The bottom opening is the pump outlet to your process. The bottom opening is the pump outlet to your process. The middle
opening is the return inlet water coming back to the reservoir tank. Fit a union and a tee in the return line. Bring the make-up
water line to the tee. This is used to fill the chiller and system.
3.
With the chiller switch OFF, turn on the MAINPOWER to the chiller. Even though the chiller switch is off, the main power will
activate the compressor crankcase heater to warm up the oil and burn off any Freon that has migrated into the crankcase (this
feature is standard in ALL compressors with the exception of scrolls). Allow the compressor(s) to warm overnight, or at least six
hours. This is a one time procedure for start-up. However, if the main power is off for over 24 hours, (four hours if outside in
cold weather), then the warm-up procedure should be repeated.
4.
To fill chiller, open the city water and fill at a SLOW RATE. When water comes out of the ½” top vent opening it means the
reservoir tank is full. SHUT WATER OFF. Open all valves to process and start chiller for about 15 seconds to fill lines and
equipment. STOP CHILLER. Open city water again at a SLOW RATE till water again comes out of the vent pipe. SHUT THE
WATER OFF. The system is full and ready for use.
I. SHUT DOWN
1.
Equipment which will not be required to operate for a period of time should be secured by storing refrigerant charge in the
receiver or condenser. On units with coolers or water cooled condensers, special precautions must be taken to completely drain
the vessels to prevent freezing if ambient should be below 32*F.
2.
Inspect system for possible worn or faulty components and repair if required.
J. SYSTEM RESTART AFTER SHUT DOWN
1.
Thorough leak test should be performed.
2.
Coil(s) should be checked for dirt accumulation or obstruction and cleaning if necessary.
3.
Refill water system and purge all air from system.
4.
Energize crankcase heaters and allow a minimum of 12 hours operation before compressor restart.
5.
Install gauges, start system and check for correct refrigerant charge, and proper system operation and balance.
K. MAINTENANCE
1.
The system should be checked periodically. Use only the services of an EPA qualified refrigeration technician for inspection and
maintenance checks or service operations.
2.
Water Treatment (Chillers and Water Cooled Condensing Units) – The water should be tested by a local testing agency and their
recommendations adhered to.
3.
Air Cooled Condenser – The inlet side of the condenser coil must be kept clean through a regular prevention maintenance
program. ]
4.
Periodically checks all electrical connections for possible loose or corroded terminals. Repair as necessary.