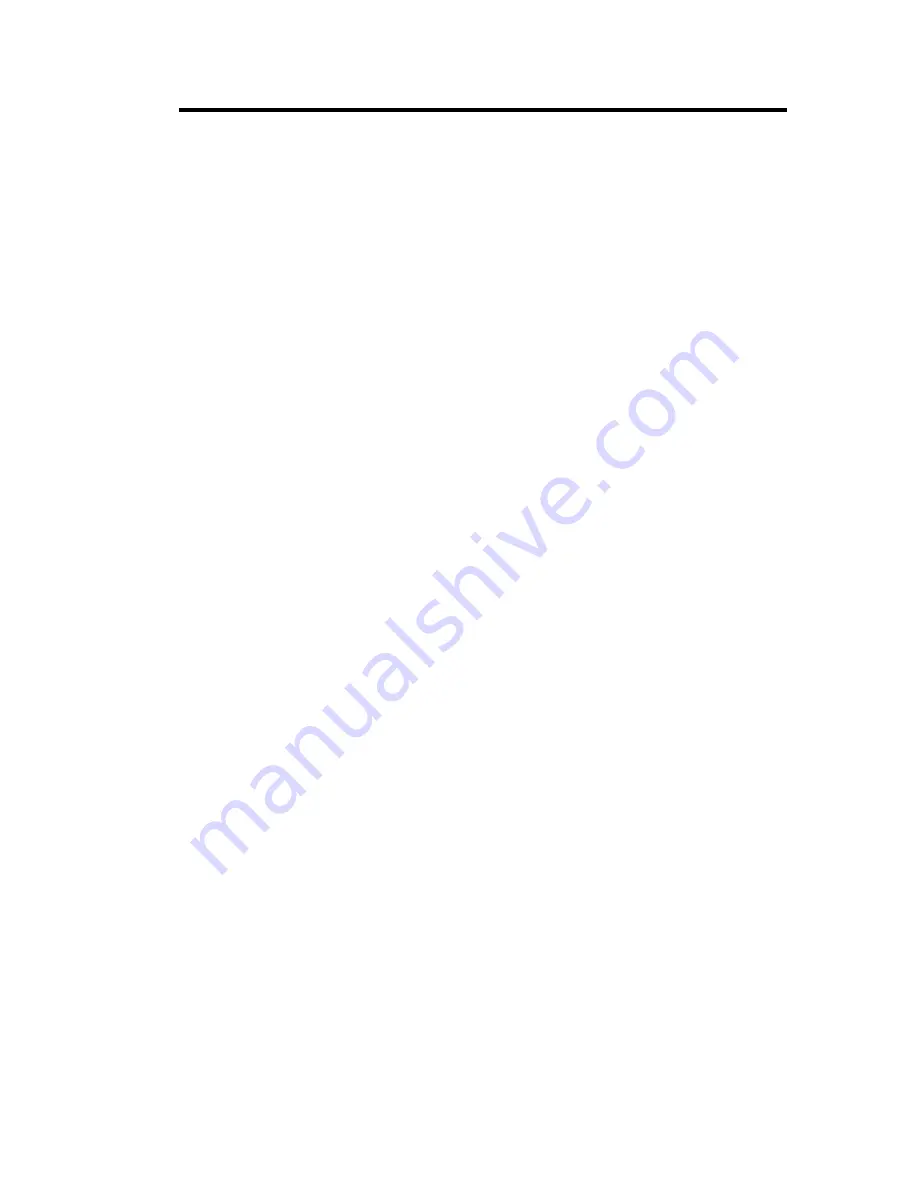
Infinity REU-V3232W /HD250E REU-V3232WC
- 17 -
Issue 1 - 8/09/03 ©Rinnai
10. Main Components
1) Printer Circuit Board
• The Printed Circuit Board controls all operational functions including Air Supply Control, Gas Control,
Water Flow Measurement, Water Flow Control, Combustion System and all sensors and safety devices.
2) Gas Flow Control
• During normal operation, the PCB keeps the main solenoid valve open whilst there is flow through the
unit and the burner needs to be lit.
• Gas flow rate is controlled by the modulating valve assembly and three changeover solenoid valves to
always ensure constant outlet water temperature, regardless of flow rate or incoming water temperature.
• The modulating valve is electronically controlled by the PCB using signals from the water flow sensor,
water flow control device, bypass flow control device, water temperature thermistors and combustion
fan speed sensor. The modulating valve directs gas to the three changeover solenoid valves.
• The three changeover solenoid valves direct gas to each of the three burner banks independantly. Any
one, two or all of the solenoid valves may be open during operation.
• Gas flow is modulated between 20 and 250MJ/hr by a combination of the modulating valve and
changeover solenoid positions.
• The maximum gas rate is predetermined and the appliance cannot be overloaded when correctly
installed.
3) Water Flow Control
• Water flow is detected by a turbine coupled to a magnetic pulse generating device. The magnetic pulses
are detected and counted by the PCB. The PCB calculates the exact water flow from the frequency of
pulses generated by the turbine, as well as the volume of water that has passed through the unit at any
instant during ‘Bath Fill’ operation. A minimum flow rate of 2.7l/min. is required for the burner to
ignite.
• Water flow control is achieved through the use of servo driven water flow and bypass valves. Both servo
motors are controlled by the PCB. The ‘Water Flow Valve’ restricts the flow of water into the heat
exchanger assembly if the programmed temperature cannot be achieved. Also, when the Bath Fill
function is activated, flow of water is stopped when the bath is full. During normal operation, cold water
from the inlet valve is mixed with hot water from the heat exchanger outlet. The ‘Bypass Valve’ mixes
the correct proportion of cold and hot water to ensure accurate hot water delivery temperature over the
available range of flow rates. The water flow and bypass valves are a combined assembly on the cold
water inlet of the appliance.
4) Air Supply Control
• Air for combustion is supplied by a centrifugal fan driven by a variable speed DC motor. The voltage to
the motor is determined by the PCB based on water flow, delivered water temperature and programmed
water temperature. The actual fan speed is monitored by a magnetic pulse counter. This counter emits a
signal to the PCB. From the voltage supplied to the DC motor and the fan speed signal, the PCB
determines whether an error condition exists with the fan.
5) Combustion System
The combustion chamber is housed within the heat exchanger assembly and comprises:
• A three chamber aluminium alloy manifold with a total of 44 integral injectors, arranged in two rows of
twenty two. The middle chamber houses eight injectors, the left chamber, twelve, and the right chamber,
twenty four injectors. Gas flow to each chamber is controlled by an electronic solenoid valve (refer ‘Gas
Flow Control’ above).
• A burner assembly comprising twenty two identical modular stainless steel bunsen burners secured by
an aluminised steel framework. The manifold is attached to the front of the burner module. Each bunsen
burner is supplied by two injectors.
• A combustion chamber. Integrated into the combustion chamber front panel are the flame rod and two
ignition electrodes.
Summary of Contents for HD250E REU-V3232WC
Page 12: ...Infinity REU V3232W HD250E REU V3232WC 7 Issue 1 8 09 03 Rinnai 4 Dimensions...
Page 18: ...Infinity REU V3232W HD250E REU V3232WC 13 Issue 1 8 09 03 Rinnai 7 Cutaway Diagram...
Page 24: ...Infinity REU V3232W HD250E REU V3232WC 19 Issue 1 8 09 03 Rinnai 12 Wiring Diagram...
Page 54: ...Infinity REU V3232W HD250E REU V3232WC 49 Issue 1 8 09 03 Rinnai 21 Exploded Diagram...
Page 55: ...Infinity REU V3232W HD250E REU V3232WC 50 Issue 1 8 09 03 Rinnai...
Page 56: ...Infinity REU V3232W HD250E REU V3232WC 51 Issue 1 8 09 03 Rinnai...
Page 57: ...Infinity REU V3232W HD250E REU V3232WC 52 Issue 1 8 09 03 Rinnai...
Page 61: ...Infinity REU V3232W HD250E REU V3232WC 56 Issue 1 8 09 03 Rinnai Notes...